www.ptreview.co.uk
06
'20
Written on Modified on
Flexible power consumption with SynErgie: smart solutions for production facilities
The volatile output of electricity from wind farms and photovoltaic plants can pose a real headache for energy companies.

This is because of the need to maintain a stable supply of power at all times, even when such facilities are generating little or no electricity. Part of the solution to this problem is to adapt the power consumption of production plants to the fluctuating output from wind and solar generation. Researchers from the Fraunhofer-Gesellschaft have now piloted this innovative concept in the Augsburg region. The results have been encouraging so far: the team has been able to show that energy-adaptive production – adapting industry’s consumption of power to the actual generating capacity – not only works in practice but also reduces CO2 emissions.
In the face of climate change, the need to expand wind and photovoltaic power is widely accepted. Indeed, without a large-scale restructuring of the power supply, it will be impossible to meet the ambitious goals targeted by the transition to a sustainable energy system. Yet the problem with electricity from renewable sources is that it fluctuates constantly, in line with the weather conditions and the time of day. Being reliant on a highly volatile source of energy means that power companies regularly have to take action, sometimes at considerable cost, in order to ensure a reliable supply of electricity at all levels of demand.
Such measures include adjusting power plant output, diverting power into distribution networks and, ultimately, expanding grid infrastructure. Battery storage is also a potential solution here. This, however, remains impracticable on account of the scale of volatility and the high investment costs.
The Fraunhofer Institute for Casting, Composite and Processing Technology IGCV has now come up with a new approach to managing fluctuations in the power supply. This research forms parts of SynErgie, a project under the overall coordination of Fraunhofer Institute for Manufacturing Engineering and Automation IPA and in cooperation with Fraunhofer Institute for Integrated Circuits IIS IIS, for Machine Tools and Forming Technology IWU and for Applied Information Technology FIT, with the Fraunhofer FIT project group Business & Information Systems, and with further partners from industry and science.
It is designed to offset fluctuations in renewable energy by making adjustments to the consumption of power by industry. SynErgie is one of four projects within the Kopernikus research initiative, which is investigating the transition to a sustainable energy system. The German Federal Ministry of Education and Research (BMBF) has supported the first phase of the project, from 2016 to 2019, with funding of 120 million euros. 30 million euros went to SynErgie.
The project is now in its second phase, also with a duration of three years. The BMBF has since pledged to extend the project to a third phase.
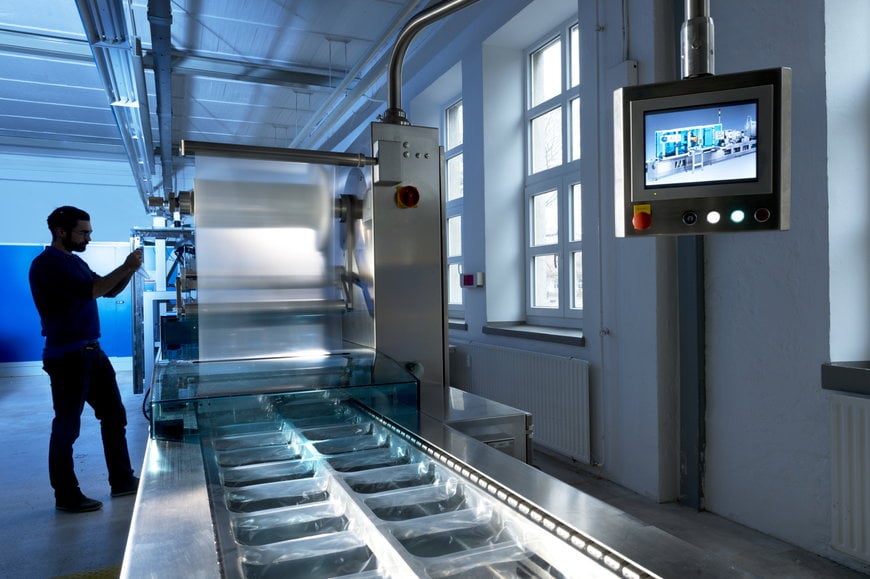
Demonstrator equipment at Fraunhofer IGCV – here a thermopackaging machine – shows how plant and associated machinery can be operated on an energy-adaptive basis.
Power consumption is synchronized with power generation
The idea behind SynErgie is to adjust industry’s power requirements to actual generating capacity. This involves scheduling production processes that consume a lot of electricity for periods at which there is an abundance of sunshine and wind. In turn, when wind and photovoltaic generation abate, preference is given to plants with low power consumption. In specific cases, the use of energy-intensive machinery can also be scaled back temporarily. Despite such measures to adjust power consumption, companies continue to meet their production targets.
The SynErgie project was able to provide proof of concept during the first funding phase from 2016 to 2019 and also showed that this approach ultimately yields significant reductions in CO2 emissions.
The research team opted to pilot the project in Augsburg and surrounding area, where there is a representative cross-section of German industry, including companies from the engineering, metal-production, metalworking, paper, chemicals and plastics sectors. Renewable energy currently accounts for around 35 percent of the region’s total power supply. As such, Augsburg and the surrounding area represent a typical German industrial region. It is therefore an ideal location to investigate the potential of energy-adaptive production, to identify any associated problems and to implement prototypical solutions.
SynErgie focuses on energy-intensive processes
The research team focused primarily on energy-intensive plants and processes. “In particular, those sectors that consume a lot of power have plants and equipment that can be made more energy-adaptive,” explains Stefan Roth, research associate and project manager at Fraunhofer IGCV. “And given the scale involved, this has a tangible effect on the power supply system.” Processes that are especially energy-intensive include smelting in foundries, forming in steel fabrication and pulp production in the paper industry. Researchers also wanted to discover whether measures to implement energy-adaptive production had an impact on output and on the energy balance.
This is particularly relevant when production is temporarily scaled back and then ramped up again, since it often takes a lot of power to restart production machinery. The team used simulations to analyze the impact that greater flexibility in power requirements would have on production targets, efficiency, the performance of production machinery and the overall energy balance of the company as a whole.
The results show that energy-adaptive production facilities can be made cost-efficient and that the carbon footprint of the overall system can be reduced. “The implementation of three prototypical measures to introduce energy-adaptive production in the Augsburg region has an impact on the regional energy balance equivalent to a medium-sized fossil-fuel power plant,” explains Jana Köberlein, research associate at Fraunhofer IGCV. “Moreover, as a result of the greater share of renewables in the fuel mix, CO2 emissions from power generation also fall.”
Electricity prices incorporated in the ERP system
How do companies receive up-to-date information on the level of power generation? Here, data from power exchanges can play a role, since fluctuations in generating output have a direct effect on the price of electricity. On platforms such as EPEX SPOT, the megawatt price depends on the time at which the power is consumed, among other things. The idea behind energy-adaptive production is therefore that the companies’ own enterprise resource planning (ERP) systems should incorporate not only company-internal data but also the current price of power along with forecasts as to its future movements.
This enables production planning to schedule operations on the basis of all the relevant parameters and data – and thereby reduce energy costs without endangering production targets or, worst of all, compromising product quality. “Production planning dynamically aligned with the energy market is the key to implementing energy-adaptive production,” says Lukas Bank, research associate at Fraunhofer IGCV. “By creating a mathematical model of individual process steps along with plant availability and delivery deadlines, an algorithm can then draw up a production plan that is optimized for cost, and this plan can be represented graphically.”
Present and future benefits for companies
In the first instance, therefore, SynErgie is attractive for energy-intensive companies. In the future, however, small and medium-sized enterprises might also benefit from this new system, since it could enable them to avoid expensive periods of peak load, for example, or to market their own aggregate capacity to adapt their production operations to supply levels.
If industry succeeds in adapting its consumption of electricity to the actual level of generation, then power companies will require fewer conventional power plants with which to offset fluctuations in generating capacity, and the need to rapidly expand the power grid will also become less urgent. At the same time, an intelligent technology mix will ensure that better use is made of regional generating capacity and help to establish Germany as a leading market for energy technology.
Fraunhofer IGCV and partners are working on other pilot projects in the Augsburg region. In particular, they are installing software platforms for industrial partners, which are to be tested in conjunction with regional grid operators.
www.fraunhofer.de