www.ptreview.co.uk
09
'22
Written on Modified on
BAUMÜLLER PRESENTS THE NEW B MAXX 6000 SERVO DRIVE FAMILY
The new b maXX 6000 servo controller generation stands for more performance and maximum scalability. Yet the servo drive can do even more: The drive can be used as a sensor or sensor hub and offers scalable IoT connectivity in the cloud, e.g. via an edge PC.
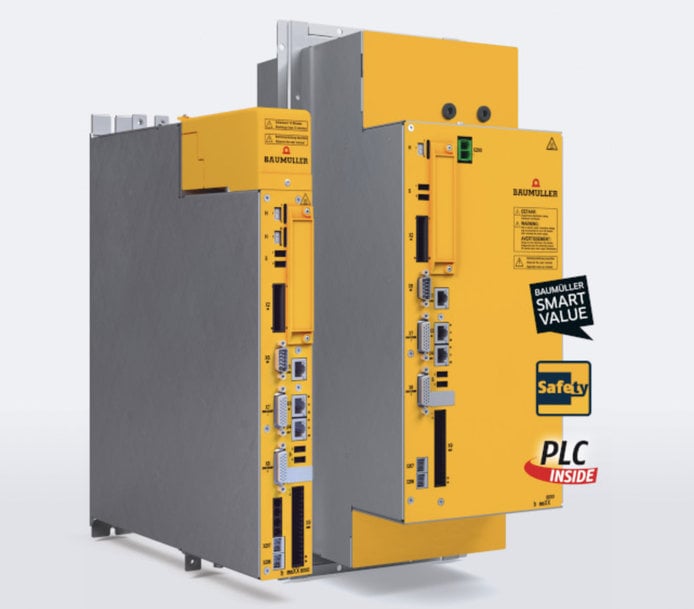
Reduce your Footprint stands for intelligent functions from the Baumüller modular SmartValue software kit. These help to improve the energy balance in production and to reduce manufacturing costs. One highlight is the integrated temperature model, which monitors important components in the power module. This enables the servo drives to be dimensioned and used optimally. This function optimizes the use of resources and permanently reduces energy consumption during operation.
New standards are also set for the device dimensions: Apart from the space-saving module system (b maXX 6300), the mono devices (b maXX 6500) are now also significantly compacter. The installed volume of the sizes is reduced significantly and therefore enables even smaller assemblies.
Highlights of the b maXX 6000 family: maximum scalability and performance
The new b maXX family offers maximum scalability to adapt the drive optimally to the requirements of the respective application. Numerous encoder, hardware and safety options are available to choose from. For example, in the case of encoders, you can choose between resolvers, optical and pure digital encoders for the standard interfaces. In the area of the hardware, the signal bus, service option, digital and analog I/Os, as well as brake connection can be selected, among other things. Integration in all kinds of different machine topologies is possible, as in the b maXX 5000 too, via numerous fieldbus options.
n relation to safety, different variants are available, from the simple hardware-controlled STO (Safe-Torque-Off) to different higher safety functions, activated via FSoE (FailSafe over EtherCAT) or hardware I/Os, all in compliance with the highest safety level (certification up to SIL 3 and PLe levels is currently being implemented). Both variants can also be combined to set up the secure drive architecture as flexibly as possible.
Safety for high-performance applications
The new safety functions have been specially developed for applications with high dynamic and precision requirements. In the new servo controllers, the safety module is integrated directly in the device. The advantage: Safety-related encoder signals can therefore be evaluated with even higher resolution. This significantly improves the position and speed accuracy still further. If, for example, a simple resolver is used in the application, then the speed resolution for the safety monitoring with the new converter generation is below 1 rpm. The application can therefore achieve a high performance even in combination with robust encoder technology, which reduces the total costs of the machine.
The safety functions of the new servo controllers also set new standards with regard to the ability to respond to safety-related events. For example, on triggering STO the servo drive is switched torque-free with a delay of less than 1 ms. Due to this fast response time, the speed of the machine can be increased, thus increasing the overall productivity.
Advantages are also provided by the new SP (secure position) safety function for transferring the secure position over the FSoE protocol. This allows not only secure space monitoring but also collaboration in applications with multi-dimensional movements, for example in laser cutting or in robotics. The ETG (EtherCAT Technology Group) standard for FSoE communication has been implemented in the new generation. This increases flexibility when choosing a higher-level safety control.
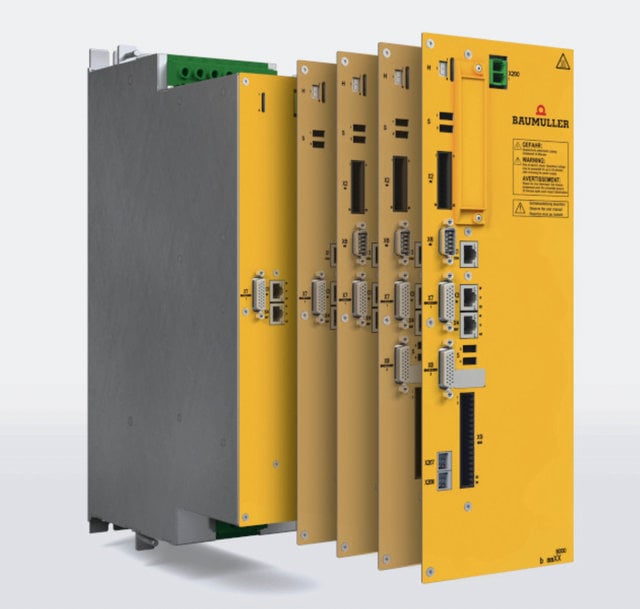
Load encoders for safety engineering: Greater dynamism through higher measuring accuracy
Mechanical components such as transmissions or drive belts can have a negative effect on the reaction accuracy. To prevent possible influence due to belt slippage or transmission clearance, in addition to the encoder on the motor, another encoder can be mounted on the load and be included in the secure monitoring. This option is available in the new servo drive and allows a higher machine speed, since the machine decelerates even faster if necessary and can be stopped. This high-precision encoder evaluation leads, for example, to higher productivity in the case of milling machines.
Parameterizable delay time and ramp monitoring: Higher machine availability for dangerous applications
The Baumüller drives offer the function of a freely parameterizable delay time (SS1 time). This is switched between a safety function and the associated Safe-Torque-Off (STO) switching-off reaction. The SS1 time delays the triggering of the STO if the machine must not be allowed to coast down in an uncontrolled way. Thanks to the parameterizable delay time, another action (e.g. quick stop) can be carried out before STO is triggered. In this case, the safety module automatically sends a signal to the servo drive, which then carries out the parameterized reaction. The moment is not switched torque-free until the SS1 time has expired. This functionality not only prevents injuring of people and damage to machines but also achieves higher machine availability.
In addition to the SS1 time described above, the new servocontrollers can also work with ramp monitoring for the SS1 and the SS2 function (Safe Stop 1 and Safe Stop 2). This is a parameterizable deceleration ramp (SS1-r = Safe Stop 1 Ramp Monitoring), which uses a safe range for stopping the drive. The shutdown to final standstill is achieved even more safely without exceeding the speed limits. A typical area of use is applications in which coasting down of the motor represents a hazard, for example, in the case of textile or woodworking machines.
Baumüller SmartValue – intelligent drives for Industry 4.0
Another new function concerns the recording, preprocessing and evaluation of the machine data in the servo drive. The intelligent monitoring functions from the Baumüller modular SmartValue software kit can be used to register drive parameters and transfer them to other architecture layers such as an Edge PC or cloud. With the integrated oscilloscope function, the devices can send signals to the control unit via the fieldbus and, for example, forward information via an OPC UA server.
The signals are provided continuously or triggered directly by the servo drive. This does not require any additional work for external sensors, wiring or a separate evaluation unit. If the available data is insufficient for the required use case, the servo drive or the servo motor can easily be used as a sensor hub. This allows the database to be extended by external sensors, e.g. via vibration sensors or data from an intelligent transmission.
The Smart Energy Reduction function is based on precisely this concept. With the new function, the energy consumption of individual axes can be determined per cycle. The energy measurement is carried out autonomously and in real time in the b maXX servo drives used. A software module in the higher-level PLC analyses the transferred measured values and then calculates, among other things, the actual energy consumption throughout the entire drive system. The values are then displayed in the machine visualization. Alternatively, a dashboard displays the results of the measurement via open IoT interfaces such as OPC UA.
This function allows optimization of the machine cycle’s energy and a reduction in production costs. This energy consumption transparency also helps the manufacturer to determine their product carbon footprint (PCF).
Intelligent drives carry out control tasks
In order to relocate certain functions from the central control into the controller, Baumüller offers two control solutions integrated into the drive: the b maXX softdrivePLC with a cycle time of ≥62.5 μs and the b maXX PLC di with a fieldbus cycle time of ≥250 μs.
The software-based b maXX softdrive PLC combines Motion Control and PLC functions and is programmable in accordance with IEC 61131. In this way, for example, simple computing of digital inputs or even highly complex control algorithms can be carried out decentrally. With the help of the softdrivePLC, programs can run highly synchronized with the controller clock cycle (≥62.5 μs). The softdrivePLC is available with the start of the new converter generation.
The portfolio of drives with integrated control is extended to include the b maXX PLC di, with which the even more complex motion control, technology and control functions are possible directly in the drive. The control PLC can therefore be relieved, made smaller or even be completely replaced, since the PLC di can also be used as the EtherCat master for the control of other servo converters. The PLC di, which will be presented soon, is one of the fastest PLCs in the drive. With a fieldbus cycle time of ≥250 μs, up to 16 axes can be activated for complex movement tasks. The devices of the b maXX 6000 family are already prepared for integration of the b maXX PLC di and can be extended to include these functions.
Switching to the new generation is easy
Existing customers can switch from the b maXX 5000 series with little effort. All existing engineering tools such as ProMaster or ProDrive can continue to be used. The controller models are already integrated as a digital twin in the ProSimulation software and are available for virtual commissioning.
The new b maXX 6500 mono devices: extremely compact and with higher peak performance
In addition to the new controllers, a complete new power module family was developed for the b maXX 6500 mono devices. This enabled the dimensions to be reduced significantly and the power density to be increased considerably. In the case of the size 4 with a power range up to 75 kW, for example, this means a saving of 48 percent compared to the previous installed volume. The new mono devices therefore require less space in the control cabinet and can be installed in the most confined space even more easily. Alongside the smaller machine footprint, the material savings in the servo drives mean a reduction in the ecological footprint and thus make a contribution to greater sustainability.
Current peaks are a major challenge for drive technology. For example, in injection molding, enormous maximum torques are required to generate the locking or pressing force and to maintain it if necessary. The drives are therefore not dimensioned correctly solely based on the nominal torques but also on the basis of the peak torque.
The peak power for the new b maXX 6500 mono devices was therefore increased considerably. Compared to the b maXX 5500 series, for example, the size 4 devices achieve a peak current that is 30 to 50 percent higher. This means that smaller sizes can be used for dynamic applications. The machine builder therefore benefits from lower initial costs and from a smaller space requirement in the control cabinet.
The scalable power modules of the mono units are planned with an extended power range of up to 400 kW. Higher power outputs can be achieved by connecting the mono devices in parallel. With fuse ratings optimized still further, the new devices are even more precisely configurable for the respective application.
Conclusion
With the new b maXX 6000 device generation, Baumüller presents a very flexible and high-performance servo drive system, in which the strengths of the predecessor family, the b maXX 5000, have been consistently developed further. The drives have convincing optimized sizes, scalable safety functions and smart software features for Industry 4.0. With the b maXX 6000, the applications implemented are future-proof and are designed for energy and cost-efficient operation.
www.baumueller.com