www.ptreview.co.uk
06
'22
Written on Modified on
Expansion of the REGLOPLAS jetPulse series with jetPulse 100L and flowControl - Efficient cooling of demanding die-cast components with hotspots
Demanding die-cast components, such as structural components in the automotive sector (megacastings), place special requirements on the temperature control, in particular on the cooling of so-called hotspots. The jetPulse system from REGLOPLAS offers a reliable and economical solution for cooling hotspots in a die casting die with pinpoint accuracy and reliability.
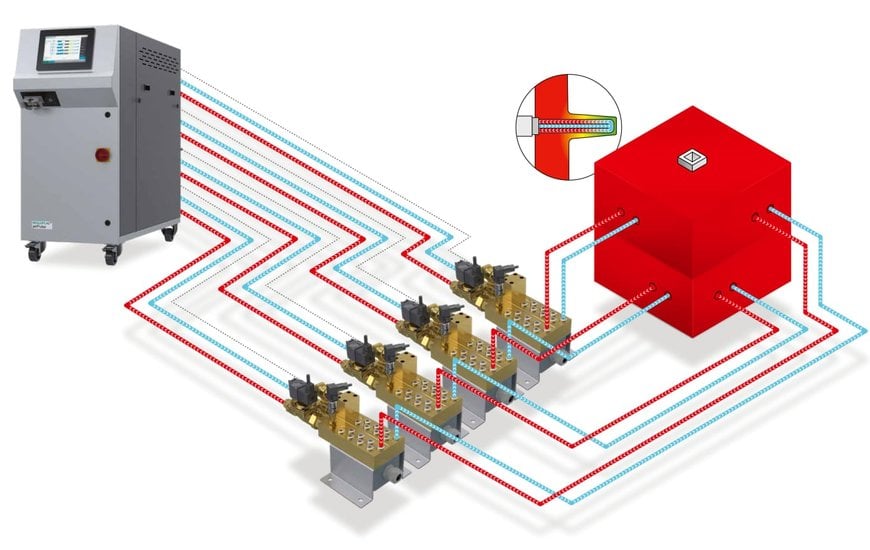
The spot cooling of so-called hotspots in die-casting dies is an established process for improving the quality and mechanical properties of components with demanding geometries and optimising the cycle time. The trend towards ever larger components, mainly driven by so-called megacasts in the automotive sector, has further increased the need for precise spot cooling systems and has raised the requirements. The jetPulse system from REGLOPLAS offers a suitable solution for every application, configuration and die size. As a supplement to the proven temperature control units and distribution systems for pressurised water and oil from REGLOPLAS, the customer receives a complete temperature control solution for his die casting machine from a single source, including the software for monitoring the entire system and with worldwide local support and service.
Flexible, adapted to needs
The REGLOPLAS jetPulse system offers two unit sizes (30 l or 100 l). Up to six multiJet distributors with 8 channels each can be connected per unit. These reliably cool up to 64 individual hotspots with pinpoint accuracy and cycle controlled. The system is supplemented by the flow rate monitoring of each individual channel with the REGLOPLAS flowControl. The system detects problems in individual cooling channels at an early stage and thus avoids costs due to quality problems and rejects at an early stage. A Profibus interface ensures simple communication between the jetPulse system and the die casting machine.
Powerful, intelligent and energy-saving
The jetPulse 100L has a frequency-controlled, multistage, low-noise pump with a flow rate of up to 100 l/min and a system pressure of up to 30 bar. The pump is equipped with an energy-saving function and is only active while cooling is running. Using intelligent technologies, the system monitors and controls the pump pressure, temperature, flow rate and output. This ensures excellent stability and the highest degree of safety during the cooling process. The intelligent process monitoring constantly checks the operating data and signals deviations from individually definable limit values before failures occur. Automatic core breakage and leakage monitoring is integrated in each jetPulse cooling cycle. This stops die casting machine immediately if an irregularity is detected in order to prevent possible damage to the tool. The complete system is individually controlled and parameterised in a simple and user-friendly way using the touch screen on the Siemens HMI panel, with easily understandable graphically assisted displays and representations.
Economical complete system from a single source
The jetPulse system offers customers an extensive system with a sophisticated component architecture from a single source. The robust and compact units can be easily and quickly integrated into new or existing die casting plants and deliver more process reliability, better and more stable product quality and shorter cycle times for demanding components with hotspots at low investment costs. jetPulse from REGLOPLAS yields lower unit costs and high component quality, thus sustainably improving competitiveness.
www.regloplas.com