www.ptreview.co.uk
15
'24
Written on Modified on
Robot.work automation solution for IMA Schelling's cut-to-size saws
By equipping the fh4 cut-to-size saw or its big sister the fh5 with an industrial robot, cutting patterns can be processed fully automatically.
www.imaschelling.com
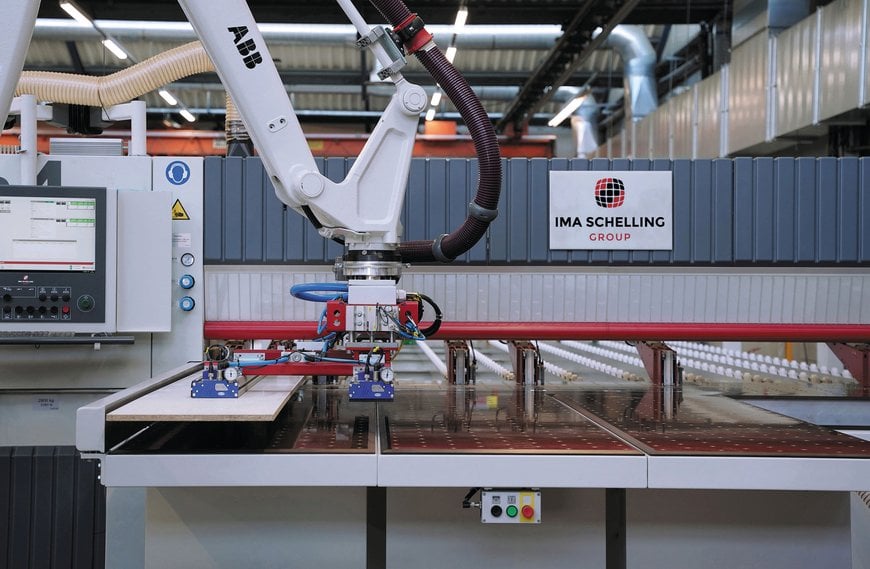
The Robot.work robot solution from IMA Schelling enables the automatic operation of the manufacturer's fh4 and fh5 cut-to-size saws. This combination increases productivity and frees up personnel for more value-adding activities. Robot.work allows fully automatic handling of strips, components and remnants, while IMA Schelling's intelligent stacking algorithm delivers the most stable stacking patterns.
The fh4 cut-to-size saw is designed for demanding carpentry work and entry into industrial production, as it can process between 500 and 800 parts per shift. It combines precision with perfect cutting guidance and optimised workflows, while also guaranteeing high productivity. A saw motor with an output of 18 kW even allows for effortless processing of unusual wood board types. The HPO cutting pattern optimisation software and XBoB remnants management system ensure that not even one millimetre of material is used unnecessarily. This conserves resources and saves on material costs.
IMA Schelling supplies the Robot.work automation solution as the perfect introduction to automated cut-to-size plants. By equipping the fh4 cut-to-size saw or its big sister the fh5 with an industrial robot, cutting patterns can be processed fully automatically. "Production can take place unstaffed over long distances," explains Jan Frederik Bode, Product Manager Robotics. He adds: "Employees can therefore focus on more value-adding activities."
Highly flexible processing solution
Robot.work is suitable for use with chaotic stacking on up to three double euro pallets or in an interlinked system. This means that customers benefit from a high degree of flexibility, because it is easy to switch between manual and automatic operation, for example. Furthermore, Robot.work can be readily retrofitted. "This is an option that no other provider on the market offers," explains Jan Frederik Bode. "It means that our customers can automate their production process in stages and do not have to commit to a large investment all at once," he concludes.
Better plant utilisation thanks to smart stack formation
The robot picks up the cut strips and finished parts, turns them for further processing and removes them again. The finished parts can be transported further along a straight or angled chain or stacked on pallets on the ground. No additional equipment is needed, ensuring that the room and the saw remains threshold-free.
At the same time, the IMA Schelling stacking algorithm ensures optimum plant utilisation and occupational safety. The software module performs advance calculation for a cutting pattern or order to determine how the workpieces can be stacked to form a unit, while a physics engine assesses the stability of the stacks. This reduces space requirements and stack changeover times. In addition, use of the plant improves the traceability of individual workpieces and establishes data consistency across the entire machining process.
A special feature of the system is that the stacking algorithm not only calculates in advance, but also during operation, which means that if, for example, a board is accidentally damaged during processing and has to be ejected, the algorithm regenerates the stack during the ongoing machining cycle.
The fh4 cut-to-size saw is designed for demanding carpentry work and entry into industrial production, as it can process between 500 and 800 parts per shift. It combines precision with perfect cutting guidance and optimised workflows, while also guaranteeing high productivity. A saw motor with an output of 18 kW even allows for effortless processing of unusual wood board types. The HPO cutting pattern optimisation software and XBoB remnants management system ensure that not even one millimetre of material is used unnecessarily. This conserves resources and saves on material costs.
IMA Schelling supplies the Robot.work automation solution as the perfect introduction to automated cut-to-size plants. By equipping the fh4 cut-to-size saw or its big sister the fh5 with an industrial robot, cutting patterns can be processed fully automatically. "Production can take place unstaffed over long distances," explains Jan Frederik Bode, Product Manager Robotics. He adds: "Employees can therefore focus on more value-adding activities."
Highly flexible processing solution
Robot.work is suitable for use with chaotic stacking on up to three double euro pallets or in an interlinked system. This means that customers benefit from a high degree of flexibility, because it is easy to switch between manual and automatic operation, for example. Furthermore, Robot.work can be readily retrofitted. "This is an option that no other provider on the market offers," explains Jan Frederik Bode. "It means that our customers can automate their production process in stages and do not have to commit to a large investment all at once," he concludes.
Better plant utilisation thanks to smart stack formation
The robot picks up the cut strips and finished parts, turns them for further processing and removes them again. The finished parts can be transported further along a straight or angled chain or stacked on pallets on the ground. No additional equipment is needed, ensuring that the room and the saw remains threshold-free.
At the same time, the IMA Schelling stacking algorithm ensures optimum plant utilisation and occupational safety. The software module performs advance calculation for a cutting pattern or order to determine how the workpieces can be stacked to form a unit, while a physics engine assesses the stability of the stacks. This reduces space requirements and stack changeover times. In addition, use of the plant improves the traceability of individual workpieces and establishes data consistency across the entire machining process.
A special feature of the system is that the stacking algorithm not only calculates in advance, but also during operation, which means that if, for example, a board is accidentally damaged during processing and has to be ejected, the algorithm regenerates the stack during the ongoing machining cycle.
www.imaschelling.com