www.ptreview.co.uk
14
'24
Written on Modified on
Digital Compressed Air Monitoring “cuts costs by up to 30 percent”
SICK has unveiled a pioneering compressed air monitoring system that accurately predicts where significant energy cost-savings can be made by fixing air leaks and removing wastage across entire production and logistics facilities.
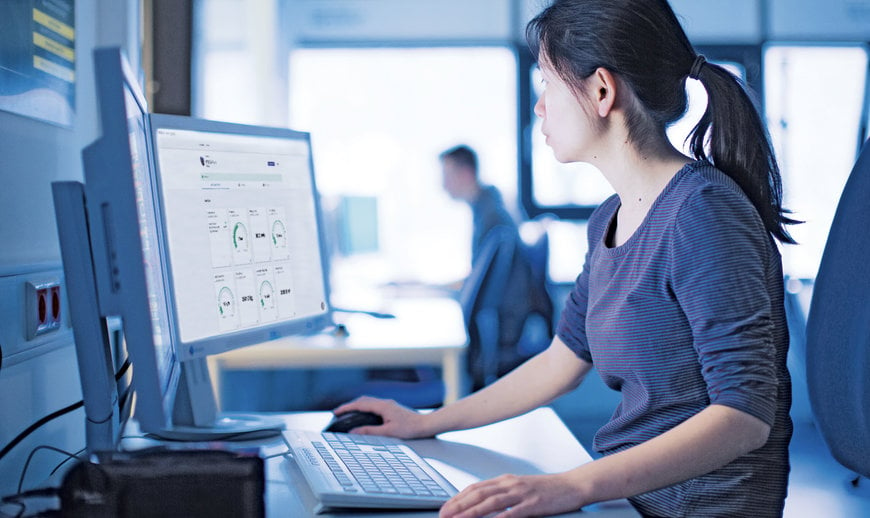
SICK’s Monitoring Box FTMg Premium is a digital and scalable service that can be used by production planners, energy managers and maintenance engineers to make compressed air cost savings of up to 30%, as well as to eliminate costly manual maintenance regimes.
The enhanced digital Monitoring Box Premium service analyses and displays accurate data from SICK’s FTMg multifunctional flow sensors that measure the compressed air usage of machines and processes. Compressed air consumption data is visualised in easy-to-use graphic displays, while alarms can be set up to alert when new leaks occur.
By interpreting the data, leaks and inefficiencies are easily eliminated, users understand their processes better and can make around-the-clock decisions to optimise their energy usage. They can make their production processes more sustainable, for example by reducing their CO2 consumption. The data insights also contribute towards ISO50001 Energy Management certification.
Expensive Resource
Compressed air is one of the most expensive resources used in production, and energy prices have risen sharply. Identifying and correcting leaks is a time-consuming and labour-intensive process of routine checks that can still only ever identify leaks at one fixed point in time. Charlie Walker, Digital Solutions Consultant with SICK UK, explains:
“Even if you walk around the factory today and identify and fix all your leaks, tomorrow there might be three more you will not have found. Now you can drill down using precise real-time data to discover exactly when, and where, you are producing air and wasting it. The system will tell you how much wastage is going on, and what that’s worth in real money. So, you know when to take action.
“Ultimately compressed-air costs could be reduced by up to 30% delivering a significant Return on Investment, while reducing your CO2 footprint and making servicing both more efficient and effective.”
Enhanced Digital Service
Already, the Monitoring Box FTMg Premium is being used successfully by SICK customers who have welcomed the easy-to-use data visualisation and scalability of the system. They have been able to set up specific alarms to indicate leaks or inefficient machine consumption. By comparing compressed air data from each measuring point, machine, and production line, cost drivers or over-consumption have been identified, for example, by comparing a machine type with the same function on two production lines. Compressed air efficiency comparisons can similarly be made across plants.

The SICK FTMg which stands for Flow Thermal Meter for inert gases, uses the dynamic calorimetric principle for precision measurement, enabling it to detect even the smallest changes reliably. Its straight measurement channel design ensures highly-accurate measurement with almost zero pressure loss as gases flow through the sensor during measurement.
The SICK FTMg enables measurement of live values for compressed air energy in kWh. Data from the FTMg flow meter is presented via the SICK FTMg Monitoring App, which has been developed from SICK’s proven Industry 4.0 Monitoring Box condition monitoring platform. As well as values for pressure, temperature, flow velocity, mass flow rate and volumetric flow rate in real time, the sensor provides totals for energy use, volume and mass over a pre-defined period.
The user-friendly dashboard makes it easy to interpret data to detect leaks or overconsumption and to look for changes and trends. Email alerts can be set up for maintenance reminders or to give pre-defined warnings with job recommendations, for example when data strays beyond pre-defined limits. Users can drill down to identify costs, for example for individual production centres or by shift.
‘Bolt-on’ Transparency
Up to eight FTMg flow meters can be configured via each SICK Smart Services Gateway, which collects data, aggregates and encrypts it before sending it securely via the customer’s own IT infrastructure through a firewall to the SICK cloud. Alternatively, it is possible to by-pass the IT infrastructure by using mobile communications over 4G. Individuals then have access through a personal SICK ID from any device with a web browser.
www.sick.com