www.ptreview.co.uk
29
'23
Written on Modified on
TAKE BIG STEPS TOWARDS THE DIGITAL TWIN AND PREDICTIVE MAINTENANCE WITH NEXOFOX
Nexofox, a Dunkermotoren creation and part of the AMETEK brand, offers solutions and services that go beyond the motor. Currently, the team is not only dealing with control programs on the motors but is also working on digital twins and predictive maintenance.
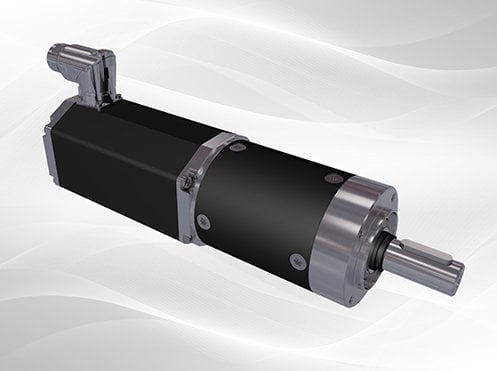
Markus Weishaar, Director of IIoT and Services at Dunkermotoren, explains in an interview how the results are presented in detail and what services Dunkermotoren customers can look forward to in the future.
Markus, with nexofox you develop digital services for Dunkermotoren's smart motors. Give us an insight into the work of nexofox.
M. Weishaar: Under the umbrella of nexofox, we basically deal with all topics that go beyond the actual motor solutions. This starts with classic services such as training or commissioning, and continues with the programming of motion codes, i. e. control programs directly on our motors, and ends with digital services. Of course, there is a lot of dynamics in this area. In recent years, there has been a great focus on networking and data acquisition, while we are currently working intensively on providing digital twins in the form of management shells and bringing predictive maintenance to the market. Another exciting aspect of our digital products and services is that they are not only available for Dunkermotoren, but also for motors from other manufacturers. For example, if our BGE 5510 dPro controller is used with another motor, all functionalities such as MotionCode, nexoLink or Smart Diagnostics are also available for it.
At sps, you will present the expansion of Smart Diagnostics. Why should Dunkermotoren customers use Smart Diagnostics? What benefits does the tool offer its users?
M. Weishaar: We have recognized that the full spectrum up to the cloud is not always needed, or at least not permanently. For this reason, we have split the Smart Diagnostics product - into nexoLink and Smart Diagnostic. NexoLink offers a simple way to integrate our controllers and motors into any IIoT or EDGE environment using standardized technologies such as OPC UA, MQTT and Docker. Smart Diagnostics, as a new add-on, is now a module that is based on this infrastructure and can be activated on-demand to specifically analyze and diagnose the behaviour of individual drives. But that is not all. The new structure enables us to easily dock other modules such as Predictive Maintenance or data integration in Asset Administration Shells (AAS) onto nexoLink.
This gives our customers an advantage in that they can get offers that are individually tailored to them. They only pay for what they need, or in the case of on-demand services, only when they need it. In the simplest case, customers can simply purchase nexoLink with a one-time license and integrate our motors themselves into their own IIoT ecosystem. On this basis, it is then always possible to add the other modules permanently or on-demand - as needed or desired.
What opportunities does Smart Diagnostics offer in terms of predictive maintenance?
M. Weishaar: To be honest, none. Predictive maintenance is a completely independent module. With Smart Diagnostics, the focus is on targeted as well as long-term data collection and supported analysis of the data by humans. Predictive Maintenance represents the automatic monitoring of the entire drive train, which sends a warning in advance of failures. The special feature of our solution is that, in contrast to many other approaches, we manage without additional sensors and use our motors as sensors to diagnose the drive train. The focus here is primarily on the wear of the mechanical components connected to the motor. On one hand, the normal creeping wear effects can be detected with the aim of maximizing the mechanical service life. On the other hand, the focus is also on sudden effects which, if ignored, would result in defects elsewhere. We are aware that an exact detection of the error patterns, such as the exact identification of the worn bearing, is only possible in cooperation with our customers who know the structure of their machine and can classify the error patterns. We can at least provide a detector for abnormalities right from the start.
How do you stand out from existing solutions?
M. Weishaar: As already mentioned, we stand out from others, for example with our Predictive Maintenance solution, in that we do not simply install an additional vibration sensor in the motor, but rather build on the existing hardware. In general, we distinguish ourselves in the market because we are not a software company that offers any kind of solution, but we develop solutions tailored to the drive technology and the controllers of Dunkermotoren. This is our core know-how and of course, we also feel comfortable connecting other manufacturer’s motors, but we don't necessarily see anything beyond that as our playground.
What development do you see for the future?
M. Weishaar: Currently I see a very strong trend in the market towards product data provision via the administration shell. I see this as the basis for bringing the topics together in the future. I think that in the future a predictive maintenance service can also be easily connected to a management shell. I imagine the following scenario: At delivery, an instance of the administration shell (AAS) is handed over to the customer. In the customer's environment, the live data of the motor that accumulates during operation is stored. If the customer then wants to use our Predictive Maintenance Service, he can book this from us via the AAS. In this case, the two instances of the management shell, ours and our customers', are synchronized with each other. Either the data is then used on-demand temporarily by the service or we as a component manufacturer "buy back" the live data for the analysis of our motors from our customer in return. In either case, this would create a closed transaction. The issue of data sovereignty would also be clearly regulated, as it would be a willing act to sell the data or make it available in exchange for a clearly named added value. Whether the approaches will look exactly like this remains to be seen. At the moment, many indicators are pointing in this direction.
Markus, with nexofox you develop digital services for Dunkermotoren's smart motors. Give us an insight into the work of nexofox.
M. Weishaar: Under the umbrella of nexofox, we basically deal with all topics that go beyond the actual motor solutions. This starts with classic services such as training or commissioning, and continues with the programming of motion codes, i. e. control programs directly on our motors, and ends with digital services. Of course, there is a lot of dynamics in this area. In recent years, there has been a great focus on networking and data acquisition, while we are currently working intensively on providing digital twins in the form of management shells and bringing predictive maintenance to the market. Another exciting aspect of our digital products and services is that they are not only available for Dunkermotoren, but also for motors from other manufacturers. For example, if our BGE 5510 dPro controller is used with another motor, all functionalities such as MotionCode, nexoLink or Smart Diagnostics are also available for it.
At sps, you will present the expansion of Smart Diagnostics. Why should Dunkermotoren customers use Smart Diagnostics? What benefits does the tool offer its users?
M. Weishaar: We have recognized that the full spectrum up to the cloud is not always needed, or at least not permanently. For this reason, we have split the Smart Diagnostics product - into nexoLink and Smart Diagnostic. NexoLink offers a simple way to integrate our controllers and motors into any IIoT or EDGE environment using standardized technologies such as OPC UA, MQTT and Docker. Smart Diagnostics, as a new add-on, is now a module that is based on this infrastructure and can be activated on-demand to specifically analyze and diagnose the behaviour of individual drives. But that is not all. The new structure enables us to easily dock other modules such as Predictive Maintenance or data integration in Asset Administration Shells (AAS) onto nexoLink.
This gives our customers an advantage in that they can get offers that are individually tailored to them. They only pay for what they need, or in the case of on-demand services, only when they need it. In the simplest case, customers can simply purchase nexoLink with a one-time license and integrate our motors themselves into their own IIoT ecosystem. On this basis, it is then always possible to add the other modules permanently or on-demand - as needed or desired.
What opportunities does Smart Diagnostics offer in terms of predictive maintenance?
M. Weishaar: To be honest, none. Predictive maintenance is a completely independent module. With Smart Diagnostics, the focus is on targeted as well as long-term data collection and supported analysis of the data by humans. Predictive Maintenance represents the automatic monitoring of the entire drive train, which sends a warning in advance of failures. The special feature of our solution is that, in contrast to many other approaches, we manage without additional sensors and use our motors as sensors to diagnose the drive train. The focus here is primarily on the wear of the mechanical components connected to the motor. On one hand, the normal creeping wear effects can be detected with the aim of maximizing the mechanical service life. On the other hand, the focus is also on sudden effects which, if ignored, would result in defects elsewhere. We are aware that an exact detection of the error patterns, such as the exact identification of the worn bearing, is only possible in cooperation with our customers who know the structure of their machine and can classify the error patterns. We can at least provide a detector for abnormalities right from the start.
How do you stand out from existing solutions?
M. Weishaar: As already mentioned, we stand out from others, for example with our Predictive Maintenance solution, in that we do not simply install an additional vibration sensor in the motor, but rather build on the existing hardware. In general, we distinguish ourselves in the market because we are not a software company that offers any kind of solution, but we develop solutions tailored to the drive technology and the controllers of Dunkermotoren. This is our core know-how and of course, we also feel comfortable connecting other manufacturer’s motors, but we don't necessarily see anything beyond that as our playground.
What development do you see for the future?
M. Weishaar: Currently I see a very strong trend in the market towards product data provision via the administration shell. I see this as the basis for bringing the topics together in the future. I think that in the future a predictive maintenance service can also be easily connected to a management shell. I imagine the following scenario: At delivery, an instance of the administration shell (AAS) is handed over to the customer. In the customer's environment, the live data of the motor that accumulates during operation is stored. If the customer then wants to use our Predictive Maintenance Service, he can book this from us via the AAS. In this case, the two instances of the management shell, ours and our customers', are synchronized with each other. Either the data is then used on-demand temporarily by the service or we as a component manufacturer "buy back" the live data for the analysis of our motors from our customer in return. In either case, this would create a closed transaction. The issue of data sovereignty would also be clearly regulated, as it would be a willing act to sell the data or make it available in exchange for a clearly named added value. Whether the approaches will look exactly like this remains to be seen. At the moment, many indicators are pointing in this direction.
www.dunkermotoren.com