www.ptreview.co.uk
11
'20
Written on Modified on
NSK lubrication units create savings at roof tile plant
A ceramic roof tile manufacturer is saving €4,950 a year by switching to NSK K1 lubrication units for its handling machinery. The move has dramatically reduced the previous labour and downtime costs associated with re-greasing the integral linear guides.
Tile manufacturing plants are subject to harsh operating environments where the ingress of ceramic dust and other contaminants prove detrimental to machinery such as handling equipment. Here, poor lubrication on the steel balls of the linear guides can lead to the requirement for regular re-greasing in order to maintain the smooth linear motion and fixed preload needed for successful operations.Frustrated with the downtime and costs incurred across its six handling machines, the roof tile manufacturer turned to the expertise of NSK and its AIP Added Value Programme. Specialist NSK engineers performed a full application review that highlighted the need to improve both the lubrication and sealing performance of the system.
NSK recommended the adoption of its K1 lubrication units, a move which has introduced a number of significant benefits. For instance, not only have the levels of sealing and protection improved, but the preload can now be maintained for a longer period due to reduced wear. Furthermore, reduced running friction has resulted in lower actuator pressure needed for the same operation (from 6 to 4 bar), thus saving energy costs.
The switch to NSK’s lubrication units across six machines means the previous need for 52 re-greasing routines (30 minutes each) per annum, has been reduced to just two. Based on the reduction in maintenance time and labour, yearly savings have been calculated at €4,950.
Building on the success of the K1, which was first launched in 1996, NSK has now developed its K1-L lubrication unit for users of linear guides who want to ensure maintenance-free operations for even longer.
Available to order since December 2019, the K1-L offers a considerable improvement in lubrication capabilities. In fact, thanks to a newly developed resin, the latest unit can supply oil for nearly twice as long. Further benefits of note include the special shape of the K1-L, which reduces dynamic friction force by about 20% when the slider moves along the rail of the linear guide. In addition, a newly developed protective casing helps to maintain structural integrity and further impedes the entry/ejection of dust and other particle contaminants.
1) Internal structure of K1 system, showing the solid lubrication
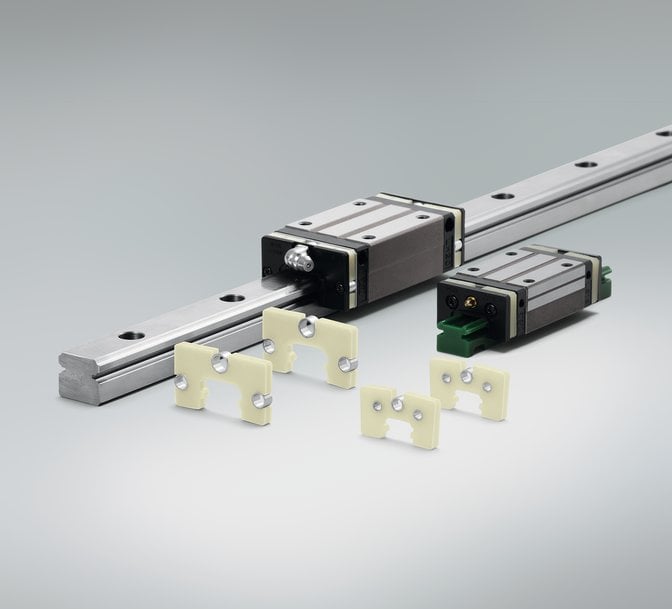
2) Linear guide at the ceramic tile manufacturer fitted with NSK’s solid lubrication K1 system
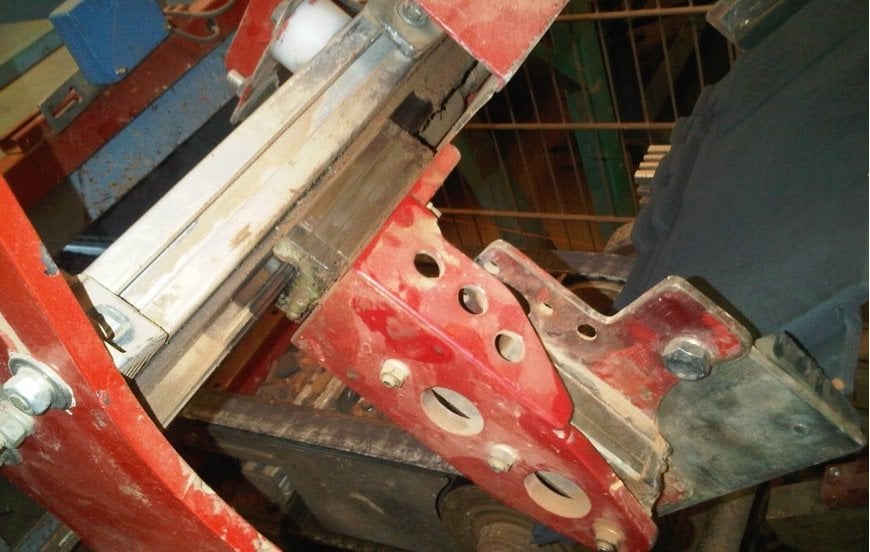
3) The new NSK K1-L offers nearly double the service life of the original K1 lubrication unit
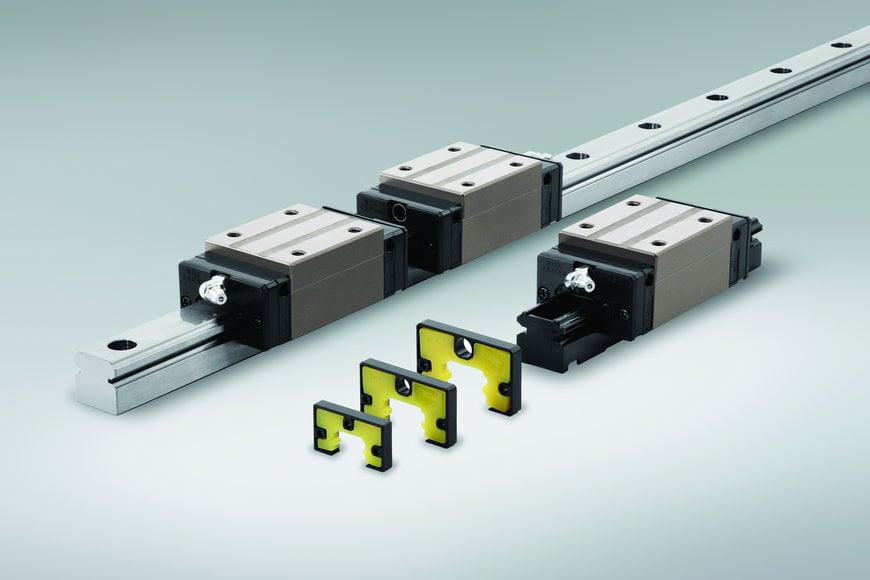