www.ptreview.co.uk
03
'22
Written on Modified on
Customer requirements drive development of FANUC ROBODRILL α-DiB Plus
FANUC’s policy of listening to its customer base was the driving force behind the development of the company’s new ROBODRILL α-DiB Plus high-reliability, high-performance machining centre.
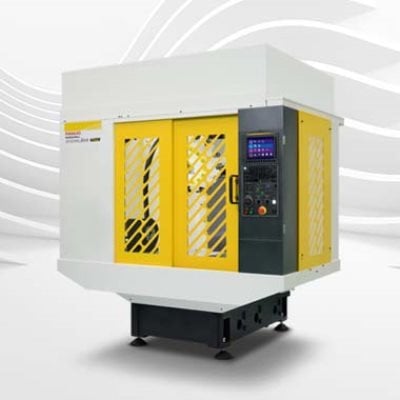
Enhancements such as higher spindle torque, intelligent feed control and support for punch tapping, are just a few of the customer-driven additions to the new ROBODRILL series, which also takes advantage of FANUC’s latest 31i-B Plus control.
“We have further developed our top seller based purely on customer feedback,” states Stefan Raff, FANUC’s Head of Sales ROBODRILL, ROBOCUT, ROBONANO Europe. “Here at FANUC we do not introduce new functions or features based on guesswork; all of the ROBODRILL enhancements are in response to specific needs identified by our customers. It’s the best ROBODRILL we have ever made.”
A case in point involves the growing industry requirement to machine reinforced workpiece materials. Many sectors, particularly transportation, are adopting lighter component materials to reduce weight and, in turn, fuel consumption. However, to ensure these parts maintain the necessary strength, they often feature an insert made from a stronger material, such as steel, which is where a machining centre with a high-torque spindle offers notable advantages.
The compact FANUC ROBODRILL α-DiB Plus delivers up to 100Nm with its new high-torque spindle, 70% more than the standard spindle. This torque rating is very high for a machine of its size, providing the potential to achieve class-leading cutting data in an economical way.
The smart choice
Increasingly intelligent functionality will be notable for users of the ROBODRILL α-DiB Plus. For instance, when the machine senses a rise in torque due to greater depth-of-cut at a certain component location, the machine will automatically reduce its feed rate to avoid triggering an ‘overload condition’ stoppage. Likewise, when depth-of-cut decreases, the machine will automatically increase to its previous feed rate.
Also new is the punch tapping function, which takes advantage of Emuge’s innovative Punch Tap™ tool. Traditional tapping involves rotating a tap into and out of a hole. However, the innovative shape of the Emuge Punch Tap™ creates threads with far less rotation, reducing tapping time by up to 75% in comparison with conventional thread cutting/forming/milling, while also saving energy. Developed to meet customer demand in the automotive industry, punch tapping is now a standard function on ROBODRILL α-DiB Plus machines.
Take control
Key to many of the latest ROBODRILL advancements is the FANUC 31i-B Plus control, which provides an excellent user interface for easy programming and set-up. Specifically for multi-axis, multi-path, high-speed, high-precision machining, the 31i-B Plus offer user benefits that include rapid machining with FANUC Fast Cycle Time Technology, high-quality finishes with Fine Surface Technology and increased SRAM memory for more flexible configuration of optional functions. From a connectivity perspective, the ROBODRILL α-DiB Plus supports all major industrial communication protocols to ensure customers can tap into the many benefits that real-time production monitoring and data analysis bring.
With a new control and enhanced communications, FANUC has also improved its DDRiB direct-drive rotary 4th-axis option, where the maximum speed is now 300 rpm (up from 200 rpm). In addition, FANUC has reduced the clamping time from 0.8 to 0.5 seconds, and increased the axis clamp torque from 500 to 700Nm. On the trunnion-style rotate DDR-TiB unit for 4-axis operations, the maximum load is now 200kg, up from 150kg, while the clamp torque has increased to 1100Nm, providing the ideal solution for larger workpieces such as EV battery housings.
As with all FANUC developments, the ROBODRILL α-DiB Plus offers energy-efficient performance: the machine only consumes electricity when necessary. Faster programming, checking and cycle times further support reduced power consumption.
A version for every manufacturer
As a high-speed all-rounder with suitability for all types of manufacturer regardless of batch quantities, the ROBODRILL α-DiB Plus is available in two versions: standard and advanced. The standard model is ideal for a large swathe of markets, including medical, watchmaking, electric mobility and general subcontract manufacturing. FANUC’s advanced ROBODRILL is typically for those with high-volume demands. This version offers more Z-axis travel, an even stronger column and bed, and a power failure back-up module so that the machine stops in a controlled way (avoiding damage to workpieces, cutters or fixtures) in the event of a power outage.
Three sizes (300, 500 and 700mm X-axis travel) are available in both standard and advanced versions, with all the usual options regarding factors such as number of axes (3, 4 or 5) and spindle speed (up to 24,000 rpm). In addition, FANUC can enhance any ROBODRILL investment via its extensive portfolio of industrial robots, with easy, simple connection between robot and machine.
www.fanuc.com