How to optimise smooth machine motion with electronic cam profiling
Gerard Bush, engineer at motion specialist INMOCO, explores how electronic cam profiling reduces jerk and enhances machine performance, enabling smoother and more precise motion in CNC, textile production, 3D printing, and robotic applications.
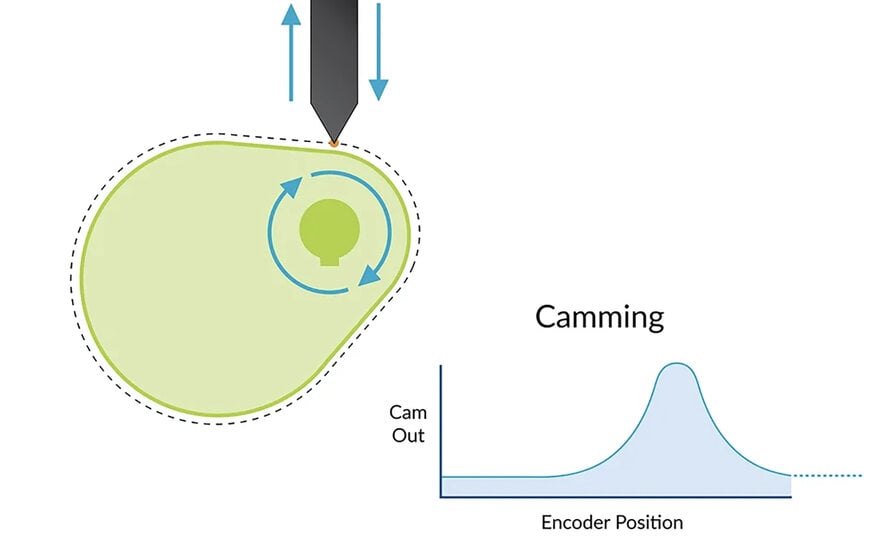
Precise and smooth motion control is essential for a wide variety of machine applications, ranging from CNC to textile production, and a key tool to achieving this is the electronic cam. Based on the principle of its original mechanical counterpart, the smooth motion profiles that an electronic cam provides can optimise machine performance.
In a machine application that relies on precise motor control, controlling jerk is crucial. Jerk is the rate of change of acceleration over time, so minimising this value is essential to achieving smooth motion. This applies to the performance of applications such as CNC machining and machine tools, fabrication equipment, textiles, plastic forming and 3D printers. Not only is controlling jerk essential to the machine’s output, but it can also affect mechanical stress. Sudden changes in acceleration and force can, over time, lead to increased maintenance, and ultimately, this additional strain can contribute to reduced operational lifetime.
The main way of minimising jerk is by exercising control over the application’s motion profile, the pre-defined parameters relating to position, velocity, acceleration - and the rate of change of acceleration. While a linear or trapezoidal motion profile typically exhibits sudden starts and stops in acceleration that are characteristic of elevated levels of jerk, a motion profile such as an S-curve produces a smoother gradient. This type of profile gradually ramps up to its maximum speed, remaining constant for the desired period, before smoothly ramping back down.
Smooth motion profile
To achieve an S-curve, or an alternative, smooth motion profile that doesn’t follow a standard envelope, cam profiling is a useful tool. Originally used to replicate mechanical rotating cams, electronic cam profiling can provide an array of profile generation and position compensation functions. This control technique uses a pre-stored look-up table of desired positions, driven by an incoming command encoder data stream. The advantage of the look-up table is prior calculation for quick retrieval, where the alternative of real-time computation would be too slow for requirements, or too processor intensive.
Often, electronic cams are encoded in a rotating frame. The last lookup value is adjacent to the first, and the encoded values are usually interpreted as absolute command positions, though they can also be interpreted as relative moves. The encoded table provides linear interpolation between points, smoothing out the output command profile but also reducing the required number of stored points. For a profile that’s smoother still, spline interpolation can also be used, increasing the linking points to optimise the curve of the motion path.
A single encoder data stream can drive multiple cam controllers, allowing multiple processes to operate simultaneously while remaining in full synchronisation. This way, it’s possible to define a motion path in three-dimensional space, with a main axis followed by cam profiles relative to it – or in coordination with one another. Consequently, the selection of alternate input data stream sources can enable multi-axis coordination for applications such as selective compliance articulated robot arm (SCARA) robots. As an electronic cam controller lookup table can store torque or position feedforward data, this technique can also be used to implement features such as lead screw mapping where torque feedforward values can compensate for known external forces from the motor or load.
For the control flow of an electronic cam system, the typical architecture involves an encoder input combined with the rate scalar that controls the rate of change in cam position. A phase adjust fine tunes this value ahead of the user-defined cam profile stage, responsible for generating a contour output based on a start and end index position. Finally, a contour offset modulates the value, compensating for factors such as wear or load, before a commanded position is generated.
Motion engineering support
Motion control equipment vendors provide various cam profile systems to assist with its implementation. Performance Motion Devices (PMD) offer the User Defined Profile Mode system (UDPM), scaled to support the range of electronic cam moves, from simple profiles through to advanced interpolation and functions. UDPM is supported in special versions of PMD’s Magellan-based IC, module, and board products.
To determine motion requirements, and to design the application concept including electronic cam profiling, specialised assistance can be useful. Not only can motion engineering support save time in development, but it can also help optimise the performance of the application.
At Intelligent Motion Control (INMOCO), engineers can receive support in motion profile design as well as equipment specification. Electronic cam profiling is just one of the tools recommended to ensure precise and reliable motion control.
www.inmoco.com