www.ptreview.co.uk
31
'23
Written on Modified on
EXPERIENCE UNIQUE INNOVATIONS LIVE
From September 18 to 23, 2023, SCHUNK will be showcasing its close-packed 360-degree portfolio at EMO Hanover.
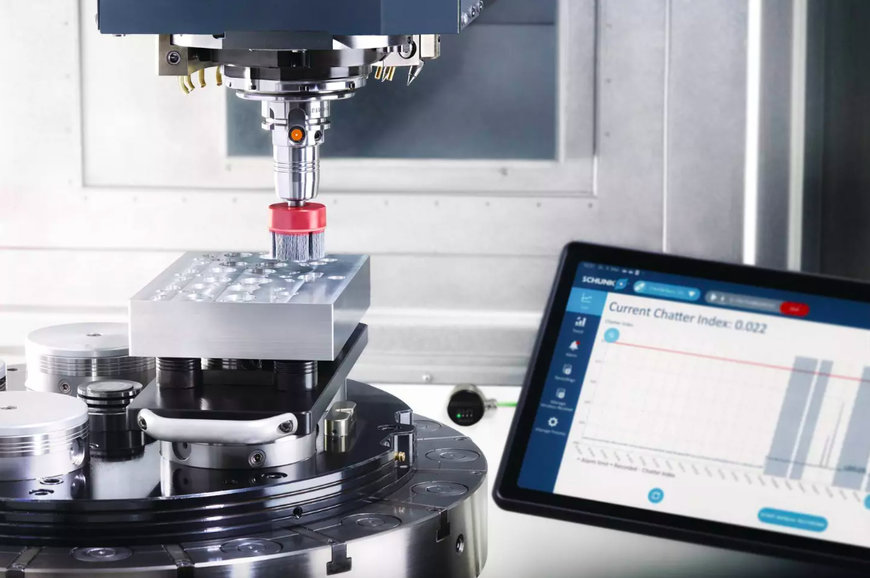
The smart toolholder iTENDO2 provides real-time data directly from the tool and detects wear early on. With easy connect and easy monitor, SCHUNK now provides two new enhanced digitalization stages.
Currently, the world of industrial production is undergoing a rapid and profound change. The need for higher efficiency, more flexibility, better quality, and higher accuracy are challenges for every manufacturing company; at the same time, they are drivers of technological development. Under the motto "Innovate Manufacturing," the industry will be showcasing its solutions to urgent present and future problems at EMO. SCHUNK will be presenting comprehensive solutions and a host of innovations, which can be used to realize digital transformation and come closer to the goal of sustainable production.
Sustainable principles in handling and workpiece clamping
Energy and resource-saving processes are a prerequisite for sustainable production. The key here is reducing consumption. EMO trade show visitors will be able to experience SCHUNK's energy-free gripping of sensitive components with the gripping technology ADHESO and see for themselves, how parts handling could be done residue-free and easy on resources - with no external energy supply. ADHESO uses natural adhesion forces to handle sensitive components in the manufacture of battery and fuel cells, as well as in applications in the medical, pharmaceutical, and electrical industries.
Advanced generations of modern lathe chucks, such as the jaw quick-change chuck ROTA THW3 also follow the principle of sustainability. In addition to its enormous flexibility and functionality, the lathe chuck impresses with up to 20 times longer maintenance intervals than comparable products due to its patented sealing. This results in up to 20 times less lubricant consumption; and the coolant needs to be changed less frequently. In addition to the environmentally friendly aspects, this also opens up new fields of application. Thanks to the jaw quick jaw system, the chuck can be adapted to changing clamping tasks in a matter of seconds.
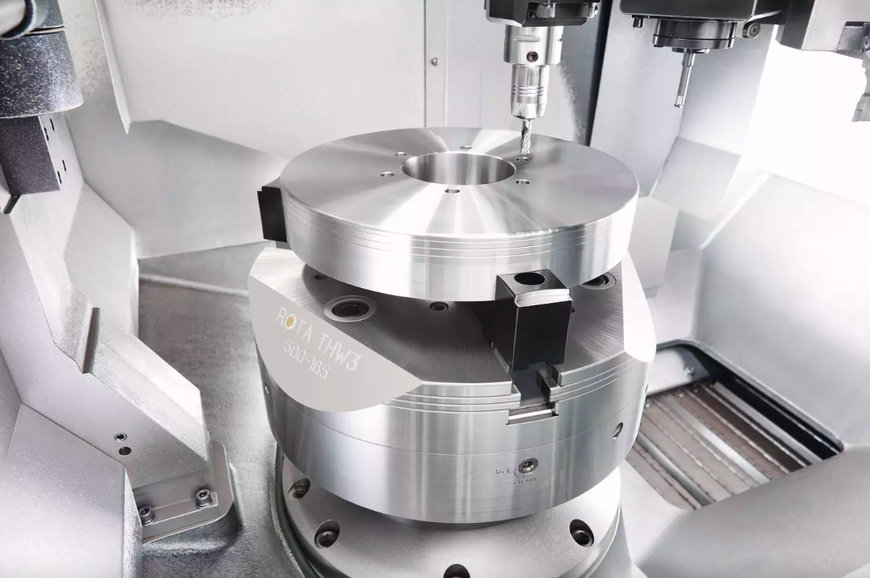
The flexible jaw quick-change chuck ROTA THW3 enables up to 20 times longer maintenance intervals than comparable products thanks to patented sealing.
Digitally networked down to the component
Networked production already starts on a small scale, with the component. Smart manufacturing components make a significant contribution to efficient, more sustainable, and transparent processes. In Hanover, SCHUNK will be demonstrating a variety of actuator and sensory clamping systems. The electromechanical quick-change pallet module NSE3-PH 138 IOL with its innovative piezo-hydraulic drive and fully integrated sensor technology is one of the absolute highlights: The clamping module is controlled via IO-Link and generates high pull-down forces with identical dimensions as comparable pneumatic clamping modules. Integrated electronics detect various clamping states such as clamping slide positions or pallet presence without additional interfering contours.
Another trade show highlight is the iTENDO² smart hydraulic expansion toolholder. It provides real-time data directly from the tool and detects wear at an early stage. In addition to process-reliable machining, the intelligent toolholder ensures a longer tool service life and less waste. With easy connect and easy monitor, SCHUNK now provides two new enhanced digitalization stages. The extension package iTENDO² easy connect enables simple connection to the machine and to the existing process monitoring system. iTENDO² easy monitor, on the other hand, offers machine operators a straightforward introduction to simple process monitoring.
Easy configuration
SCHUNK already showed how to make application-specific solutions quickly available with its new configurable product series last year. Using free, browser-based SCHUNK web tools, electric and pneumatic SCHUNK grippers, gripper fingers, and chuck jaws can be adapted to specific applications. At EMO, SCHUNK presents easyToolholder, another product configurator for individual design of toolholders. With the new digital tool, standard toolholders can be modified in terms of dimensions, clamping diameter, interface or chip bore as required and be optimally adapted to the application with just a few clicks. The respective 3D data is available for download in real time and in various formats and can then be tested virtually in the machine simulation. This reduces complexity in system planning and provides tailored solutions for a wide range of applications.
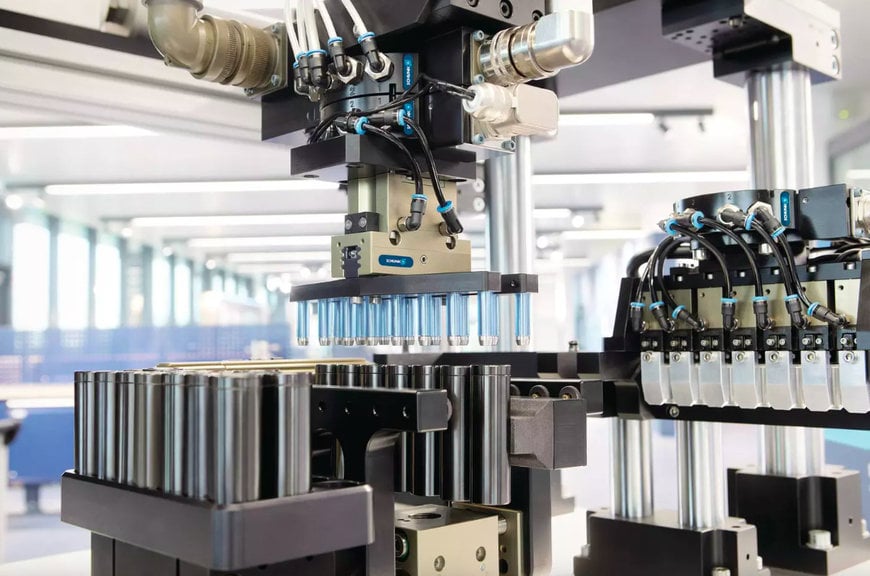
Everything from a single source: Thanks to its extensive application know-how and broad portfolio, SCHUNK designs suitable concepts for tasks of electric mobility.
360-degree portfolio for new industries
Automated processes are becoming more and more important. There are many reasons for this and, sooner or later, companies will have to embrace this trend. With its new jaw quick-change system BWA for TANDEM3- clamping force blocks, this is precisely the issue SCHUNK is addressing. With it, the clamping jaws for 2- or 3-jaw clamping force blocks can be exchanged manually or automatically via a robot within a very short time and thereby adapted to new clamping tasks - completely without tools.
New SCHUNK adapter jaws now open access to the extensive SCHUNK clamping jaw program for vises from third-party manufacturers, too. Until now, the portfolio of available top jaws was limited to the respective vise manufacturer, since the interfaces are manufacturer-dependent. Now, with its adapter jaws, SCHUNK is enabling compatibility between vises from third-party manufacturers and the top jaws portfolio from SCHUNK and Gressel.
EMO visitors can look forward to further innovations in toolholder technology or automated pallet loading.
Currently, the world of industrial production is undergoing a rapid and profound change. The need for higher efficiency, more flexibility, better quality, and higher accuracy are challenges for every manufacturing company; at the same time, they are drivers of technological development. Under the motto "Innovate Manufacturing," the industry will be showcasing its solutions to urgent present and future problems at EMO. SCHUNK will be presenting comprehensive solutions and a host of innovations, which can be used to realize digital transformation and come closer to the goal of sustainable production.
Sustainable principles in handling and workpiece clamping
Energy and resource-saving processes are a prerequisite for sustainable production. The key here is reducing consumption. EMO trade show visitors will be able to experience SCHUNK's energy-free gripping of sensitive components with the gripping technology ADHESO and see for themselves, how parts handling could be done residue-free and easy on resources - with no external energy supply. ADHESO uses natural adhesion forces to handle sensitive components in the manufacture of battery and fuel cells, as well as in applications in the medical, pharmaceutical, and electrical industries.
Advanced generations of modern lathe chucks, such as the jaw quick-change chuck ROTA THW3 also follow the principle of sustainability. In addition to its enormous flexibility and functionality, the lathe chuck impresses with up to 20 times longer maintenance intervals than comparable products due to its patented sealing. This results in up to 20 times less lubricant consumption; and the coolant needs to be changed less frequently. In addition to the environmentally friendly aspects, this also opens up new fields of application. Thanks to the jaw quick jaw system, the chuck can be adapted to changing clamping tasks in a matter of seconds.
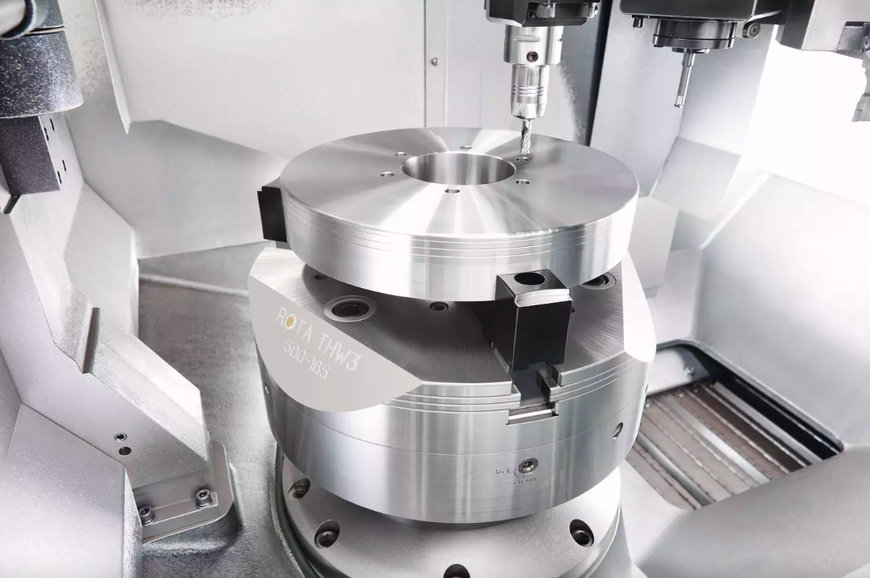
The flexible jaw quick-change chuck ROTA THW3 enables up to 20 times longer maintenance intervals than comparable products thanks to patented sealing.
Digitally networked down to the component
Networked production already starts on a small scale, with the component. Smart manufacturing components make a significant contribution to efficient, more sustainable, and transparent processes. In Hanover, SCHUNK will be demonstrating a variety of actuator and sensory clamping systems. The electromechanical quick-change pallet module NSE3-PH 138 IOL with its innovative piezo-hydraulic drive and fully integrated sensor technology is one of the absolute highlights: The clamping module is controlled via IO-Link and generates high pull-down forces with identical dimensions as comparable pneumatic clamping modules. Integrated electronics detect various clamping states such as clamping slide positions or pallet presence without additional interfering contours.
Another trade show highlight is the iTENDO² smart hydraulic expansion toolholder. It provides real-time data directly from the tool and detects wear at an early stage. In addition to process-reliable machining, the intelligent toolholder ensures a longer tool service life and less waste. With easy connect and easy monitor, SCHUNK now provides two new enhanced digitalization stages. The extension package iTENDO² easy connect enables simple connection to the machine and to the existing process monitoring system. iTENDO² easy monitor, on the other hand, offers machine operators a straightforward introduction to simple process monitoring.
Easy configuration
SCHUNK already showed how to make application-specific solutions quickly available with its new configurable product series last year. Using free, browser-based SCHUNK web tools, electric and pneumatic SCHUNK grippers, gripper fingers, and chuck jaws can be adapted to specific applications. At EMO, SCHUNK presents easyToolholder, another product configurator for individual design of toolholders. With the new digital tool, standard toolholders can be modified in terms of dimensions, clamping diameter, interface or chip bore as required and be optimally adapted to the application with just a few clicks. The respective 3D data is available for download in real time and in various formats and can then be tested virtually in the machine simulation. This reduces complexity in system planning and provides tailored solutions for a wide range of applications.
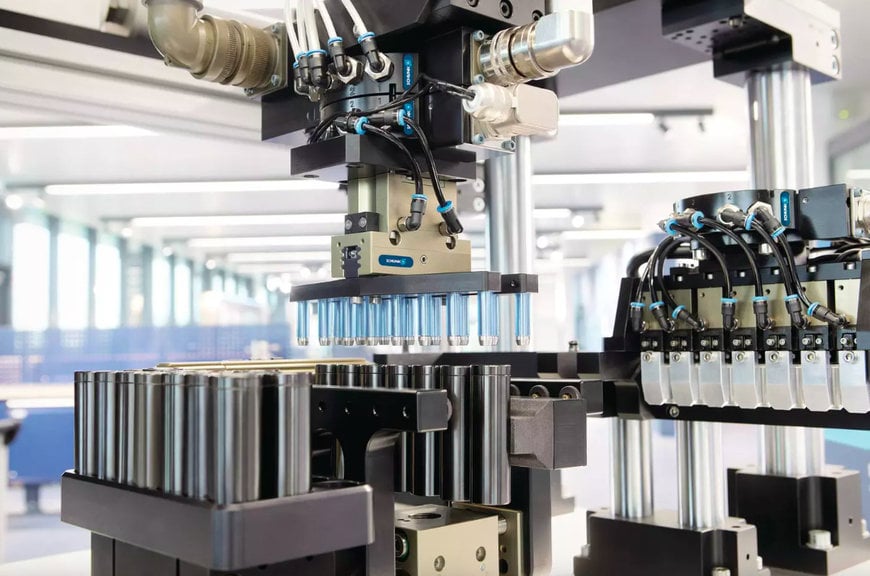
Everything from a single source: Thanks to its extensive application know-how and broad portfolio, SCHUNK designs suitable concepts for tasks of electric mobility.
360-degree portfolio for new industries
Automated processes are becoming more and more important. There are many reasons for this and, sooner or later, companies will have to embrace this trend. With its new jaw quick-change system BWA for TANDEM3- clamping force blocks, this is precisely the issue SCHUNK is addressing. With it, the clamping jaws for 2- or 3-jaw clamping force blocks can be exchanged manually or automatically via a robot within a very short time and thereby adapted to new clamping tasks - completely without tools.
New SCHUNK adapter jaws now open access to the extensive SCHUNK clamping jaw program for vises from third-party manufacturers, too. Until now, the portfolio of available top jaws was limited to the respective vise manufacturer, since the interfaces are manufacturer-dependent. Now, with its adapter jaws, SCHUNK is enabling compatibility between vises from third-party manufacturers and the top jaws portfolio from SCHUNK and Gressel.
EMO visitors can look forward to further innovations in toolholder technology or automated pallet loading.
www.schunk.com