www.ptreview.co.uk
31
'25
Written on Modified on
The Role of Autonomous Inspection Robots in High-Risk Environments
ANYbotics explains key safety challenges in metal production and how inspection robots in the metal industry are reshaping industrial safety standards.
www.anybotics.com
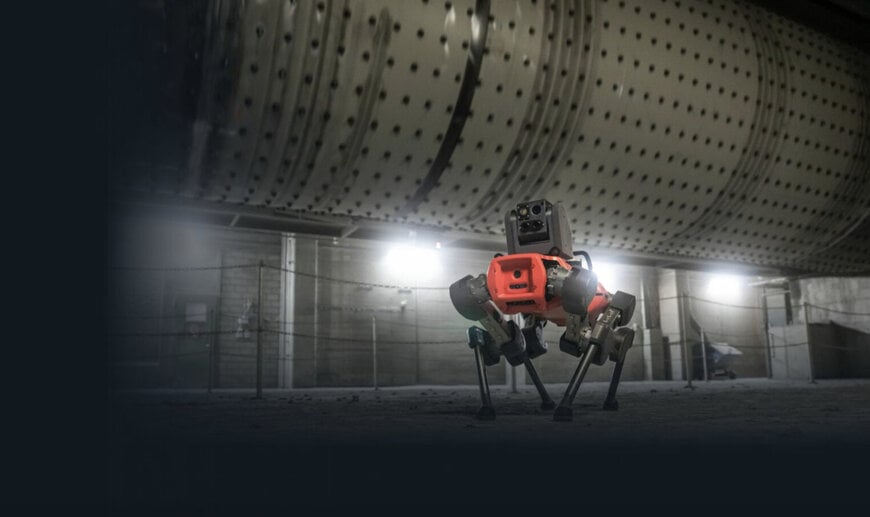
The iron and steel industry is one of the most hazardous industrial sectors in the world. Workers are exposed daily to extreme temperatures, toxic gases, and heavy machinery. Despite advancements in personal protective equipment (PPE) and safety regulations, traditional inspection and maintenance methods still require human exposure to these high-risk environments.
Autonomous inspection robots are redefining workforce safety by minimizing human risk, enabling predictive maintenance for metal plants, and improving operational efficiency. This article explores key safety challenges in metal production and how inspection robots in the metal industry are reshaping industrial safety standards.
Safety Challenges in the Metal Industry
1. Extreme Heat and Hazardous Environments
Steel manufacturing involves blast furnaces and electric arc furnaces with temperatures exceeding 1500°C. Manual inspections in these areas expose personnel to intense heat and potential burns. Toxic gases like carbon monoxide (CO) further increase the risk to human health.
2. Heavy Machinery and Moving Equipment
Steel plants rely on conveyor belts, rollers, and high-powered motors to transport raw materials and finished products. These machines pose a significant risk of crush injuries, particularly during maintenance or manual inspections. Ensuring these machines function correctly while minimizing direct human interaction is critical to workplace safety.
3. Gas Leakages and Chemical Exposure
The use of compressed air, steam, and industrial gases in metal processing requires constant monitoring for leaks. Traditional manual inspections are challenging due to the extreme conditions and can be inconsistent, leading to undetected leaks that pose both safety and environmental risks.
4. Workforce Shortages and Safety Implications
The aging workforce and declining number of skilled operators make staffing industrial facilities increasingly difficult. With fewer personnel available for inspections, critical safety checks can be delayed, increasing the risk of accidents and operational failures.
The Role of Autonomous Inspection Robots in Mitigating Safety Risks
1. Minimizing Human Exposure to Hazardous Environments
Autonomous inspection robots like ANYmal eliminate the need for human workers to enter high-risk zones. These robots can navigate blast furnaces, electric arc furnaces, and cooling systems to perform continuous safety inspections without endangering human lives.
For example, ANYmal can inspect tuyeres in blast furnaces in under 10 minutes, reducing worker exposure to hazardous CO concentrations while ensuring efficient temperature monitoring and preventing equipment failures.
2. Enhancing Leak Detection and Predictive Maintenance
Equipped with visual, thermal, and acoustic sensors, robotic inspection solutions can detect anomalies such as overheating motors, pressure leaks, and failing bearings before they lead to catastrophic failures. Unlike traditional inspections, which are performed manually and at irregular intervals, autonomous robots provide consistent, real-time monitoring.
3. Increasing Inspection Frequency and Accuracy
Industrial robots can conduct repetitive, high-precision inspections multiple times a day, ensuring reliable data collection for trend analysis and predictive maintenance. This reduces the reliance on human intervention and allows operators to make data-driven decisions to optimize plant performance and safety.
4. Addressing Workforce Shortages and Reducing Human Fatigue
By automating routine inspections, autonomous robots free up human workers for more critical decision-making tasks. This not only improves operational efficiency but also helps alleviate the growing labor shortage in the industrial sector.
The Business Case for Autonomous Inspection Robots in Metal Industries
1. Reducing Workplace Incidents and Compliance Risks
Minimizing human exposure to high-risk environments significantly reduces workplace accidents, injuries, and compliance violations. Autonomous inspections help companies meet stringent occupational safety regulations while lowering insurance and compensation costs.
2. Preventing Unplanned Downtime and Equipment Failures
A single furnace failure or gas leak in a steel plant can lead to production halts and financial losses in the millions. ANYmal’s ability to autonomously monitor critical equipment ensures early detection of potential issues, preventing costly unplanned shutdowns.
3. Enhancing ROI Through Improved Data-Driven Decisions
Robotic inspection technology integrates seamlessly with asset management systems, providing real-time insights and alerts that enable operators to take proactive maintenance actions. The high-quality data collected by robots supports predictive maintenance strategies, reducing costs and optimizing plant efficiency.
Conclusion
Workforce safety remains a major challenge in the iron and steel industry, but autonomous inspection robots provide a scalable and reliable solution. By minimizing human exposure to hazardous environments, enhancing predictive maintenance capabilities, and addressing workforce shortages, these robots are reshaping industrial safety standards.
As metal manufacturers continue to prioritize safety and operational efficiency, adopting robotic inspection solutions will be critical to maintaining a safe, productive, and future-ready industry.
www.anybotics.com