www.ptreview.co.uk
21
'20
Written on Modified on
NSK adds manufacturing technology to its core focus areas
For many years NSK has focused its development competence on the company’s four core technologies of tribology, simulation/analysis, mechatronics and materials engineering. Now, these core areas are being joined by a fifth: manufacturing technology. The move to ‘four core technologies plus one’, highlights the increasing importance of optimised machines, systems and equipment in the manufacture of high-quality bearings. Moreover, through this addition NSK is acknowledging the growing influence of global trends such as the IoT, Industry 4.0 and artificial intelligence (AI).
When NSK develops new generations of bearings, the key objectives that the company seeks to attain include higher speeds, lower friction, improved energy efficiency and prolonged service life, even under harsh environmental conditions. In short, NSK focuses on core technologies which offer the greatest leverage for improving the characteristics and performance of bearings.With a fifth core technology that centres on manufacturing, the company is underlining the meticulous approach required to produce high-quality bearings that help maximise both precision and efficiency.
NSK’s production capabilities are mostly developed and optimised in-house, which is advantageous because its international network of 64 production plants in 13 countries utilises state-of-the-art manufacturing technologies. Many of these technologies make use of digitalisation strategies to enable highly efficient, flexible and sustainable production. For instance, utilising the IoT, NSK increases the optimisation of its factory network by equipping manufacturing technology with AI. The company also works to realise the creation of smart factories that save on space and energy, and reduce manpower requirements.
Investment in the other four core technologies will of course continue in the future. By way of example, with the latest high-efficiency deep groove ball bearings for electric motors, NSK demonstrates improvements that can be achieved through intelligent tribological development work. For these bearings, the company’s tribologists have developed EA7, a grease that reduces internal friction. In conjunction with optimised grease filling, this innovation not only leads to significantly reduced friction and, subsequently, higher energy efficiency, but doubles the service interval for electric motors.
NSK’s impact in this area has been recognised by an award from the Japanese Society of Tribology (JAST), which recently presented NSK with the Tribology Technology Award 2019. The award was conferred for a research project that, for the first time, enables the very precise simultaneous measurement of lubricant film thickness and rupture rate in grease-lubricated bearings operating at low speeds. The findings from these measurements contribute to the development of low viscosity and friction-reduced lubricants that reduce the required torque and, in turn, cut CO2 emissions to help prevent global warming. Despite their low viscosity, lubricants of this type enable energy-efficient rolling bearings to benefit from long service life.
Masayuki Maeda, member of NSK Central Research, with the "Tribology Technology Award" conferred by the Japanese Society of Tribology.
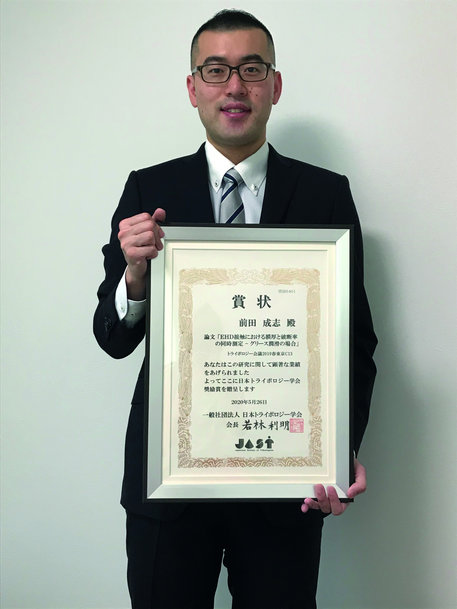