www.ptreview.co.uk
07
'23
Written on Modified on
SCHUNK PRESENTS USER-FRIENDLY CMS MANUAL CHANGING SYSTEM
As well as simple and convenient operation, the extensive range of optional modules and complementary end effectors is also impressive with the CMS.
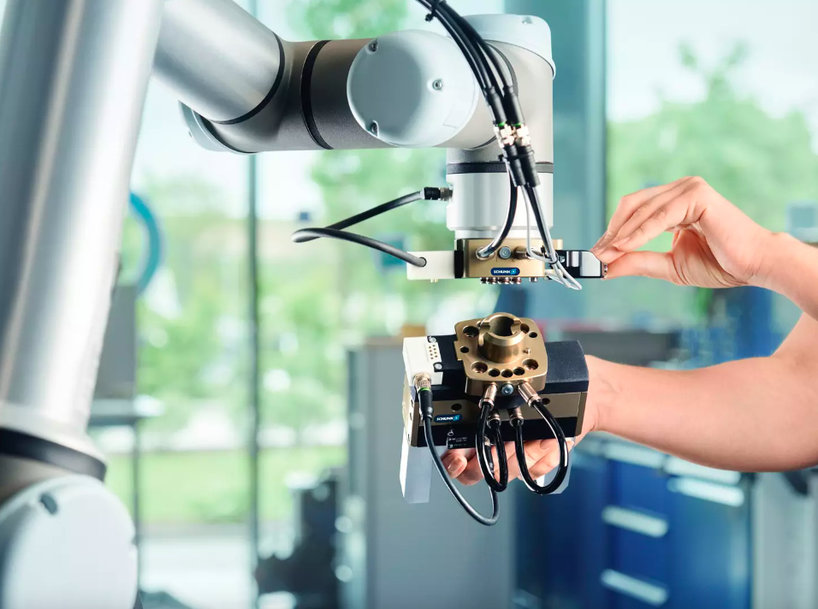
The user-friendly CMS manual changing system can be locked or unlocked easily and conveniently without the use of any additional tools.
The new CMS manual change system from SCHUNK is the optimal addition for flexible tasks in manufacturing, handling technology or at assembly workstations. It enables rapid, process-reliable changeover at the robot front end or also on stationary systems such as in fixture construction. The manually operated system consists of a CMS-K interchangeable head and a CMS-A interchangeable adapter and can handle payloads of up to 58 kg. It can be flexibly combined with handling or machining components from the extensive SCHUNK portfolio - from grippers to machining tools from the R-EMENDO series, for example for automated deburring, polishing or filing.
The CMS is the further development of the SHS changing system, which is already an established part of the SCHUNK portfolio and can replace it 1:1 due to its having the same height and screw-on patterns. The successor version now offers decisive optimizations in terms of operation, design, process reliability and usage options.
Fast and process-reliable changing
Tried-and-tested push lever technology makes the operation of the CMS extremely simple and convenient. The interchangeable head can be locked by hand with the interchangeable adapter without the use of any additional tools. Innovative, integrated air feed-throughs via sealing pins with cylinder seals support manual locking so that only minimal force is required for this process. In addition, the thrust lever has a new, cranked shape that does not conceal any of the numerous connections. This means that all system connections can now also be used radially.
More operational safety is provided by a spring-loaded latching pin that fixes the hand lever to the housing and prevents the system from opening during operation. The integrated monitoring sensor system, which enables inductive monitoring of interlock status and mould presence with optional sensors, provides additional operating safety and a plus in process reliability. Thanks to the ISO flange pattern, the CMS can be mounted on all common robot types without an additional adapter plate.
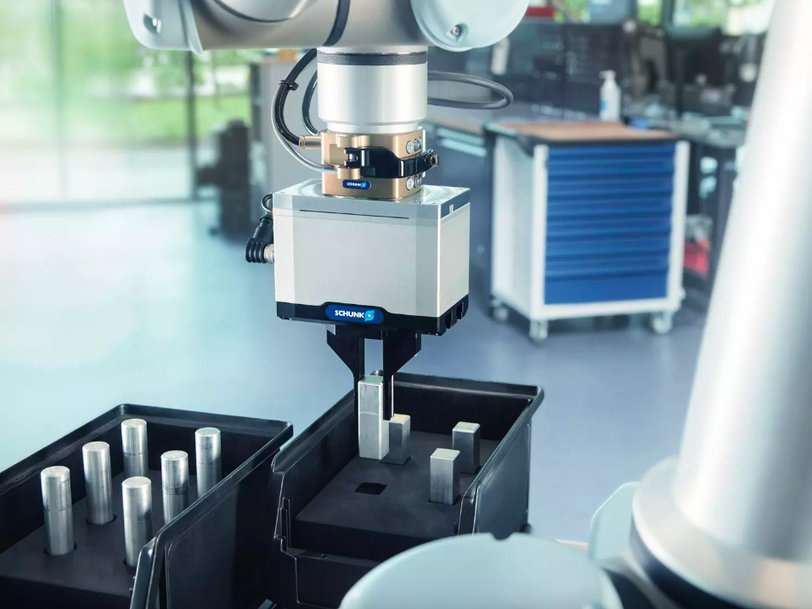
For flexible parts handling in machine loading: With the CMS changing system, appropriate end effectors can be exchanged easily as needed - in this case the electric universal gripper EGU.
Wide range of optional modules and end effectors
A wide variety of end effectors such as gripper or machining tools can be supplied via integrated pneumatic feed-throughs or a vacuum. In addition, energy supply is now also possible via directly bolted-on electrical, pneumatic and fluid modules, saving both space and weight. Alternatively, SCHUNK also offers a lower-price, identically constructed basic variant CMS-B without pneumatic feed-throughs.
The CMS manual change system is available in six sizes from 40 to 125. In addition to a wide range of combination and application options, users benefit from the breadth of knowledge about applications of the full-range automation supplier.
www.schunk.com
The new CMS manual change system from SCHUNK is the optimal addition for flexible tasks in manufacturing, handling technology or at assembly workstations. It enables rapid, process-reliable changeover at the robot front end or also on stationary systems such as in fixture construction. The manually operated system consists of a CMS-K interchangeable head and a CMS-A interchangeable adapter and can handle payloads of up to 58 kg. It can be flexibly combined with handling or machining components from the extensive SCHUNK portfolio - from grippers to machining tools from the R-EMENDO series, for example for automated deburring, polishing or filing.
The CMS is the further development of the SHS changing system, which is already an established part of the SCHUNK portfolio and can replace it 1:1 due to its having the same height and screw-on patterns. The successor version now offers decisive optimizations in terms of operation, design, process reliability and usage options.
Fast and process-reliable changing
Tried-and-tested push lever technology makes the operation of the CMS extremely simple and convenient. The interchangeable head can be locked by hand with the interchangeable adapter without the use of any additional tools. Innovative, integrated air feed-throughs via sealing pins with cylinder seals support manual locking so that only minimal force is required for this process. In addition, the thrust lever has a new, cranked shape that does not conceal any of the numerous connections. This means that all system connections can now also be used radially.
More operational safety is provided by a spring-loaded latching pin that fixes the hand lever to the housing and prevents the system from opening during operation. The integrated monitoring sensor system, which enables inductive monitoring of interlock status and mould presence with optional sensors, provides additional operating safety and a plus in process reliability. Thanks to the ISO flange pattern, the CMS can be mounted on all common robot types without an additional adapter plate.
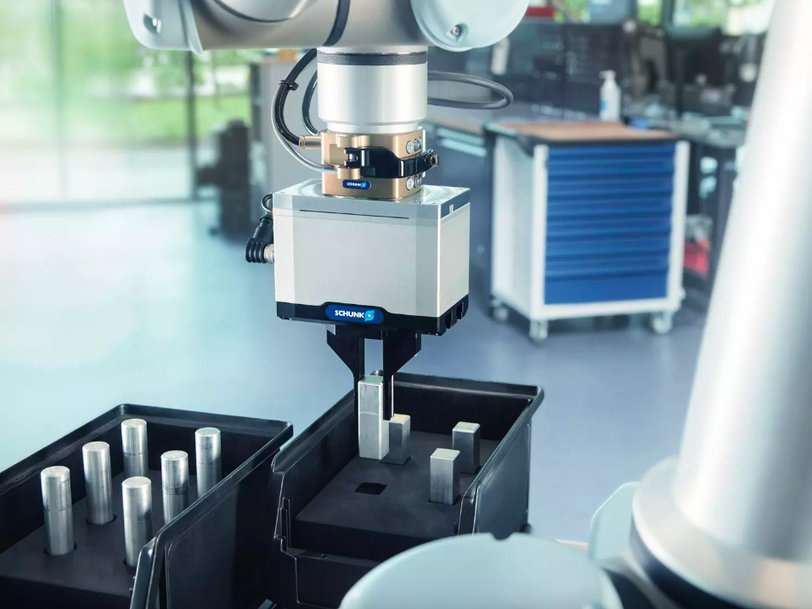
For flexible parts handling in machine loading: With the CMS changing system, appropriate end effectors can be exchanged easily as needed - in this case the electric universal gripper EGU.
Wide range of optional modules and end effectors
A wide variety of end effectors such as gripper or machining tools can be supplied via integrated pneumatic feed-throughs or a vacuum. In addition, energy supply is now also possible via directly bolted-on electrical, pneumatic and fluid modules, saving both space and weight. Alternatively, SCHUNK also offers a lower-price, identically constructed basic variant CMS-B without pneumatic feed-throughs.
The CMS manual change system is available in six sizes from 40 to 125. In addition to a wide range of combination and application options, users benefit from the breadth of knowledge about applications of the full-range automation supplier.