www.ptreview.co.uk
20
'21
Written on Modified on
The dual channel principle
The dual channel principle is just one of many new developments within the scope of Leuze's nearly 60 years of innovation history.
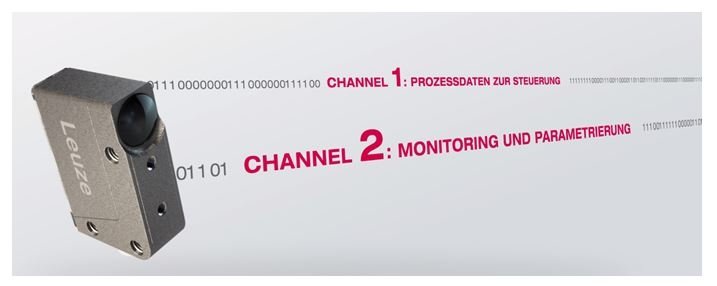
What does dual channel actually mean?
The increasing digitization opens entirely new possibilities in automation technology for increasing the productivity and efficiency of machinery and systems. A much more precise look into the machine is possible today than in the past. It is possible to obtain much more detailed and, in addition, constantly available condition information about the machine – not only on-site, but also remotely, and in digital form. An increase in the amount of information also means ever larger amounts of data, not to say a flood of data, that must be managed. New strategies, expertise and future-oriented technologies are necessary here. Leuze accepts this challenge and develops smart sensors. Smart means sensors that, on the one hand, record the relevant real-time process data, but, on the other hand, can also supply a great deal of additional information which, once evaluated, can provide information at any time about the current machine state.
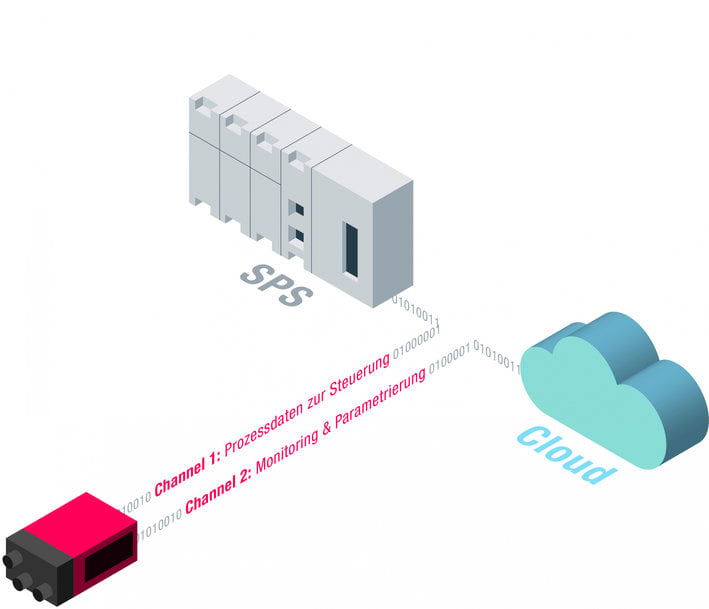
Dual channel principle from Leuze
To ensure the that the information reaches the desired recipient – be it the process control, the operating company or even the appropriate machine support service – new communication technologies are needed. In addition to offering sufficient bandwidth (e.g., industrial Ethernet interfaces), these must also provide multi-channel capability. Only in this way can the data be delivered in a targeted manner and processed further. This is precisely what the innovative dual channel principle from Leuze offers. First: A real-time process data channel and, second, a need-oriented information channel for exchanging status information and configuration settings.
And what exactly is Industry 4.0?
The primary idea behind Industry 4.0/IIoT is to standardize data and the way it is exchanged across all system borders and all the way up to the cloud. Most of this data is generated with the help of sensors. Their job is to capture process variables and transfer these in the form of data to the receiving systems via one or more interfaces.
Through Industry 4.0/IIoT, additional and even new topics, such as a recipe change, a format changeover or the condition monitoring as well as the predictive maintenance of a machine or system are increasingly shifting into focus. The data required there is, however, often not essential for the actual automation task. But it does make it easier for the user to plan for maintenance. Preventative maintenance intervals ultimately increase the availability of the machine or system since the maintenance can be performed before the machine or system comes to a standstill with the associated loss of productivity.
Leuze communication solutions within the scope of Industry 4.0/IIoT
In the past, point-to-point connections between the control unit and the respective sensor or actuator have defined industrial automation. A master-slave communication model currently prevails. This means that a control unit usually serves multiple end devices via one cable in linear topology (fieldbus installation). The use of new technologies will allow a transition to a netlike or star-shaped communication architecture. We are already accustomed to this from the IT field.
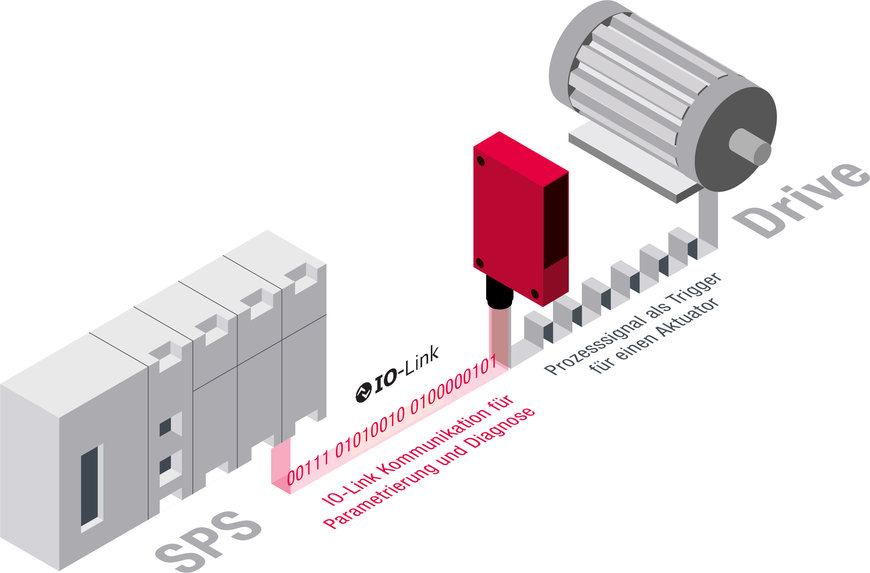
Dual channel with connection to the PLC
As the interfaces to the control systems are increasingly Ethernet-based and therefore powerful enough to serve two data channels simultaneously, this is opening up completely new possibilities. These are necessary for the networked world of Industry 4.0 and deliver the data to the various receivers in a target-oriented manner. With two data channels, the basis for this already exists, i.e., through the integrated industrial Ethernet interface with additional TCP/IP channel and the possibility to expand it for OPC UA communication – and even to new cloud-based applications in the integrated connectivity devices. The latter are denoted at Leuze with a red i in the type designation. This is precisely where IO-Link is indispensable: this simple, 3-wire interface offers all functions that are needed for new IIoT approaches, such as asset management or condition monitoring. It can also be economically integrated in the smallest of devices.
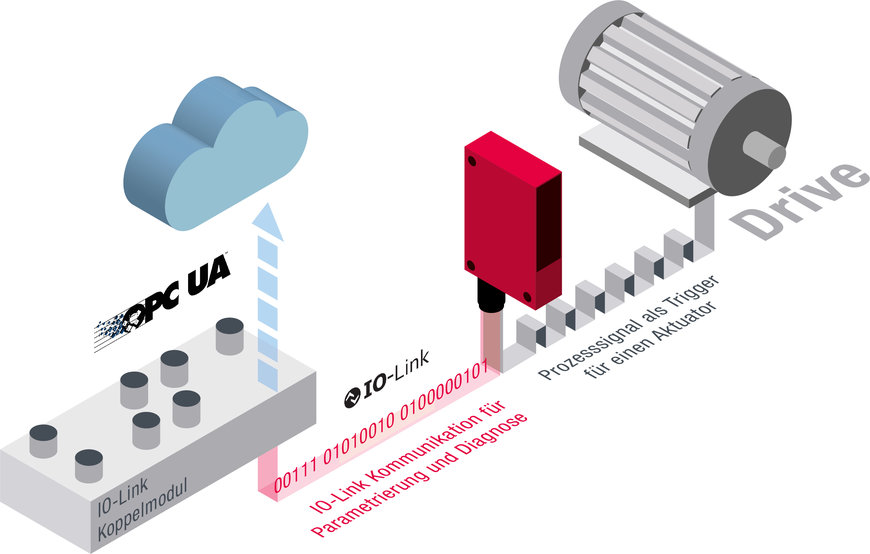
Dual channel and Industry 4.0/IIoT with a binary-switching sensor
Dual channel in practice
Nevertheless, the original measurement task of the sensors cannot be forgotten – especially as many highly dynamic applications are heavily dependent on all process-relevant information with respect to time. In combination with the newly emerging application possibilities, the dual channel principle from Leuze supports precisely this requirement. The data is transferred to the process control in real time via the first sensor channel. At the same time, the information for monitoring and analysis of the machine flows over the second channel. The classic IO-Link interface for the binary switching sensor cannot achieve this. In SIO mode (Standard IO Mode), it permits only one switching signal. During active point-to-point communication, it can handle no more than the direct data exchange of the control. For the process control, however, both types of information are necessary in parallel but with different time requirements. The dual channel principle is the same for all sensors with one or more integrated data interfaces – regardless of their complexity. In the following, we consider and differentiate between two possibilities for a binary switching sensor: first, the dual channel principle with connection to the PLC. And second, the dual channel principle with respect to Industry 4.0/IIoT. In addition, we consider dual channel for sensors with fieldbus interface.
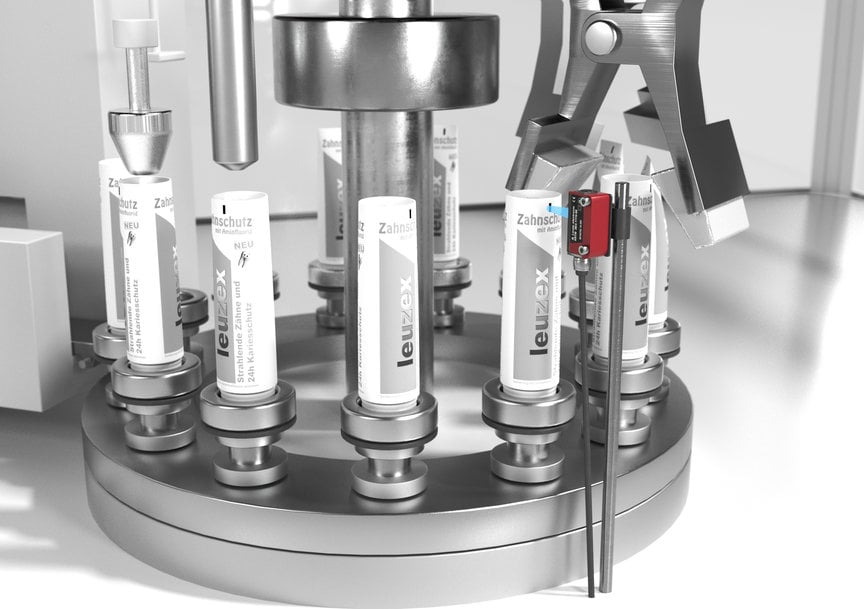
Determination of the print mark position with the KRT 3B contrast sensor
1 Dual channel with connection to the PLC
Consider as an example the KRT 18B contrast sensor, which is used in extremely fast-running packaging machines to determine an exact print mark position: here, the packaging quality of the machine is dependent on the real-time capability of the switching output. The trigger signal from the switching output of a contrast sensor is therefore not processed via the control but is rather connected directly to the actuator. This then directly triggers the placement of a label without time delay. (Figure 2). In addition to the fast reaction time of the machine, the exact teaching of the contrast differences between print mark and background is largely responsible for the reliable operation of the machine or system. Optical contrast sensors such as, the KRT 18B, offer the possibility to determine the optimum contrast ratio for each container or label using multiple transmitter colors. For this reason, the KRT 18B is also equipped with an IO-Link communication interface in addition to the fast switching output. Using a teach routine, the transmitter colors are taught in once and then stored in the respective sensor or the control. Defined or taught-in products can then be selected from the recipe memory of the sensor at any time via IO-Link. If the machine undergoes a format change, the entire configuration file is transferred from the control. This eliminates the need for another teach-in process. (Figure 3).
2 Dual Channel and Industry 4.0 / IIoT
Within the scope of Industry 4.0/IIoT, data needs to be available to other automation participants, independent of location and worldwide. This is used, for example, for monitoring and configuration. Cloud solutions are generally selected here. Provided the prerequisites identical to those described above exist, the connection can be made via a decentral IO-Link coupling module with Ethernet interface and OPC-UA communication protocol instead of the direct IO-Link connection to the PLC. The data is then connected to the cloud via, e.g., an IoT Edge gateway. (Figure 4). As per the practical example from the area of bottle filling as follows:
Within the scope of Industry 4.0/IIoT, data needs to be available to other automation participants, independent of location and worldwide. This is used, for example, for monitoring and configuration. Cloud solutions are generally selected here. Provided the prerequisites identical to those described above exist, the connection can be made via a decentral IO-Link coupling module with Ethernet interface and OPC-UA communication protocol instead of the direct IO-Link connection to the PLC. The data is then connected to the cloud via, e.g., an IoT Edge gateway. (Figure 4). As per the practical example from the area of bottle filling as follows:
Transparent objects, e.g., glass or PET bottles, on a conveyor belt must be reliably detected during the ongoing process – even in cases of challenging environmental conditions such as fogging, water vapor or soiling. Through the use of a retro-reflective photoelectric sensor for transparent objects with IO-Link – such as the Leuze PRK 3C, PRK 55 or PRK 18B – such environmental influences can be detected and appropriately analyzed so that the machine control can respond accordingly. (Figure 5). A fast trigger signal is needed in this case as well. For example, to trigger an inspection camera or eject faulty parts. In addition to the convenient teach-in using IO-Link, the second channel can be used to realize a simple but effective contamination monitoring system. The received signal level of the sensor can be compared with the set switching threshold at any time for this purpose, thereby allowing a reduction in the function reserve to be detected. If this information is transmitted to the person responsible for the machine or system, e.g., via the OPC UA interface of the IO-Link coupling module, the necessary cleaning measures can be determined from the analysis of this information and scheduled during breaks without interrupting production (predictive maintenance).
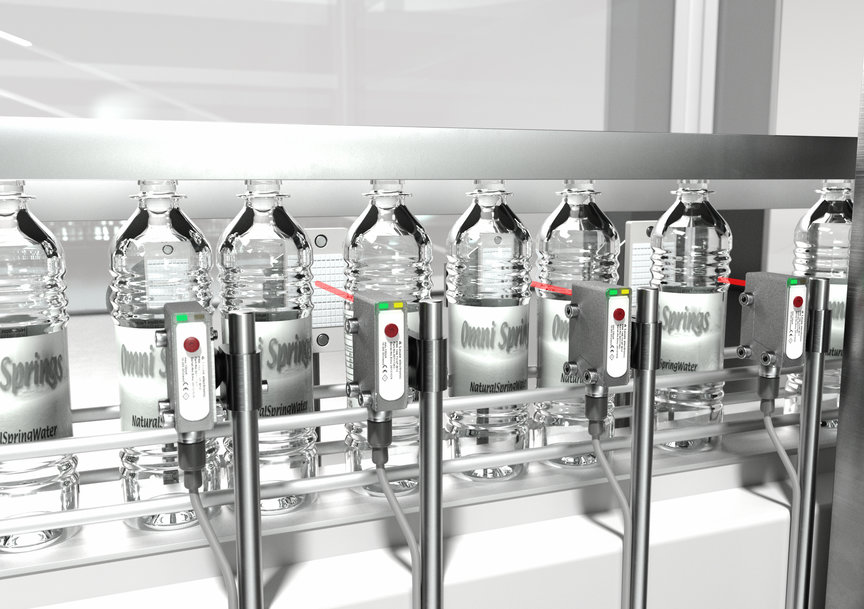
Reliable detection of transparent objects with the PRK 3C, PRK 55 or PRK 18B retro-reflective photoelectric sensors
3 Dual channel with sensors with fieldbus interface
Leuze offers a dual channel solution for more complex sensors with an integrated fieldbus interface as well. The BCL 348i bar code scanner, for example, primarily has a PROFINET fieldbus interface. Process and alarm values, detailed status and diagnostic messages as well as the complete device parameterization can be carried out from the control via this interface. If the data needs to be available location-independent and worldwide for monitoring, the sensor offers this possibility via its industrial Ethernet interface with the OPC-UA communication protocol. Via an integrated cloud connector or an IoT Edge gateway, the data can be transported all the way to a cloud application. (Figure 6).
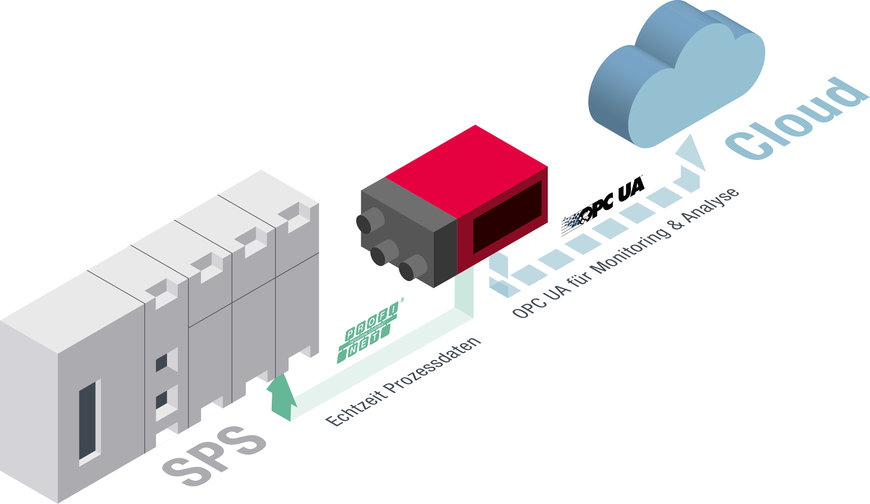
Dual channel and Industry 4.0/IIoT with fieldbus interface sensor