www.ptreview.co.uk
04
'25
Written on Modified on
SEGULA Technologies develops AI-based industrial software that reduces process time and complexity by 33%
Three main blocks address code generation, intelligent connectivity, and AAS connectivity.
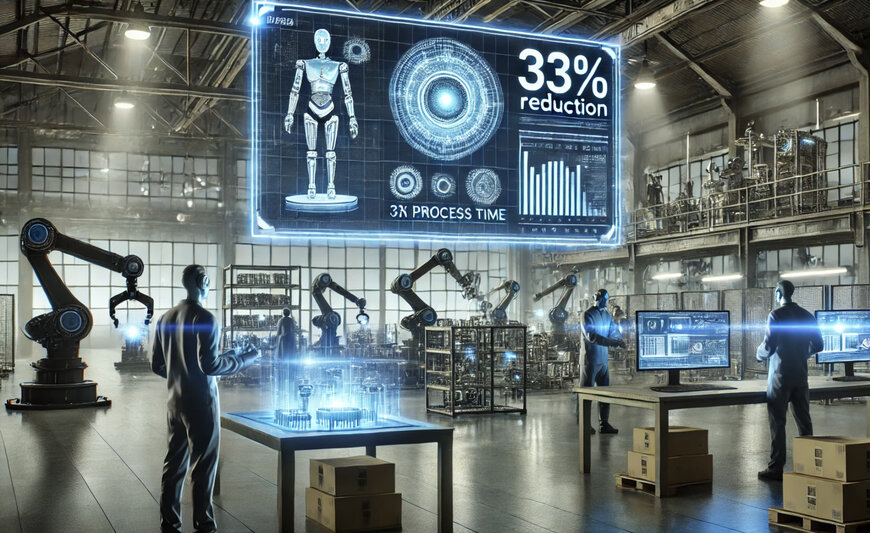
The industrial sector is experiencing a new revolution as a result of the integration of Artificial Intelligence and the use of data, which is allowing an improvement in efficiency and an increase in productivity and competitiveness. This has led to 67% of industrial companies already betting on this technology for production optimization, according to data from the Ascendant report by Minsait (Indra).
In this context, SEGULA Technologies has launched SOFIA, a project focused on the development of industrial software in the field of data capture and visualization applications in “machine tool”, and it is expected to be completed by the end of 2026. The key to SOFIA lies in the introduction of the concept of ‘software factory’, where AI plays an essential role in automating and reducing development tasks.
The project proposes an ecosystem that allows dynamic consultation of data and obtaining customized graphs or panels with less effort. In this way, the user can interact directly with a friendly interface. SOFIA also includes the application of AAS (Asset Administration Shell) and UNS (Unified Name Spaces) for system standardization.
“Since 2018, at SEGULA Technologies we have been making a strong commitment to R&D projects focused on the use of AI and, in recent years, these have expanded not only to cover needs such as process optimization, but we are also focusing on supporting our clients to be faster and more effective, reducing the prototyping time of SCADA solutions or reducing the complexity in processes such as anomaly detection in machine tool. SOFIA is an R&D project that starts from an idea with a high technical risk and seeks to validate technologies and generate prototypes from which to develop new tools and services towards our clients. That is, SOFIA proposes an ecosystem of tools that allows us to reduce by 33% the time and complexity that we would normally need,” explains Jorge Martínez Santiago, R&D Manager of the IA & Industry 4.0 of SEGULA in the Vitoria-Gasteiz office.
SOFIA is being developed in Vitoria Gasteiz (Basque Country), within the framework of the CDTI Transmissions call, and thanks to the collaboration of 8 companies (PROXYA, TSK, Grupo. AZVI, SEGULA Technologies, COTESA, INIXA, UNDANET) and two universities (U. de SALAMANCA and U. de MÁLAGA).
This initiative is structured in three main blocks that address different applications: code generation with AI, intelligent connectivity in the naval sector, and connectivity and data structure with AAS.
Code generation with AI
The first block focuses on using machine learning models to generate automated code capable of executing specific tasks. “We use LLMs (Large Language Models) to generate the necessary code, for example, to create an anomaly detector or a classifier. The idea is to replicate the behavior of a person in software development,” explains Jorge Martinez. This technology has the potential to transform the way solutions are designed and programmed, speeding up processes and minimizing human intervention in repetitive tasks.
Intelligent connectivity in the naval sector
Through this development, SOFIA seeks standardization in data capture in machinery, more specifically, in the electro generator system of ships, systems that are distributed in fleets and need to capture data, as well as being able to use these data for maintenance tracking, performance, etc.
The project proposes a common infrastructure that allows data capture in distributed EDGE devices and their subsequent grouping and management at a central point.
“In the naval sector, it is a land-based system that benefits from the grouping of data to provide solutions to common problems on ships,” explains Jorge Martínez.
Connectivity and data structure with AAS
The implementation of machinery in production lines poses a challenge: the lack of standardization of many systems. Therefore, the use of standards such as AAS allows a robot to be changed in less time on a production line, and increase its capabilities, allowing the user to access the data generated through a chat where they can consult the data of a line with natural language.
“For example, if one wants to know the temperature of all the motors on line 5 or the maximum temperatures this month, that is key because it allows us to propose visualization panels of the data and facilitate the relationship of the data,” explains Jorge Martínez.
www.segulatechnologies.com