Battery inspection using machine vision – fast, reliable, and variable
Averna automates battery inspection using MVTec HALCON software to identify defects and screen faulty batteries.
www.mvtec.com
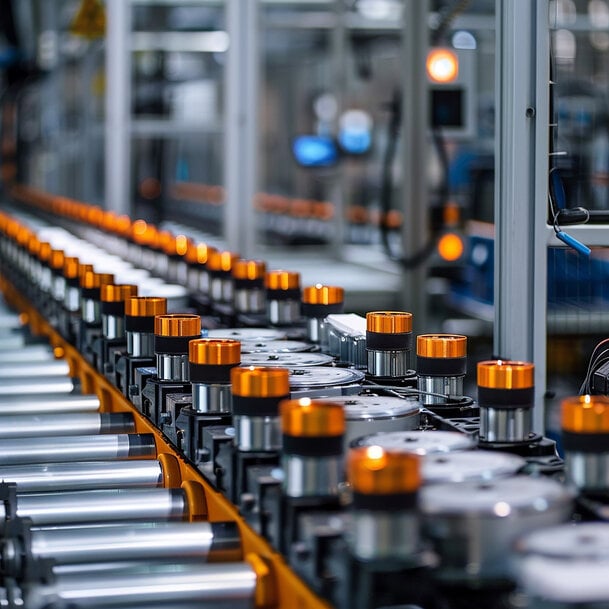
Batteries, whether they are for consumer electronics or any other applications, are subject to extremely high-quality standards. That’s why the manufacturing process is followed by a comprehensive inspection of each battery as part of the forming and aging process. The battery is not only tested for correct functioning, but also inspected for external faults like deformations, indentations, and scratches. Potential defects can vary greatly in terms of both shape and size. Precisely identifying all these anomalies is extremely challenging, but it is the only way to screen out defective batteries reliably before they leave the factory.
A modern testing and quality assurance solution for a prestigious battery manufacturer
Averna has developed a sophisticated solution to this complex problem. Founded in 1999 and headquartered in Montreal, Canada, the company offers specialized concepts and technologies for automated testing procedures. Its range of services includes intelligent measuring systems for the automated performance of functional testing, smart vision solutions for fault inspections, and many other quality-focused applications.
The Averna team designed and implemented an advanced testing and quality assurance solution for a prestigious battery manufacturer. This solution was intended to identify a variety of external product faults and precisely pinpoint their location before the batteries leave the factory. The goal was to improve quality, increase customer satisfaction, and reduce overall costs. “Speed was the top priority for this application because production processes must not be delayed by a time-consuming screening procedure,” says Roel Geraerts, Team Leader, Vision at Averna.
The variety of battery shapes and sizes and the multiplicity of potential damages posed additional challenges. Deformations, scratches, and indentations of many different types and dimensions can appear during the manufacturing process. Until now, the finished batteries were first labeled and then inspected for defects. As a result, production errors were often concealed by the label and therefore overlooked. This allowed lower-quality products to be delivered to customers. The new solution had to be capable of inspecting the batteries very quickly while at the same time identifying every conceivable type of damage reliably. The inspection had to take place before the labeling process and ensure that only fault-free products were labeled and approved for shipping.
360-degree inspection requires powerful technologies
“Our best option for achieving the necessary speed and high level of automation for the inspection workflow was a professional machine vision solution,” says Geraerts. Because a 360-degree approach involves inspecting batteries from all sides, powerful technologies for lighting and handling were needed. In close collaboration with the customer, specialists at Averna developed a sophisticated solution consisting of high-quality cameras and lighting systems mounted on a conveyor belt. The powerful light beams are aimed directly at the battery at optimal angles for making the smallest discrepancies in the battery’s surface visible.
A large number of images recorded at an extremely high speed makes it possible to quickly determine and electronically communicate the position of the test object. Each image includes multiple batteries so that the necessary inspection time can be minimized through simultaneous viewing. Multiple cameras record the battery from every angle, generating nearly 10,000 images per minute. The lighting is designed so that defects appear in the image as shadows resp. at a higher contrast, making scratches, discolorations, and all other types of anomalies easily recognizable. Even indentations that are differently oriented are taken into account. Three Gardasoft controllers regulate the timing of the light precisely and intensify it by up to 300 percent for brief 20-μs intervals.
Precise fault analysis thanks to MVTec HALCON
Averna used MVTec HALCON as its machine vision software for this project. It is seamlessly integrated into Averna’s own software and allows a highly precise analysis of the images. The combinations of light and shadow and the high contrasts thus created in the image are evaluated by blob analysis, which is one of the fundamental methods used in machine vision. It involves the extraction of features from connected pixels that share the same logical state (blobs), such as the color value. The key advantage of this technology is its extremely high processing speed. First the relevant area of the image (region of interest) and then the potential anomalies – in this case, defects – are identified rapidly. The battery is then either rejected as defective or, if no faults are found, forwarded for labeling. A digital, high-speed I/O system communicates the inspection results to the controller, and the products are sorted automatically. The system can also be integrated seamlessly into existing fieldbus technologies like EtherCAT.
In this use case, MVTec HALCON is used to install Averna’s inspection software on a real-time engine, thereby guaranteeing stable recording and evaluation of the image data in order to ensure that defective products are rejected promptly and automatically even at high speeds. With the aid of MVTec HALCON, Averna was able to develop an easy-to-use, customer-specific system that includes fiducial markers. These markers enable a precise measurement of the camera’s focus, brightness, positioning, and angle for various purposes, allowing the customer to calibrate the system easily and independently. The fiducial markers also make it possible to quickly set up identical inspection stations in other locations to guarantee consistent, company-wide results.
Analyzing 10,000 images per minute in real time
“With advanced technologies like blob analysis, MVTec HALCON plays a decisive role in providing our customers with an innovative testing and quality assurance solution. Thanks to the analysis of nearly 10,000 images per minute in real time, we not only achieve a high speed, but also benefit from a highly robust success rate when automatically identifying a wide range of defects of different shapes and sizes. As a result, users can achieve perfect quality in battery manufacturing as well as an extremely high level of customer satisfaction,” concludes Geraerts.
www.mvtec.com