www.ptreview.co.uk
20
'21
Written on Modified on
NSK innovation overcomes long-standing bearing challenge in the mining industry
NSK has used its extensive problem-solving capabilities and experience to provide mines and quarries with the solution to a long-standing problem. Many conveyors operating in the hostile environment of a mine suffer from the premature failure of bearings on the head, tail, drive and tensioning pulley. There are numerous reasons why overcoming this issue has proved challenging over the years, but NSK has come up with a solution that improves service life by up to 20 times without comprising any other requirements.
To allow important accessibility, the head, tail, drive and tensioning pulley on mining and quarrying conveyors traditionally relies on open bearings. However, the short service life of these bearings frequently threatens the uptime of operations.Widespread problem
In Australia, mining is a pillar of the country’s economy, where downtime and costly repairs represent a danger to bottom-line profitability. Like in many other regions of the world, mining companies across Australia experience expensive maintenance and lengthy conveyor downtime due to the failure of tensioning pulley bearings. These bearings typically suffer from hard particles (dirt, dust) and water penetrating the housing seals and entering the open bearings.
As well as improving the sealing situation, any new solution would have to avoid compromising important user requirements, one of which is rapid mounting. As an industry-standard procedure, each spherical roller bearing slides quickly and easily on to a tapered sleeve. In contrast, bearings that mount on a regular cylindrical surface require heating and cooling to ensure a suitable shrink fit, not only taking time but requiring special equipment.
Tapered bearing bores and corresponding tapered adapter sleeves provide a faster and more convenient solution. The adapter sleeve has a cylindrical bore to slide over the end of the conveyor belt roller shaft, while the outside diameter of the sleeve features a taper to match that of the bearing bore. At the end of the adapter sleeve is a thread, where the application of a nut serves to push the bearing on the taper.
To know how much the spherical roller bearing requires pushing on the tapered surface, maintenance professionals use a feeler gauge to check the bearing’s internal clearance. This strategy ensures there is no over-exertion of force that could push the bearing too far up the tapered sleeve, causing too much reduction in internal clearance.
The beginning of change
The life expectancy of open spherical roller bearings for applications such as mining and quarrying conveyors is relatively short, typically just months. However, in the absence of a better solution, this somewhat unacceptable situation has prevailed for many years.
The first sign of a breakthrough arrived in 2012-13, when NSK Australia and its distributor began working closely with major mining companies across the country to set up several on-site trials in various problematic conveyor pulley locations where the mean time between failures (MTBF) was as low as 6 months.
NSK set out to develop a type of sealed spherical roller bearing that could provide a useful service life extension through highly effective seal design and the use of unique long-life bearing material. However, among the major challenges was accommodating the need for final radial clearance measurement. Only by using open bearings was it previously possible for feeler gauges to gain access. Using a conventional sealed bearing would prevent this critical operation from taking place.
Some bearing manufacturers have addressed this issue by offering standard sealed spherical roller bearings (featuring a tapered bore) with a set of conversion tables. These tables provide a correlation between the amount of axial push distance, a hydraulic nut oil pump pressure and how much the internal clearance is shrinking. However, this is a theoretical calculation that does not offer 100% certainty, leading to a percentage of mounting errors.
A brand new concept
To improve upon this approach, NSK came up with a world-first idea: a detachable seal. This concept centres on a seal mounted to a ring/holder that is fully detachable (via bolts), thus providing access for clearance measurements using feeler gauges (as well as the end user’s ability to select and pack their choice of grease at commissioning and re-grease if required). The NSK design requires no heat-shrink equipment and continues to make use of ISO-standard tapered adapter sleeves and locknuts, thus offering interchangeability with existing solutions.
Importantly, despite the addition of the detachable seal, there is no extension of the ISO-specified boundary width dimension, therefore permitting the use of standard bearing housings. NSK achieved this outcome by deploying its proprietary, independently certified Hi-TF/Super-TF bearing material to mitigate the design constraints of the seal.
This material increases the load rating by up to 10% (depending on size) in comparison with a standard open bearing, allowing the solution to remain within the same dimensional envelope. Mining companies can therefore quickly and simply swap their existing open bearings with the NSK solution; there is no requirement for a new housing.
As a point of note, Hi-TF and Super-TF bearing material provides twice the service life of conventional bearing material when operating with clean lubrication, and up to 10 times when operating with contaminated lubrication.
NSK’s solution also features proven heavy-duty nitrile (HNBR) seal technology capable of operating up to 100°C., providing 30% more effective sealing than standard industry concepts thanks to the use of spring-loaded lip technology. This design helps to deliver protection from contaminants and long service life.
Service life up to 10 years
Some of the trial spherical roller bearings fitted to mining conveyors by NSK Australia in 2012-13, remain in service with problem-free running. However, NSK removed one set (although working perfectly) after two years and sent it to the company’s R&D Centre in Japan for X-ray fatigue analysis. The result indicated that a residual life of eight years remained. So, together with the service time already achieved, NSK determined that a 10-year service life is possible, which is far in excess of anything previously witnessed by conveyor applications in the mining and quarrying industry.
NSK Australia has since supplied around 1600 long-life spherical roller bearings with detachable seal technology across the country’s mining industry. A full range of standard sizes from 120 to 480 mm bore diameter is now available worldwide, including in Europe. Some installations have already taken place in the Nordic countries, for example.
1) NSK’s long-life spherical roller bearings with detachable seal provide increased uptime and higher reliability for operators of conveyor systems
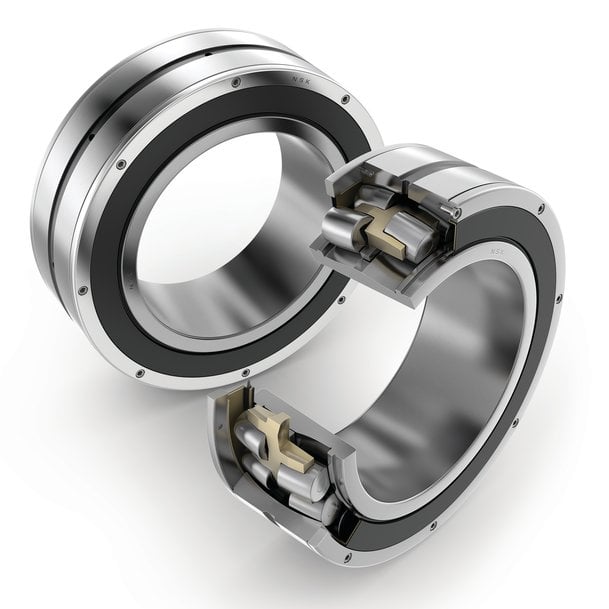
2) The seal is mounted to a ring/holder that is fully detachable (via bolts) to allow access for internal clearance measurements using feeler gauges
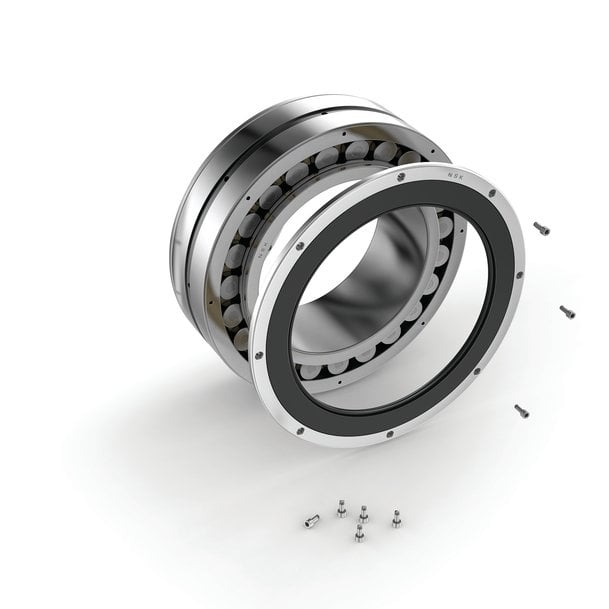
3) A cross-section of NSK’s long-life spherical roller bearings with detachable seal shows the inner ring, outer ring, seal holder and seal

4) The higher dynamic load rating of NSK’s Hi-TF/Super-TF bearing material mitigates the design constraints of the seal, keeping the bearing within the ISO-specified boundary width dimension
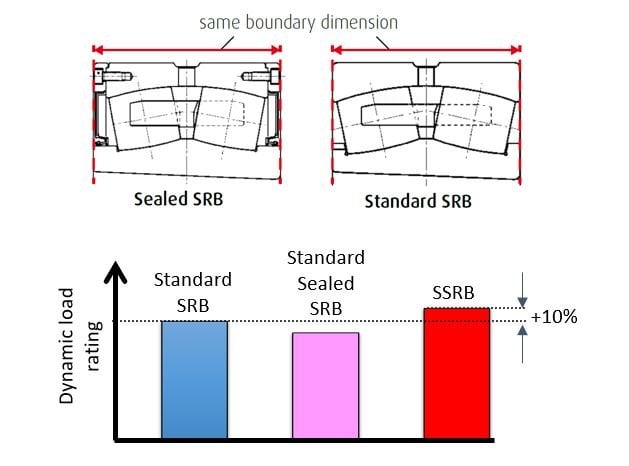