www.ptreview.co.uk
09
'21
Written on Modified on
STAUFF invests in another Riello rotary transfer machine
STAUFF – manufacturer for all components in hydraulic line systems – put a new Riello rotary transfer machine into operation. The machine produces elbow and T fittings from steel forging blanks for the STAUFF Connect tube connector range in all common sizes and versions.
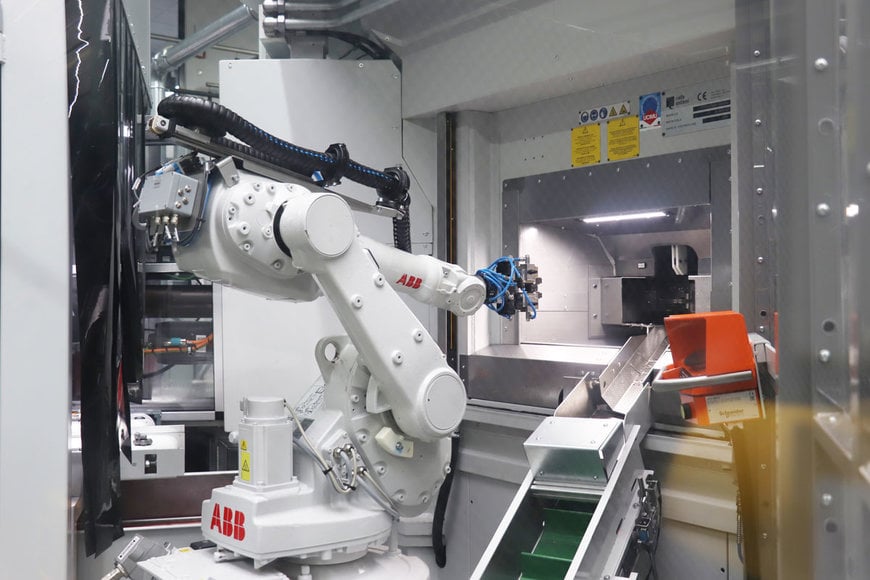
These rotary transfer machines are primarily designed for batch sizes from 5000 units per production run. The blanks are clamped in a fully automated process and multiple machining processes are executed in one flow, reducing tool changes and set-up times. For dealers and manufacturers of machines and systems, this ensures a high level of availability, even for short-term orders of large quantities.
Carsten Krenz, Managing Director of STAUFF Germany and Product Manager of STAUFF Connect Global, estimates that the “new” Riello will output 1.2 million workpieces in the future, for the production of small and medium tube connectors with sizes ranging from 8L/S to 18L: “The worldwide demand for tube connectors from STAUFF has increased disproportionally despite the difficult economic situation during the coronavirus crisis. Worldwide, there is high demand from retailers and from OEMs, in particular in the field of construction and agricultural machinery, in the railway industry and in the energy sector.” The company’s production sites in the South Westphalia region of Germany now run three rotary transfer machines. An investment of 6 million euros was already made in two machines from the Italian manufacturer Riello in 2018, only a few years after the market launch of STAUFF Connect. Demand has been continuously increasing since then, while the turnover in the first half of 2021 even grew by around 50 per cent compared to the same period in 2020.
The repeated forward-looking investments in high-performance machinery for efficient production of large batches guarantee a strong delivery performance for OEMs and dealers. Carsten Krenz is expecting a further increase in the demand for STAUFF Connect and sees the STAUFF Line concept as one of the reasons for this: “Our product range includes all components for hydraulic line systems developed and manufactured in house, meaning these are system-based, coordinated solutions, produced in house at a high-quality level.” The benefits for machine and system manufacturers go far beyond single sourcing, though. The STAUFF Line concept includes all services for hydraulic line systems – from concept development and configuration to the delivery of pre-assembled lines. The family-run company with subsidiaries in 18 countries is following a trend in international machinery and plant engineering: focusing on core skills while outsourcing others, for example hydraulics. “To meet this responsibility worldwide, investments are being made in equipment, such as in-house tube bending stations, at our international sites, so we can take over more and more production steps for our customers,” Carsten Krenz explains.
www.stauff.com