www.ptreview.co.uk
08
'22
Written on Modified on
AI enables greater mobility: Personalized finger joint implants from a 3D printer
The remobilization of finger joints that have been damaged by illness or injury is an emerging market in the field of demand-driven patient care. The FingerKIt consortium, which brings together five Fraunhofer institutes, uses AI to develop personalized 3D-printed joint implants so that these delicate finger parts can be replaced when necessary.
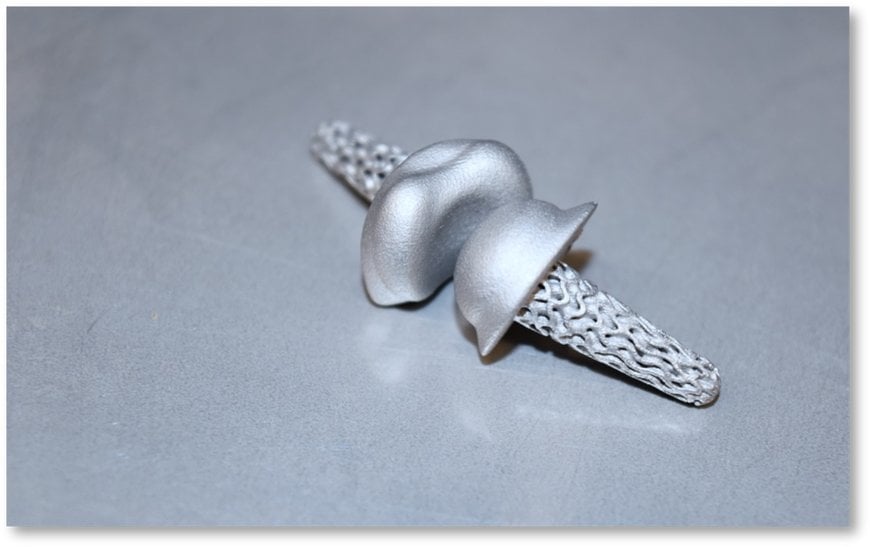
When finger joints become inflexible, after a sports accident or as a result of rheumatoid arthritis for example, it can put serious limitations on someone’s life and cause them physical and mental strain. For certain professions — such as musicians, surgeons or craftspeople — it can even mean the end of their career. In the future, a solution developed by the Fraunhofer Research Institution for Additive Manufacturing Technologies IAPT, the Fraunhofer Institute for Ceramic Technologies and Systems IKTS, the Fraunhofer Institute for Toxicology and Experimental Medicine ITEM, the Fraunhofer Institute for Mechanics of Materials IWM and the Fraunhofer Institute for Digital Medicine MEVIS could help to restore the mobility of fingers with damaged or ruined joints.
Current treatment for damaged finger joints
At the moment, if a finger joint loses its function due to accident or injury, the treatment methods are limited. In most cases, the joint is fused, but this results in severe restrictions in the patient’s day-to-day life. If an implant is to be used, there are currently two options on the market: silicone implants, which often come loose quickly and need to be reattached in another procedure, or basic standard implants, which are only available in certain sizes and do not allow full movement. To ensure the best possible patient care, the goal should therefore be to create a perfectly fitting solution that does not slip out of place and that restores the previous level of mobility — i.e., a personalized implant.
FingerKIt project: numerous innovations in one forward-looking product
This could now be possible thanks to a concept developed by five Fraunhofer institutes within the FingerKIt project: An automated process chain will allow personalized finger joint implants to be produced from metallic or ceramic materials in a rapid, safe and certified manner. The scientists at Fraunhofer MEVIS started off by developing a piece of AI-based software which is able to turn two-dimensional X-ray images into three-dimensional models of the finger bones and correct any malposition of the fingers. The researchers from Fraunhofer IAPT then use AI to derive the individual implant design from the finger model and send it for 3D printing. Since the structures involved are very fine and delicate, the scientists use the metal binder jetting process to build up the pieces layer by layer. The implants then undergo a sintering process, which means that they are compacted and solidified. At Fraunhofer IKTS, the implants are produced using near net shape manufacturing — a process which aims to create products that are as close as possible to the final shape, reducing the need for subsequent finishing work. Thanks to the expertise of Fraunhofer IKTS, it is also possible to use ceramic materials — these are processed by means of slip casting, which is a special plaster mold casting process. Fraunhofer ITEM is taking care of questions regarding the biological compatibility and certification of the implants, while Fraunhofer IWM is responsible for the simulation of the mechanical loads.
The researchers have developed a number of innovations in the course of this project: “The AI-based calculation of a three-dimensional implant design from 2D templates such as X-ray images is completely new and is now patent pending,” reveals Dr. Arthur Seibel, head of the Part Design group at Fraunhofer IAPT. His colleague Dr. Philipp Imgrund, head of the AM Process Qualification department at Fraunhofer IAPT, adds: “Process engineering is special too. As the structure of the implant shaft is very delicate, we have chosen to use the metal binder jetting 3D printing method for titanium. This method allows for an extremely precise production of the small, complex implants and also enables us to structure the surface of the shaft in such a way that it grows into the bone more effectively. Furthermore, this minimizes the finishing work required for the joint surfaces, which need to be as smooth and frictionless as possible.”
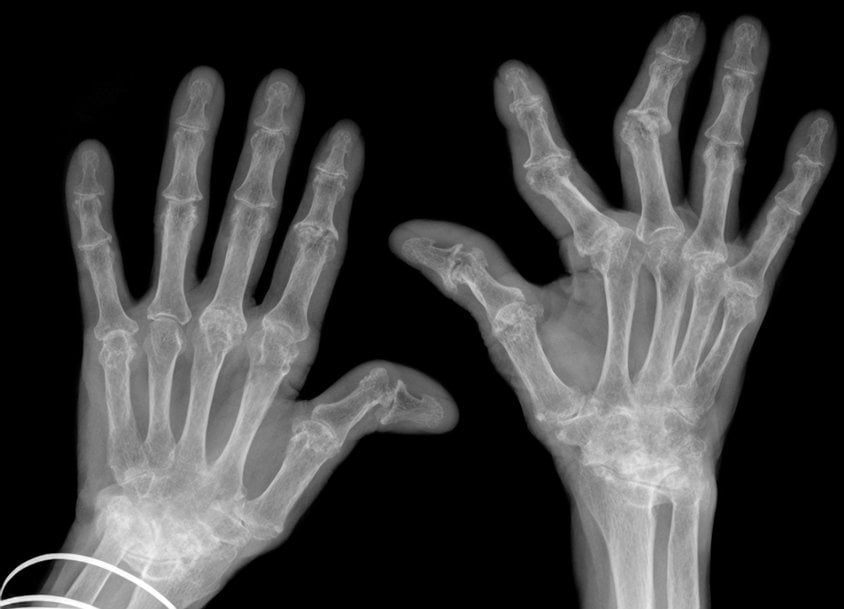
Rheumatoid arthritis: Even patients with severely bent fingers can receive optimal treatment with a FingerKIt implant.
A new standard for patient care?
The results of the FingerKIt project are good news for any patients who in the past have been unable to find the help they need. The Fraunhofer innovations mean that, in the future, it will be possible to provide effective treatment even for complicated cases such as severely bent fingers, missing bone parts or very small joints. Furthermore, thanks to the automated model creation and 3D printing, the personalized production process also saves time: According to the researchers’ initial calculations, it may be possible to save up to 60 percent of the time normally required from identifying the need for an implant to fitting it in the patient. This means that the process could be completed within a matter of days, resulting in shorter hospital stays and, hence, lower costs. Not only that but, because the implant design is modeled on the original joint, the level of mobility achieved is much greater than with currently available solutions. Dr. Imgrund sums up the project as follows: “FingerKIt could completely change the treatment of rheumatoid arthritis, for example. Personalized implants could become the gold standard.”
Finger joint implants — a growth market
According to the German Society for Rheumatology, around two percent of the adult population in Germany are suffering from inflammatory rheumatic diseases — and the majority of them do not wish to sacrifice their good quality of life as they get older. The newly developed implants will also be able to help patients who have sustained injuries. In comparison with foot or ankle implants, for example, the market for the remobilization of finger joints is still significantly underdeveloped. Experts predict that the total potential will stretch to 5.8 million euros by 2026.
The technological development within the FingerKIt project has now reached a stage where the product could be made ready for the market in collaboration with a partner from the medical engineering sector: The AI-based design creation and the manufacturing process work, and exhibitable implants have already been produced. The next step is to obtain the necessary approval. Dr. Imgrund: “We are currently looking for corporate partners who have the required expertise to help us bring our AI-created medical devices to market.”
www.fraunhofer.com