www.ptreview.co.uk
22
'20
Written on Modified on
Pick, Place and Package from Above
With high payload, large reach, and high performance, the DR-3iB/8L heralds a new age of versatility for delta robots
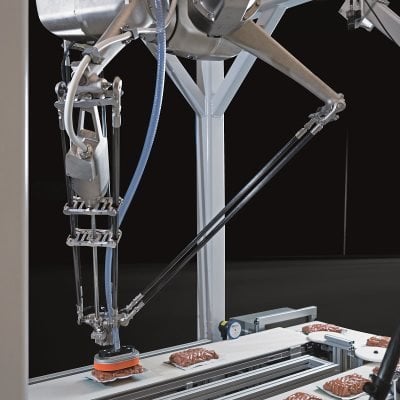
The dimensions and reach of the DR-3iB/8L make it easy for line builders to integrate this delta robot into pick-and-place applications of all sizes. Thanks to its huge workspace the model can cover wide conveyor belts, but also pack deep into a box. The advanced motion performance, with a motion speed of up to 10,000mm/sec, makes the DR-3iB/8L to the perfect choice for typical pick-and-place as well as packing applications, e.g. in the food and pharmaceutical industries.
At the same time, the high payload and wrist inertia make the DR-3iB/8L a viable option for a number of other applications. “The model supports larger grippers than typical delta robots, allowing larger parts to be handled or multiple parts to be picked up”, explains Thomas Schneider, Product Manager Robotics at FANUC Europe GmbH. Thus, the DR-3iB/8L can be used in packaging larger or already grouped goods, but also to support the assembly of e.g. solar panels or battery packs. Compared to a serial link robot, a delta robot setup takes up a lot less floor space, as it is mounted above the line. It is therefore particularly attractive for line builders who have to offer an optimal automation solution under severe space restrictions.
Ease of installation, operation and maintenance needs were also kept in mind in the development of the DR-3iB/8L. A hollow wrist design (Ø= 20mm) neatly contains the cable pack inside the robot, both to protect it from mechanical interference and to facilitate clean installation. Viewing windows on all major axes’ reducers allow the user to easily detect grease or oil collecting in the secondary catch basins. Maintenance can therefore be initiated before any problems occur. A freely accessible brake release switch (option) on the J # 1 housing enables the operator to carry out maintenance work easily and to quickly resolve any faults. An additional advantage of the newly designed robot is that the angled outer surface of the robot allows liquid to flow away after cleaning without contaminating the products on the conveyor belt.
The first model of the new-generation delta robots will be available with two different surface finishing’s. It is either painted or plated to achieve a smooth/clean surface, but both types surface can be used for food applications. The plated variant has an additional advantage, as the risk of paint chipping off into the food goods is eliminated. In general, the DR-3iB robots are equipped with food grade grease in all axes and resistant against acid and alkaline cleaners and disinfectants, to be prepared for wide market requirements.
The DR-3iB/8L is powered by the R-30iB Plus controller which supports FANUC’s image processing tool iRVision®, the logistics software iRPickTool® and conveyor tracking, the application enables picking on the fly and significantly increases productivity. Of course, the new generation delta robots also support all other state-of-the art FANUC Robot software. Our ROBOGUIDE® simulation software for feasibility can check a picking or packing project in respect of throughput, reach and robot durability in advance without taking a financial risk or creating expensive mechanical designs. Thus, FANUC can offer a one-stop solution for varied picking and packaging applications.
www.fanuc.com