www.ptreview.co.uk
27
'22
Written on Modified on
Using ASICs to enable high-performance, cost-effective position sensors
Dr Mike Coulson, Analogue Design Manager at ASIC design and supply company Swindon Silicon Systems, explains how custom ICs for position sensors are helping to deliver speed, accuracy and cost savings to industrial automation. Numerous industries are embracing the ‘4.0’ paradigm, which frames the adoption of various digital technologies as a fourth industrial revolution.
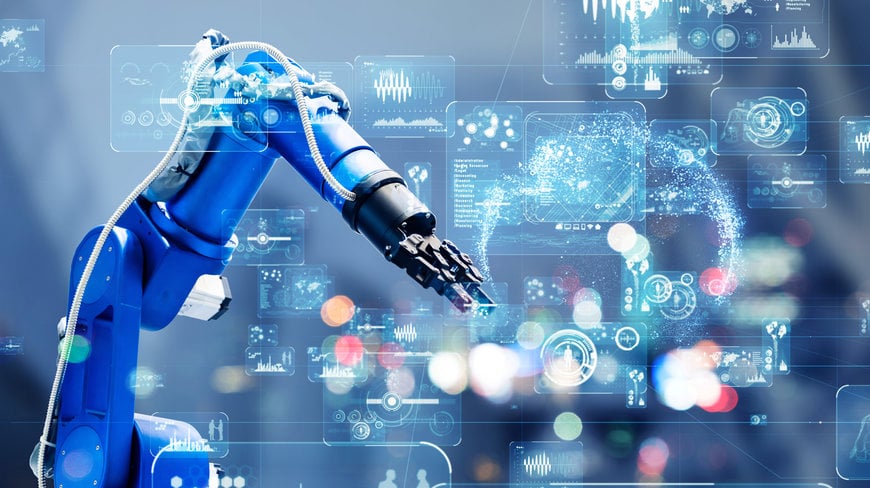
Alongside these new concepts sits an evolution of the robotics that underpinned Industry 3.0: an advancement of seemingly mature technologies to serve us for the coming decades. Part of this advancement is facilitated by next generation position sensors employing Application Specific Integrated Circuits (ASICs).
Modern industrial processes are underpinned by highly automated machinery, which must move with accuracy and speed. Accuracy is an enabler: it allows new feats of manufacturing to be accomplished, and gives rise to products that outperform and outlast their precursors. Speed equates to higher throughput, and reduced part cost. Such machinery may be driven by electromagnetic, pneumatic or hydraulic means — but will invariably be under the control of an electronic system that governs its motion. A key part of these systems are the position sensors that detect the state of each moving component.
‘Position sensor’ is a broad term covering a range of technologies. In this article, we consider sensors that measure rotation and linear displacement. For example, a rotary encoder might measure the angle of a robotic arm, while a linear encoder might report the position of a printhead. In each case a ‘read-head’ moves across a precisely manufactured scale, often graduated with sophisticated ‘redundant’ patterns.
Position sensor electronics
The encoder includes a sensing element that converts a physical stimulus into a weak electronic signal. In an inductive encoder, this is a coil detecting a changing magnetic environment — say a slotted ferrous metal scale. In an optical encoder, the sensing element may be a phototransistor. Each case features excitation circuitry to create the stimulus, and signal conditioning circuitry to select and amplify the weak electrical response. Most encoders then digitise the signal using an Analogue-to-Digital Converter (ADC), the digital result passing to a Central Processing Unit (CPU) with Random-Access Memory (RAM) and flash memory.
This CPU calculates position from the potentially sophisticated scale encoding, before serialising the output. It may also recognise events such as reference marks being passed, or overspeed conditions, generating immediate interrupts towards the host system. There are interface electronics too, which provide a bidirectional data path from the CPU to the host, and finally components that provide a stable power supply voltage.
Increasing integration
When an encoder is first prototyped, these separate components appear as numerous off-the-shelf ICs, each supported by its own discrete capacitors and resistors. When production volumes are very low, and the design does not attempt class-leading performance, this may be an optimum solution. In most other cases the cost of developing an ASIC is justified, and the developers integrate as much of the circuitry as possible into a single package. The benefits of this can be dramatic.
Firstly, the PCB’s size is reduced, leading to a smaller and lighter encoder that offers improved dynamics, and is able to serve new applications. Assembly becomes simpler, and the electronics are afforded greater protection from environmental factors such as chemical attack and vibration. Some customers also value the protection it affords for their circuit IP, as monolithically integrated circuits are far more difficult to reverse engineer than a collection of standard parts wired together in plain sight.
Secondly, an ASIC brings opportunity to reduce part cost. Systems built from off-the-shelf components are frequently over-engineered, as standard parts are designed and sold with maximum versatility in mind. Swindon will assess its customers’ systems and hunt out every opportunity to squeeze cost from the design: is that CPU really necessary, if we could synthesise hard-coded logic for a fraction of the price? Is that dual-channel ADC used to capacity? For high volume products, the cost of the ASIC’s development is offset by a decimated bill of materials and simplified assembly.
Thirdly, an ASIC design allows investment in performance where it matters. In position sensors this might be a non-linearity specification, equating to accuracy at different scale points. It could equally be an aggressive target on low-frequency noise, which cannot be easily averaged away. This is where working with an experienced ASIC partner yields benefits: the entire signal path can be optimised and simulated down to the finest detail, and proven IP and expertise can be deployed.
For example, ‘chopping’ may mitigate troublesome flicker noise, or temperature measurement may be used to compensate for voltage reference drift. The best ASIC partners serve as consultants from the outset, understanding the system, recognising where the custom IC design unlocks improvements, and guiding the customer as they write a black-box specification.
The process of ASIC development
A company should consider whether a project is ready to benefit from a custom ASIC as soon as a prototype exists. At this point, a supplier like Swindon will assess whether a custom solution is for them, and identify the best possible system partitioning. It is common, but not always necessary, for a supplier to undertake a four to eight-week feasibility study to inform these conclusions and arrive at a detailed proposition and costing. The supplier will then architect the chip, breaking the design down into analogue and digital blocks. At this stage, many customers benefit from receiving a detailed behavioural model, in VHDL for example, to allow co-simulation with the rest of their system.
Beyond this, the work is firmly in the supplier’s hands, and no more resource is required from the customer beyond periodic reviews to demonstrate the growing maturity of the design and its verification. The timescale of the entire process from specification to silicon will depend on the complexity. But in every case, it is essential to work with an ASIC supplier who can own all aspects of the project, from the initial consultancy to the ongoing supply of qualified production parts.
Position sensors underpin modern industry, and continue to evolve in their performance and technology. The sensor electronics are a key part of this evolution, having direct influence on speed, accuracy and overall form factor. While off-the-shelf components suit some applications, manufacturers looking to truly differentiate their products must take the next step and explore the benefits offered by a custom IC.
www.swindonsilicon.com