www.ptreview.co.uk
21
'23
Written on Modified on
New electric parallel gripper from Festo is compact, simple and precise
Festo's HEPP electric gripper offers flexibility in handling multiple workpieces, addressing the need for handling solutions that can handle product diversity, shorter life cycles, and increased customization.
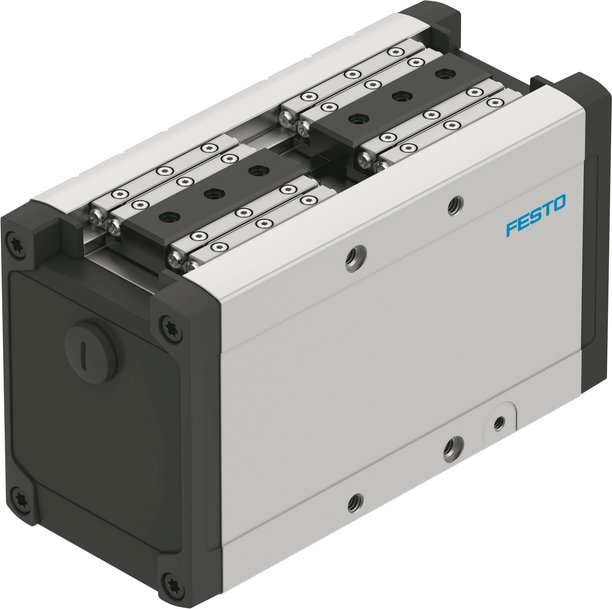
Its compact design and ability to handle complex movements precisely make the HEPP particularly suited to applications in the electronics and small parts industry, laboratory automation and special machine building.
The powerful and versatile HEPP is available in three different sizes with a gripping force of up to 400N and a stroke up to 56mm. The motor, encoder and controller are integrated into a single component, making the HEPP a very compact solution by removing the need for an external controller in the panel. This is even more critical for EOAT (End of Arm Tooling) on cartesian and 6 axis robots, as only the power supply and communication cable need to be routed through the energy chain.
The HEPP can be adjusted for a wide range of workpieces, both in terms of size and type of material as well as gripping force, to ensure the workpiece is handled correctly. To achieve high gripping forces within a compact unit, Festo has used a precise counter-rotating spindle that can manage the high stress from the feeder forces. This spindle also maintains process positioning reliability of less than 0.02 mm during endurance testing.
The HEPP is also a great solution for handling a workpiece in an e-stop condition due to the integrated holding brake on the motor. If the power supply fails, the tried-and-tested integrated holding brake will hold the gripper fingers in position to prevent the workpiece from being dropped and damaged.
Connectivity meets simplicity
The HEPP electric gripper makes connectivity simple. Users can choose between EtherCAT, PROFINET, EtherNet/IP and Modbus protocols to integrate the HEPP seamlessly into the system environment of their PLC. Necessary function blocks are also provided – at no extra cost – for integration in Festo, Siemens, Beckhoff, Rockwell and Omron environments.
Setting up the HEPP is equally simple: just input the parameters for position, stroke, speed, acceleration or gripping force. With this information and the dynamic electric motor, it is easy to adjust HEPP to specific applications. The motion response and how workpieces are handled can also be defined as required, including for complex production processes.
Integrating the HEPP follows exactly the same process as Festo’s industry leading CMMT range of Servo Controllers, ensuring that a standardised approach to programming of a complete automation solution can be achieved, which optimises programming and commissioning time.
www.festo.com