www.ptreview.co.uk
15
'21
Written on Modified on
Planning for the unplanned
Turning downtime into uptime.
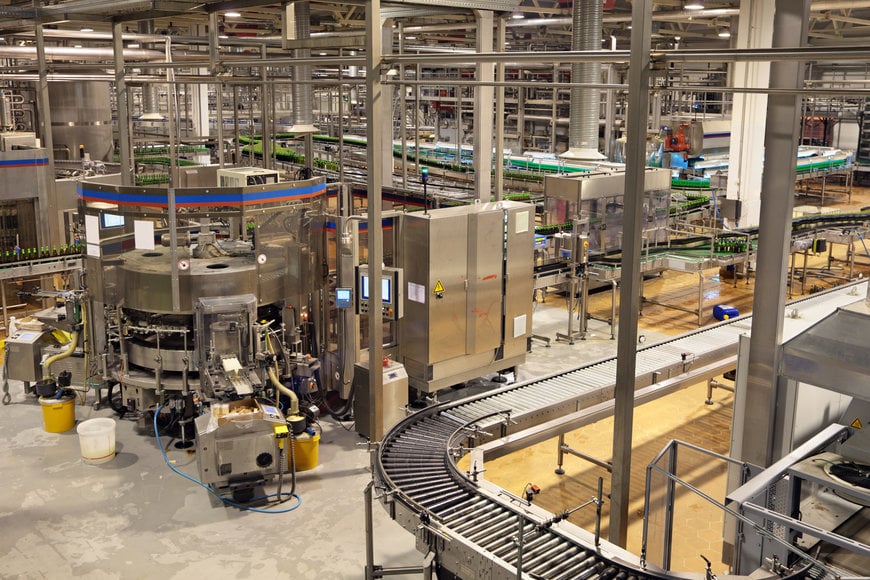
Unplanned downtime is an unfortunate fact of any industry. Nobody can see the future, after all. Your production line might stop for a variety of reasons, but no matter the problem, the emphasis is getting things going again. Here Neil Ballinger, head of EMEA sales at industrial automation specialist EU Automation, discusses the problems unplanned downtime causes, and how to avoid it.
Studies suggest that every minute that an automotive manufacturing plant experiences downtime costs the factory $22,000. When this fact is combined with other studies suggesting each company experiences an average of 800 hours of downtime per year, it’s clear to see that downtime costs quickly grow out of control.
While automotive might be on the higher end of the scale, every industry suffers when production halts. However, just because downtime might be unplanned, that doesn’t mean plans can’t be made for when things happen.
Lights out
There is one style of failure that cannot be easily mitigated against — general power failure. Most industrial processes will cease without power, halting the production line. Sudden or unpredictable power fluctuations can also damage equipment, as well as possibly leaving process equipment in unsafe states.
The obvious answer to this problem is to have banks of backup generators ready to spin up when external power fails. A working fix for most industries, but backup power systems can be prohibitively expensive, impractical or possibly unworkable depending on the power needs and other specifics of the industry in question.
An industrial bakery, for instance, might benefit from backup power to keep the conveyors running until product is moved out of the ovens. Any product left mid-process could pose fire risks or hygienic problems while the conveyor is inoperable. Alternatively, a cold vegetable production line would be far less likely to cause knock-on problems.
Planning and installing a backup power system might be worth it, or not, depending on the specifics of production you perform. It doesn’t have to keep things running in perpetuity — just long enough to make things safe.
Changing trends
Things like the weather and power outages cannot be reliably predicted, and neither, sadly, can customer orders. When orders dry up, production lines stop — a fact made clear by the recent pandemic.
For some industries this is a bitter pill that they must withstand, but for others the option to switch over to a new product might be available.
Switching production to a new product when using traditional manufacturing techniques can take weeks or even months. The part must be designed, prototyped and tested before moulds and tooling parts can be created for their manufacture, on a specially designed production line.
Businesses often talk about updating their processes with new production methods, with two in five surveyed suggesting their use of 3d printing alone will quintuple over the next two to five years.
3d printing, and other computer aided production methods, can completely skip the prototyping steps, as well as mould production or other product specific tooling. A product can be easily designed on a computer and a working prototype printed in minutes.
Breaking down
The previous two downtime modes are unpredictable, but not explicitly damaging. Breakdowns definitely are, and are therefore the most detrimental.
Physical wear and tear, leading to breakdowns, is an unfortunate, unavoidable fact of life. Things wear out and break, but with a bit of forward planning the damage can be limited, or even eliminated.
The ideal way of dealing with unpredictable breakdowns is to do everything possible to make them predictable. This is achieved with supervisory control and data acquisition (SCADA) systems, which watch for anything going wrong and flag events that exceed parameters.
More recent developments in machine learning algorithms are allowing the latest SCADA systems to be predictive. The machine learning algorithms watch normal operation to discover the warning signs that precede failures. For a motor the warning sign might be an increase in back EMF implying misaligned poles, or for a sewage pipe a cyclical flow rate might imply faulty valves. Spotting these subtle tells and patterns between them, which a human may never, means that maintenance can be planned to cause the least amount of disruption.
All that said, what are you supposed to do after something breaks? Even with a perfect SCADA system, human error and mistakes are another fact of life. Sometimes you need a spare part. Fast.
That’s where working closely with suppliers is the key. Well placed suppliers, such as us here at EU Automation, have the knowledge and ability to pick new, refurbished and even obsolete original equipment manufactured parts and get them to where they’re needed as fast as possible.
It’s in nobody’s interest to spend hours, or even days, searching for a spare part when production is halted. You’ll not get a rebate for the $22,000 a minute it might cost you, after all, so it pays to plan ahead.
www.euautomation.com