www.ptreview.co.uk
04
'23
Written on Modified on
SWAP-IT BY FRAUNHOFER IS AN INNOVATIVE PRODUCTION ARCHITECTURE FOR THE FACTORY OF THE FUTURE
Researchers at the Fraunhofer-Gesellschaft have developed an innovative production architecture, where orders are issued in a newly developed production language and carried out autonomously by machine tools or robots.
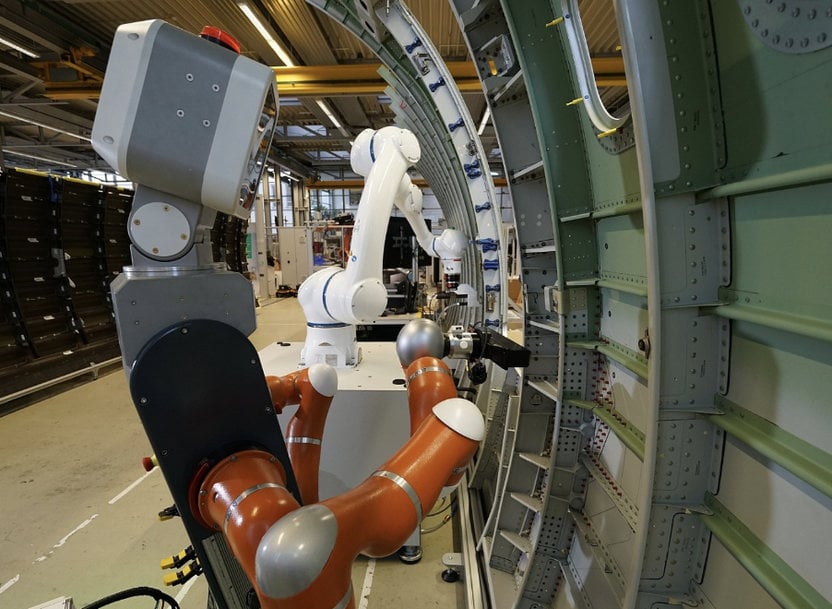
Conventional concepts from the manufacturing industry are increasingly being pushed to their limits. This is often due to a combination of current challenges like volatile markets, supply crises and rising energy prices. Researchers at the Fraunhofer-Gesellschaft have developed an innovative production architecture that addresses these challenges. This architecture relies on modular production rather than rigid process chains. Orders are issued in a newly developed production language and carried out autonomously by machine tools or robots. This way, manufacturers can adapt processes on the factory floor flexibly to suit their targets. The Fraunhofer institutes will be presenting their production architecture at the Hannover Messe 2023 from April 17 to 21, at the Fraunhofer booth (Hall 16, Booth A12).
Ongoing crises and rising costs pose enormous challenges for the manufacturing industry. Businesses often need to produce large quantities of top-quality products or deliver tailored individual products or small batches on request. Energy efficiency and sustainability are also growing in importance in production, requiring extensive retrofitting. Conventional production environments are typically characterized by rigid process chains. Such architectures are inadequately prepared to meet all these requirements, even though the digital transformation of the last few years has resulted in some modernization.
Ten Fraunhofer institutes in the Fraunhofer Groups for Production, Light & Surfaces and ICT are presenting a solution to this problem in the lighthouse project SWAP. The concept behind SWAP points to “heterogeneous, workload-optimized robot teams and production architectures.” The “SWAP-IT” architecture is designed to establish a scalable, and lean, cyberphysical production system suitable for a variety of production processes.
Thanks to its modular structure, the SWAP-IT production architecture breaks up the static structures and schematic processes of conventional production facilities. Instead, it supports individual planning and order assignment for the individual production steps. A uniform and semantically simplified description language for machines, processes, and products enables the integration of resources like machines, robots, or automated guided vehicle systems – resulting in a smart and adaptable production environment.
The description language defines the order
A key element of SWAP-IT is the “PFDL” (Production Flow Description Language), developed by Fraunhofer researchers for the project. It incorporates both the manufactured product and the machinery required to manufacture it. The PFDL is used to define the finished product or component before manufacturing begins, and then add the desired special features. “Take the example of a car door. The first step is to describe the basic dimensions or geometry of the door, followed by its individual properties, such as the paintwork or tinting of the windows. To simplify the process, the PFDL can load a CAD model, which only needs to be customized," explains Peter Detzner, expert in cyberphysical production systems and research fellow at the Fraunhofer Institute for Material Flow and Logistics IML.
As a result, a set of orders can be implemented autonomously by an order-centric production system. Every production step of the order is implemented through the machine interface, simply by calling the services provided by the respective machine. Once completed, the required machine tools and robots can begin to work in a targeted way. There is a crucial advantage in this: Because the PFDL sets out the sequence of production steps in principle but does not specify which particular machine will carry out each task, the SWAP-IT software incorporates the flexibility to exchange the assigned machines based on availability, costs or location during operation. The production system furthermore considers many different factors such as the current status of the systems, the duration of each task or previous tasks and the costs incurred by running the machine. It is only logical, that the name SWAP-IT alludes to the possible swap in production steps or machinery.
This allows each order to be executed efficiently and adapted individually to the requirements. Conventional manufacturing, with its standardized workstations, cannot achieve the same case-by-case flexibility.
“The long-term vision is that, once an order has been issued to build a car, for example, machines and robot systems can work on the car’s components as a well-organized team. The same applies to other sectors, such as the optical or aircraft construction industry,” explains Niels Schmidtke, project manager and head of the central office of the Fraunhofer Group for Production.
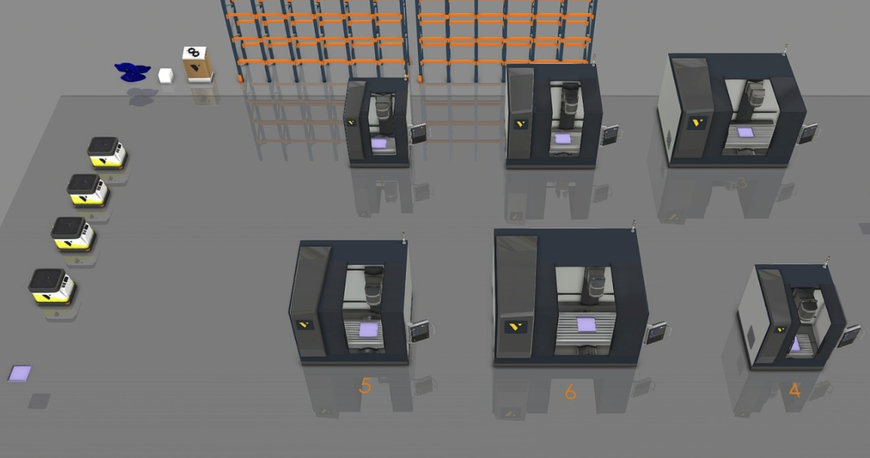
The SWAP-IT production system decides how an order will be carried out and allocates the tasks to available machines or robots.
Individual targets for each production order
“Employees can also incorporate targets into the PFDL order. They can specify that the manufacturing needs to be particularly energy-efficient or rapid or make the greatest possible use of the available system and machine capacity,” explains Andreas Ebner, expert in cognitive industrial systems at the Fraunhofer Institute for Optronics, System Technologies and Image Exploitation IOSB. These targets can be changed at any time. If there is an unexpected peak in order volumes, employees can, for example, require the system to speed up production even if this leads to higher energy costs. This way, production can easily respond to follow-up orders or changes to product characteristics when a new product version is to be released.
The SWAP-IT production architecture can also allocate the production of a particularly large component to multiple machines. For example, the production of a large molding tool for the side panel of a car can be segmented and distributed to several smaller machines, each of which manufactures just one segment of the tool. The segments can be assembled afterwards. This method allows the factory floor to use small, less expensive machines instead of costly machines with low availability.
A logical extension of Industry 4.0
The Industry 4.0 megatrend has seen technologies such as sensors, networking and digital twins make their way onto the factory floor. The lighthouse project SWAP continues this trend. “These technologies gather information on what happens on the shop floor and make this information available. SWAP-IT uses the data to free production from rigid processes. It’s the next logical step,” explains Detzner.
Although it may seem that SWAP-IT leads to complex structures and long familiarization times, it is easily manageable in practice. When developing the PFDL description language and designing SWAP-IT, the experts at Fraunhofer prioritized reducing complexity as much as possible. When implemented on the shop floor, the PFDL vocabulary is tailored to the individual usage scenario. “This way, we reach the perfect compromise between maximum flexibility and a streamlined system,” explains Ebner. The researchers are also working on a hands-on approach to implementing SWAP-IT that makes it easier for businesses to switch to the innovative production architecture.
www.fraunhofer.com