www.ptreview.co.uk
25
'24
Written on Modified on
STMICROELECTRONICS PRESENTS STSPIN REFERENCE DESIGN FOR SMART ACTUATORS
EVLSPIN32G4-ACT brings together innovation in motor-control systems with data science and its applications to achieve breakthrough performance and ensure sustainable profitability.
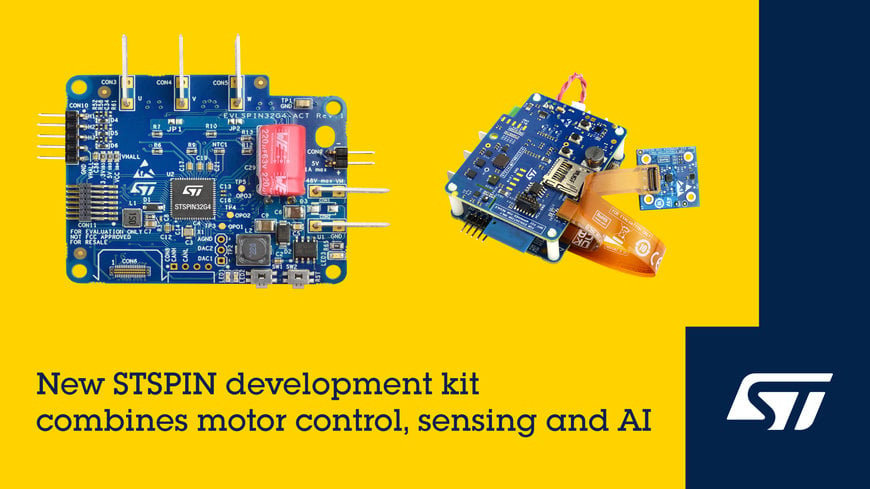
STMicroelectronics is making smart actuators easier to build with the EVLSPIN32G4-ACT edge-AI motor-drive reference design based on the STSPIN32G4 intelligent 3-phase motor driver. The board connects directly with ST’s wireless industrial sensor node, STWIN.box (STEVAL-STWINBX1), to accelerate the development of systems combining motor control, real-time analysis of environmental data, and IoT connectivity.
The high-quality sensors contained in STWIN.box capture information about the status of actuation engines, while high-speed data-logging capabilities help create advanced solutions based on edge AI and machine learning. Mixing environmental and control data shows system engineers exactly how an application is operating, helps identify anomalous conditions, and enables data-driven algorithms to guide troubleshooting and performance optimization.
The STSPIN32G4 on-board combines an intelligent gate driver with power management and the STM32G4 microcontroller (MCU). There is also an inverter stage for 3-phase motors up to 48V/5A and software to connect the sensor module and start building applications. The kit helps users create autonomous mechanisms that respond intelligently to events such as temperature change, barometric pressure, sounds, motion, and ultrasonic signals.
The STSPIN32G4 motor driver enables IoT and IIoT devices to achieve a compact footprint and low power consumption. Applications include factory and building automation systems, servo drives, and domestic and industrial robots. The embedded STM32G431 MCU has peripherals for controlling three-phase BLDC motors, including four ultra-fast comparators, three op amps, and two sets of advanced PWM timers and 12-bit ADCs. The device also contains bootstrap diodes, a DC/DC converter, and low-dropout regulator that generate the gate-driver and MCU power rails from the motor supply with no external circuitry.
The EVLSPIN32G4-ACT can drive motors up to 250W, operating from a 12V, 24V, 36V, or 48V supply. Over-temperature, under-voltage, over-voltage, and over-current protection are all included, helping achieve a minimal bill of materials and small form factor. Users can select six-step or field-oriented control (FOC), sensored or sensorless rotor-position detection, and three-shunt or single-shunt current sensing.
The STWIN.box module is ready to plug in and power up. It includes an ultra-low power STM32U5 microcontroller, Bluetooth®, Wi-Fi, and NFC transceivers as well as a broad range of industrial-grade ST MEMS sensors. The sensors include a 3-axis magnetometer and a state-of-art industrial IMU with in-sensor AI capability, the Machine-Learning Core (MLC) technology, which together provide 9-DoF (Degrees of Freedom) inertial sensing. There is an additional high-performance accelerometer, a 3-axis digital vibration sensor with 6kHz bandwidth, and 2-axis high-precision inclinometer with MLC. Environmental sensors on-board include a digital barometer, and I²C/SMBus temperature sensor. There are also digital and analog MEMS microphones for capturing audio and ultrasound, respectively.
The software includes data-logging firmware and software suite, a Bluetooth Low Energy application and a Python software development kit (SDK). These are easily integrated in typical data science workflow to design edge-AI and machine-learning solutions. The high-speed datalogger (FP-IND-DATALOGMC) supports real-time monitoring with acquisition and labelling of high-resolution and precisely time-stamped datasets that combine data from motion-control algorithms with those from external sensors.
Leveraging the functionalities described and the complete support software, the reference design enables edge AI for motion control, combining STMicroelectronics sensing and three-phase motor-drive technologies. Users can bring AI close to the main motion-controller, creating a device with intelligence and decision-making capabilities. This allows faster and more efficient processing of data and actuation in a wide range of uses such as industrial automation, smart appliances, and generally any application that requires smart actuation.
www.st.com