Global reach and innovation: Key to a healthy food chain in a year like no other
When Marel’s crucial role in the food chain was put to the test in 2020, the company’s global reach and focus on innovation proved essential to continuity.
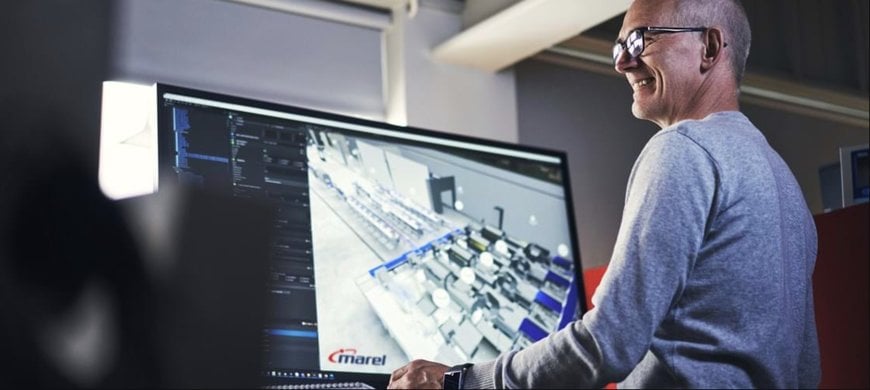
As the global community began locking down early in 2020, Marel quickly took measures to ensure the safety of its employees, the continuity of its manufacturing facilities, and the ongoing delivery of equipment, software and service to its customers around the world.
It was a year marked by unprecedented restrictions on human movement and interaction. As well as enabling safe, uninterrupted food production, Marel’s huge innovation arm also continued to flex its muscles to keep the long-term development of new technologies on track and quickly implement short-term changes that would prove essential for food processors to keep up production and supply during the pandemic.
Marel supports the production of safe, affordable, quality food to consumers worldwide. As a global company, we recognize the gravity of this shared responsibility. As always, it would be a question of how to act and adapt, not if.
A new reality
There was an abundance of hand sanitizer and a preference for elbow touches instead of handshakes at Marel’s 2020 Salmon ShowHow event in Copenhagen on 5 February 2020. Otherwise, it was business as usual. Almost 300 representatives of the global food industry attended the event, enjoying product demonstrations, seminars and guest speaker presentations.
Then, within just a few weeks, exhibitions and other events around the world were being cancelled due to the rapid spread of Covid-19.
Robotics and automation were already hot topics in food processing. Nobody predicted just how crucial these advances would become in the months ahead.
Keeping the food chain intact
Governments endeavored to safeguard the basic rights of their people to healthcare, food, water and education. Healthcare workers took position on the frontline. And all of us in the food processing industry became ‘second responders’, tasked with keeping food supply chains intact.
Marel’s vision is of a world where quality food is produced sustainably and affordably. Covid-19 did little to change our priorities, but it did alter the way we can best accomplish them. From how we perform routine maintenance to enabling greater automation in process lines, 2020 saw the company release more than 30 innovations.
Automation gains momentum
Automation in food processing isn’t a recent development. Since the first canning factories of the 19th century, each industrial revolution has meant a jump in the level and nature of that automation.
With the onset of Industry 4.0, two of the major trends in automated food processing are digital transformation and robotics.
Robots are becoming smarter, more collaborative by design, more digital (so more connected with overall production) and cheaper to produce, operate and maintain – all very appealing characteristics in the food processing industry.
Robots in food production
The manufacturing industry as a whole installs more than 350,000 industrial robots per year. The food and beverage industry accounts for around 3% of this total, installing more than 10,000 robots per year.
Food processors can increasingly use robotic solutions to help meet challenges such as labor availability, ergonomics, food safety and higher yield and efficiency. In addition to increasing automation, robots enable greater scalability and flexibility.
Robotics innovations at Marel’s February event included:
- A prototype depalletizing robot that moved and emptied heavy boxes of salmon, as well as automatically cutting the box straps
- A RoboBatcher Thermoformer demonstrated as part of a fully automated fixed-weight tray solution packing fresh portions into a Thermoformer
Later in the year, Marel released another exciting innovation for salmon processors – the I-Slice 3400 Retail Pack Slicer. This solution uses the latest weighing and slicing technology to ensure exact weighing, cutting and placement of slices, with automatic board size matching.
In other sectors, Marel advances in automation during 2020 included:
- The M-Line Robot product release – Representing a new generation of slaughter robotization in pig processing, complete with 3D scanning that ensures very high cutting accuracy.
- The WPL 9000+ Automatic Weigh Price Labeler product release – A high-speed machine that applies printed, self-adhesive labels with catch or fixed weight information to packaged food products.
- SensorX Magna product release – A high-capacity, inline trim inspection system that revolutionizes the mixing and grinding process.
- Joint creation of an AI-enabled Manufacturing and Maintenance (AIMM) lab – Setting out to improve decision-making in manufacturing and maintenance using artificial intelligence, as part of a project with Eindhoven University of Technology (TU/e) in the Netherlands.
“And we took significant steps forward in combining vision and robotics technology and cascading knowledge and insights from one industry to another,” says Hildur Einarsdottir, Automation Program Manager, Marel Innovation.
Digital transformation comes to food processing equipment
The innovations mentioned here assume a high level of automated data management. More than ever, in the past 12 months comprehensive software has become a vital element of modern food processing.
Food processors need to be in control of what’s happening in every area of operation – throughout every process, every device, every action. To achieve this, they need real-time information: data on customer orders and stock levels, machine performance and operator productivity, product quality and traceability, and so forth.
Marel’s Innova food processing software is the tool that does all this, with modules covering everything from individual device control to complete factory solutions across multiple sites.
Business continuity and competitive advantage with Innova
Factories already operating with Innova software had a clear advantage above less digitally mature competitors during 2020. With Innova, managers have full control of the production process, making it easy to analyze costs, plan production, make the best use of available labor and raw materials, all the time confident in the knowledge that they have full traceability.
In short, Innova makes food processors much more agile – a crucial advantage in turbulent times.
The food processing industry has to be agile enough to adapt to fluctuations (in staffing, raw materials, order demands etc.), to prevent stoppages (by being in better control of hardware performance and maintenance) and to avoid recalls (by instantly being able to trace irregularities back to the source and forward to finished products).
These challenges are not new, but they were compounded by the consequences of the pandemic. So agility has become more critical than ever to food processing, especially to business continuity. Innova helps keep production running.
Irish poultry producer Moy Park uses Innova software to manage processes from a central control room, where dashboards show key production indicators in real time. As David Anderson, Director of IS and Business Solutions at Moy Park, explains:
“We are so glad we invested in Innova. It has added value to our operation and has given us competitive advantage. We are sure that we will recoup its cost many times over.”
When CEOs, production managers, quality inspectors and others convened online for Marel’s Software KnowHow in April, gaining this type of competitive advantage was an underlying theme of the event.
From demonstrating established traceability solutions to announcing upcoming software launches, the webinars, demos and conversations helped guide food processors toward greater agility as part of their digital journey.
Food processors adapt to 2020
Regardless of the level of automation in their factories, the food processors attending Marel’s online events had many of the same interests, concerns and plans that they’d had for years. But they were all facing new ‘2020 challenges’ too.
Limited manual labor, for example, which has always been a challenge in food processing, was compounded by social distancing requirements and travel restrictions, becoming a real threat to the stability of the food supply chain.
Even when workers were able to travel to work, they were no longer allowed to stand close together on production lines.
While not a complete solution in itself, investment and interest in automation in general – and robotics and software in particular – quickly accelerated during 2020, as the industry realized how vital they would be to navigating the way ahead.
“In a scenario like this, certain manual operations become difficult to be done efficiently and within certain required standards, which makes automation attractive from an economic point of view and for quality too,” says Ruud Berkers, Marel Sales Director for Latin America.
In an ideal world, a processing plant achieves high utilization of the raw material, uses minimal manual labor, makes safe, high quality products sustainably, and does all this while making a healthy profit. This is nothing new, but the events of 2020 clarified how greater automation helps processors get closer to that ideal.
In terms of production equipment, we’ve seen that automation enables a higher level of accuracy – in cutting and weighing, for example – which in turn reduces giveaway. Automation reduces the amount of manual handling, which improves product quality. And automated data collection puts processors in control of every process, device and action.
But how does automation help set everything up and keep it running smoothly?
Remote service
During February’s Salmon ShowHow, attendees entered a virtual processing facility using Marel’s augmented reality (AR) technology. Among other things, this gave people an insight into how routine service might be performed remotely, sometime in the future.
That future arrived sooner than expected. As travel restrictions kicked in, Marel quickly extended its capability in remote service.
Remote service via AR and a headset was no longer a futuristic demo. It was now key to providing ongoing support to customers. Armed with specially designed headsets, Marel service engineers began using AR technology to tap into expert knowledge from dedicated Marel support operatives, stationed all over the world.
Fast forward six months and this technique is now routine.
Marel has local service personnel based in over 30 countries, but in order to provide top service and support across all stages of processing in a number of industries, Marel’s extensive service network often pairs a local service engineer with an expert based elsewhere. We used to hop on a plane to achieve that – now we connect remotely.
Even if the engineer has no experience at all with a specific piece of equipment, this real-time remote assistance effectively places the relevant expert right next to them, providing as much guidance as required.
The expert who is not on site can take over the headset camera via remote control and, as a bonus, the local engineer gains new skills via immersive, interactive on-the-job training.
Without Marel’s established network of local service personnel, this solution would not have been possible. Our catchphrase “global reach, local solutions” certainly rings truer than ever.
As we enter 2021, Marel continues to ship dozens of headsets to its service people, so that more of our customers will be able to benefit from this technique.
Maintaining our partnerships with the industry
Besides service and installations, extended reality is now a much bigger part of Marel’s interaction with the industries at events too.
In April 2020, Marel hosted its first ever online global expo – in lieu of the annual Seafood Processing Global exhibition in Brussels, which had already been postponed indefinitely.
This was one of more than 20 online events Marel held for customers during 2020, where attendees walked around virtual exhibition booths, interacting with the machines, and exchanged ideas with our experts during lively online Q&A sessions, as well as during private conferences following events.
“Extended reality solutions, like VR, have allowed us to have meaningful conversations about our solutions with our customers without travel and face-to-face meetings,” says Haukur Hafsteinsson, Embedded Software Engineer at Marel.
Innovating the future: Every step counts
Marel’s mission is to transform the way food is processed and the company has a long history of working in partnership with its customers in the food processing industry to address current challenges and prepare for future ones, all the while having a positive impact on societies, the environment, business opportunities and profits.
Automation, digitalization and sustainability set the drumbeat to Marel’s innovation activities for the past year and continue to do so. Our cooperative work focused on these themes made 2020 a successful year, despite the challenges, and we brought over 30 breakthrough innovations to the market.
“With our global and local teams, we delivered new solutions and progressed on great innovations using digital solutions and virtual reality to test and develop along the way,” says Anna Kristin Palsdottir, EVP Innovation at Marel.
“We have over 1,000 innovation experts around the world and each one has helped make it possible for us to take another step forward, and then another. Every step counts.”
Innovation is key to making sure the food supply chain is strong and reliable, now and in the future. At Marel, innovation is as much about developing and utilizing new technologies as it is about securing a continuous flow of solutions and services to our customers.
This past year, as always, it’s been about pioneering exciting new ideas in collaboration with the food processing industry and following through until they become real and practical applications.
All the same, we hope the food processing industry – and the world as a whole – has a less tumultuous year ahead.
www.marel.com