www.ptreview.co.uk
01
'24
Written on Modified on
Yamaha: Automating with Robots to Maximise Productivity per Square Metre
While automating processes using robots is a reliable way to increase production throughput and productivity, the savings in floorspace can vary depending on the type of robot chosen, where space is at a premium, a ceiling-mounted orbital robot can offer a suitable solution.
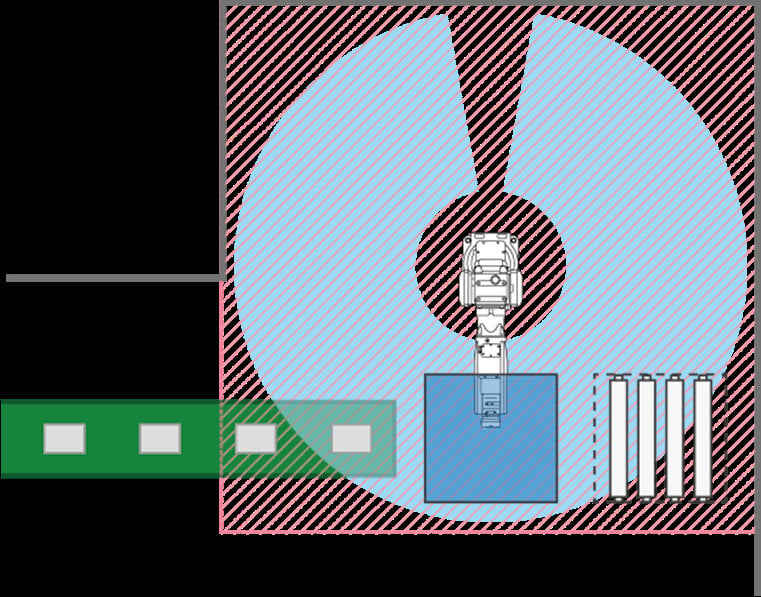
Utilising factory floorspace efficiently is as important to productivity as choosing the best equipment. Like human workers, machines such as pick-and-place robots for tasks including packing and palletising need room to move. A keep-out area may also be required to ensure the safety of any human staff who may be working in the vicinity of the robot. The total working area can be significantly larger than the robot itself, preventing factory floorspace from being used for other purposes.
Where incoming items must be moved from a pallet onto a conveyor, a vertically articulated robot can provide a fast and repeatable solution. These are relatively easy to select, install, and program. A secure base is required and can be large depending on the moving masses and payload. The robot is usually positioned to the side of the work area, far enough from structures such as conveyors to allow the robot to articulate and reach the target positions for picking and placing objects. The size and construction of this is determined according to the moving masses and payload. The complete automation solution, as installed, can occupy a large area as figure 1 illustrates.
After some time, inevitably, factory real-estate needs to be reorganised to introduce new equipment and processes, and as business requirements change. An extra production line may be needed, or more space for storing inventory. Expanding or extending the factory may be practically impossible; moving to larger premises expensive and disruptive. Reclaiming the floorspace around a large, heavy robot can appear an attractive alternative. Indeed, there are some options to consider.
Some robots, such as parallel link machines, are designed to be installed directly above their working area and can liberate the space to the side of a conveyor otherwise occupied by a vertically articulated robot. However, these can be tricky to setup. A strong frame is needed to handle the robot’s weight, and the robot may be tall if a long reach is required. The savings gained can be small, as figure 2 illustrates.
This example shows a parallel link robot which is installed above a pair of conveyors to pick and align randomly positioned workpieces that are moving at a high flow rate. The robot can operate at high speed, and realises a worthwhile saving in floorspace compared to a vertically articulated machine, as the diagram shows. However, an even more economical use of space would be desirable.
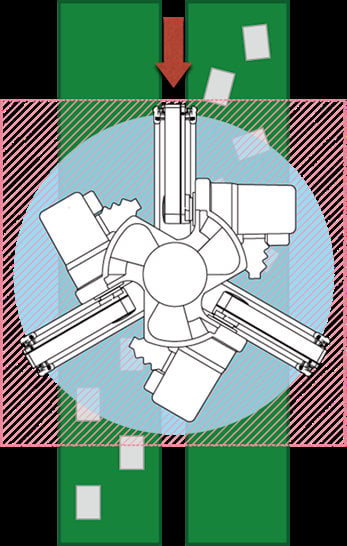
Figure 2. Although the parallel link robot can save floorspace, the total area remains large and the installation can be tall if a long reach is required.
On the other hand, a SCARA robot can allow a smaller footprint, particularly in relation to its load carrying capacity. Choosing a SCARA can deliver other advantages such as easier programming, greater z-axis accuracy, and high speed and acceleration. The example shown in figure 3 illustrates how two SCARA robots can be arranged to pick random items from a single conveyor and place them on separate conveyors according to type. The orange shading shows areas that may be saved if a more space-efficient solution can be found.
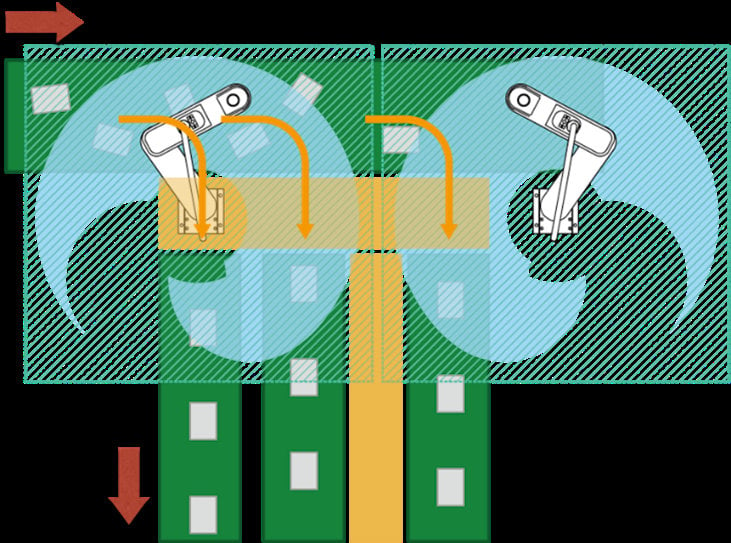
Figure 3. Two conventional SCARA robots can sort and conveyorise at high speed, although some floorspace remains unused.
To achieve the greatest possible savings in floorspace, an orbital SCARA robot may be considered. These can utilise space more efficiently than vertically articulated, parallel link, and conventional SCARA machines. The orbital motion allows access to all points in a circular area beneath the robot and high speed as well as high accuracy are both achieved. The arm movement range can be limited if required, to allow use in extremely small spaces.
When picking items from a pallet, an orbital SCARA mounted directly above the work area as in figure 4 can save much of the space needed to safely install a vertically articulated robot like the example shown in figure 1.
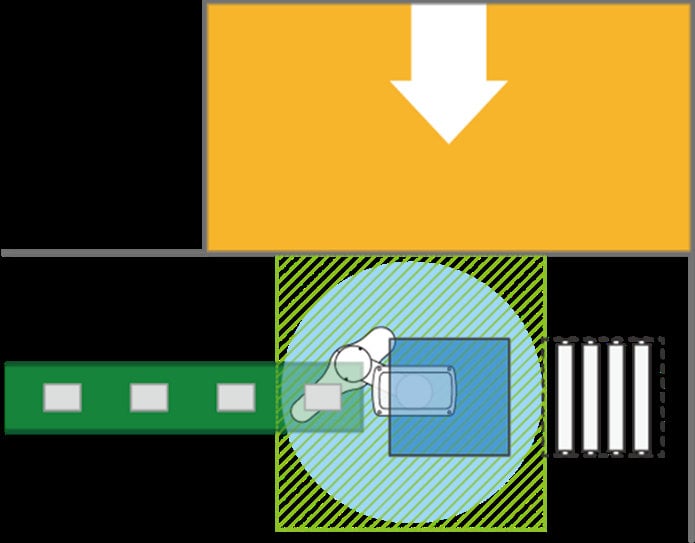
Figure 4. Compact de-palletising automation based on orbital SCARA.
In addition, compared to the parallel link machine used for aligning random items, shown in figure 2, an orbital SCARA can save more space as seen in figure 5.
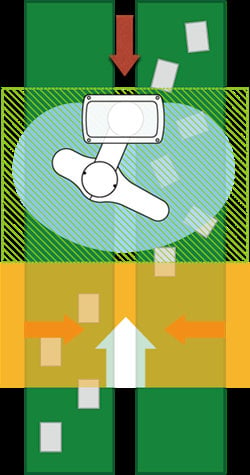
Figure 5. Orbital SCARA saves the orange-shaded area that a parallel link robot would need to perform the same function.
Compared to conventional SCARA robots, a centrally positioned orbital SCARA can do the work of two machines when moving items from one conveyor onto three. The orbital machine occupies considerably less floorspace, as figure 6 shows.
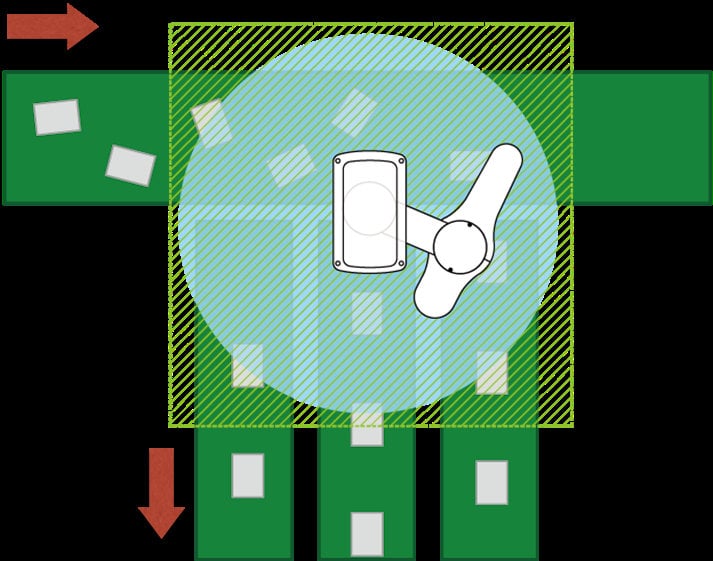
Figure 6. Orbital SCARA for accurately placing randomly positioned items on multiple conveyors.
A system integrator working with Yamaha Robotics found that the YK-TW series orbital SCARA series expanded the company’s opportunities to build more compact solutions to fulfil end-users’ requirements. Choosing a YK-TW model with a payload of 5 kg and a large movement range of φ1,000mm ensured enough reach to pick items from large pallets while occupying a compact overall working area. The chosen model has extremely low height of just 392 mm and weighs just 27 kg. Taking advantage of the properties of this orbital SCARA, the team was able to deliver a uniquely space-efficient solution that led, ultimately, to a winning tender.
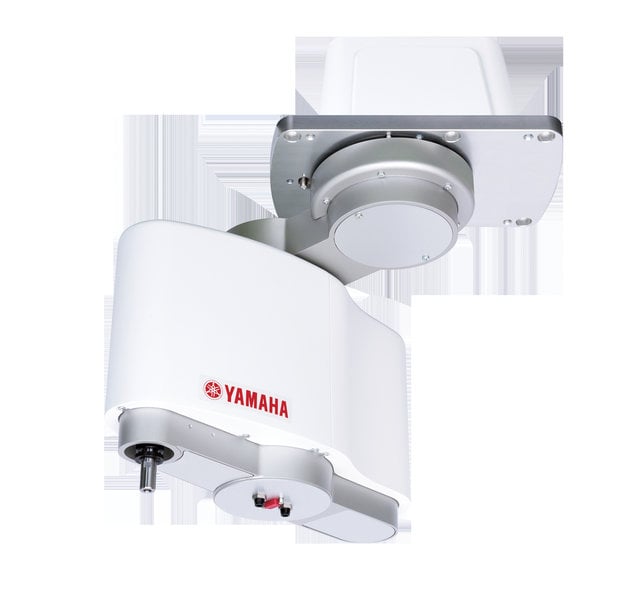
Yamaha YK350TW
As figure 7 shows, the range of motion allows the orbital SCARA to be installed within the area of the conveyor thereby eliminating any need for safety guards. With the conveyor height of 900 mm and the 600 mm total height of the robot mounted on its gantry, the total height of the installation is about 1.5 metres. Assuming a typical human-worker’s height of 1.7 metres, the orbital robot contributes towards a more comfortable environment for people to work in without feeling dominated by large robots.
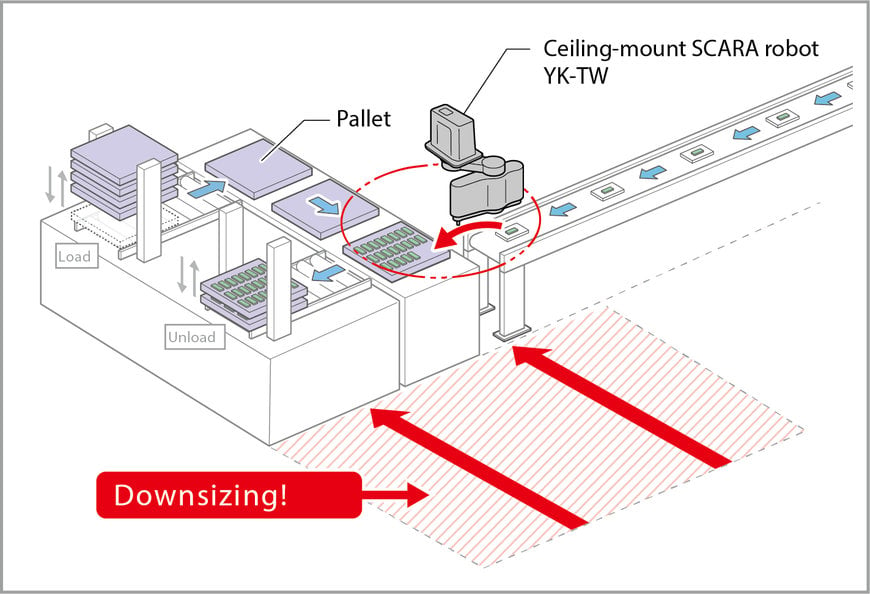
Figure 7. The orbital SCARA saves floorspace, eliminates safety guards, and achieves a low overall height.
In addition, Yamaha can supply a dedicated mounting bracket for YK-TW robots that relieves engineering teams of laborious strength calculations and significantly reduces project development time.
Conclusion
Orbital SCARA robots can help save space in factories and also permit a lower overall equipment height compared to vertically articulated robots as well as other space-saving options such as parallel link and conventional SCARA robots. In projects where saving floorspace has a high priority, orbital SCARA can be operationally efficient and permit a fast project turnaround.
www.yamaha-motor-robotics.com