www.ptreview.co.uk
03
'25
Written on Modified on
Flexibility and Efficiency in Small Batch Production through Automation
David Dorfmüller Söhne GmbH & Co. KG enhances flexibility and efficiency in small-batch production with Yaskawa automation.
www.yaskawa.eu.com
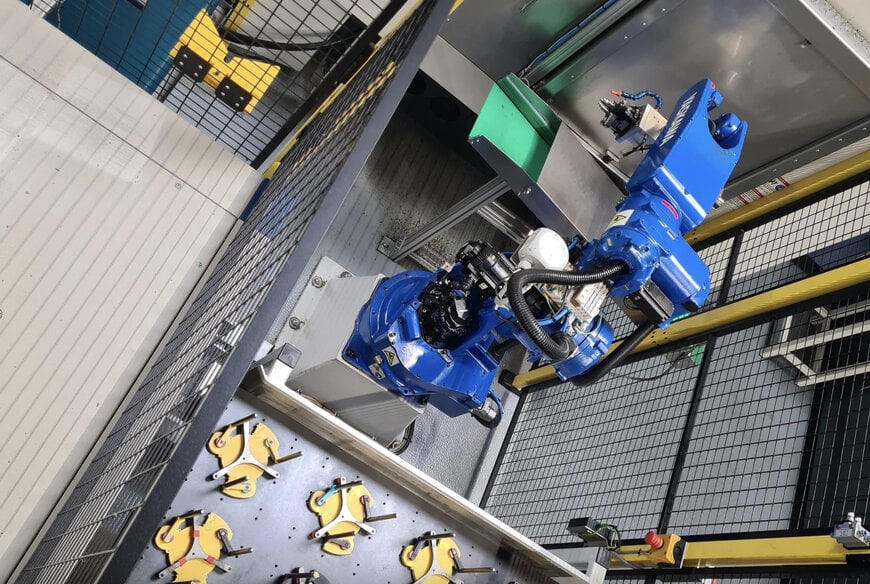
The competitive, machining-based production of special parts in small to medium series is a challenge for many SMEs. The goal is to set up and utilize a modern machine park as flexible as possible. A key aspect is process automation, which significantly contributes to quality assurance and machine utilization, and can also address the shortage of skilled workers. This flexibility and efficiency in production directly benefit customers by ensuring high-quality products and timely delivery. A great example of this is David Dorfmüller Söhne GmbH & Co. KG in Remscheid, Germany.
At Dorfmüller, fasteners are considered a core competency, producing nuts, bolts, washers, and custom parts in large dimensions for all relevant industries, including shipbuilding, wind power, railways, gear manufacturing, and the energy sector. Specifically, this means nuts up to size M200, corresponding washers, special screws up to 2 meters long, and custom parts up to 800mm in diameter made from various steels and in different shapes. The company's history dates back to 1884, and today it employs 60 people.
The fifth generation, Lucas Dorfmüller, is now in management. "Knowing today what will be needed tomorrow" is the motto on their website, with a note clarifying that while they don't possess clairvoyant abilities, they aim to be as well-prepared as possible. This proactive approach ensures that customer needs are anticipated and met efficiently. In addition to a large raw material warehouse and a modern machine park, this also includes the automation of machining processes. Specifically, this means the automatic loading and unloading of machines with automation solutions that are both flexible and offer a high degree of autonomy. Such automation ensures consistent quality and reliability, which are crucial for customer satisfaction. Dorfmüller decided to venture into robotic automation in 2017.
During an online search for potential system providers, they came across EGS Automation, a brand of AMETEK from Donaueschingen, Germany. EGS has been developing and implementing automation solutions for machine tools since 1996 and has been offering standardized robot solutions under the product name SUMO since 1999.
Initially, Dorfmüller wanted to automate an existing lathe or milling machine. EGS developed concepts and made initial offers. However, it was then decided to automate a machining center that was due for new acquisition. The workpieces to be machined should be loaded and unloaded.
This decision was driven by the need to enhance production efficiency and meet customer demands more effectively. Considering all requirements, the choice fell on the SUMO Flexiplex from EGS. This solution can be retooled for different part sizes in just a few minutes without tools. The workpieces can have different geometries and are stored on a multi-lane conveyor system and fed to arobot. The robot loads and unloads the machine. No workpiece carriers are required. The automation was installed on a Brother Speedio machining center. The machine offers a side loading door, so the front door remains fully accessible, e.g., for setup tasks on the machine or for manual loading of small and special series. "Regarding interface coordination, we initially feared that difficulties might arise and responsibilities might be shifted between the machine supplier and the automator. However, this concern was completely unfounded. EGS clarified everything directly with the machine supplier, and it worked plug and play," recalls Lucas Dorfmüller about the commissioning. This seamless integration ensures minimal downtime and uninterrupted service for customers.
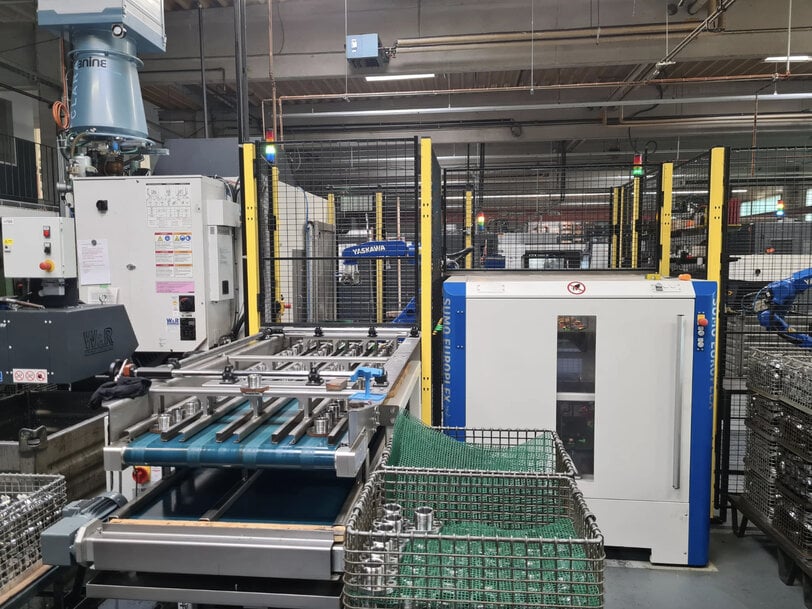
The first automation was immediately convincing, and the machine's utilization could be maximized. The effective runtime was almost tripled, both in operation with personnel and through an additional ghost shift without personnel. At the same time, labor costs per machine hour could be significantly reduced, and new orders were ultimately won through the possibility of automated production. In total, the investment was amortized in significantly less than 24 months.
These improvements translate to cost savings and competitive pricing for customers. Every machine at Dorfmüller is integrated into a reporting system. When the workpiece stock is automatically processed, a message is sent to the company's central control unit, which then initiates the shutdown of energy-intensive systems, such as compressed air generation. This is just one of many measures for energy efficiency and sustainability in the company. Such measures ensure that customers receive products from a company committed to sustainability and environmental responsibility. Due to the positive experiences, it was clear from the beginning that the next machine for similar workpiece sizes would be equipped with automation. This time, however, a larger workpiece spectrum and heavier parts were expected. Therefore, a solution was implemented that was supplemented by a SUMO Europlex in addition to the SUMO Flexiplex. The smaller and lighter components are fed via the Flexiplex's conveyor system, while larger and heavier parts are loaded on pallets in adjustable holders via the Europlex palletizing system. The pallets can be loaded and unloaded in the SUMO Europlex using a forklift during automatic operation.
This results in even greater autonomy and significantly increased flexibility of the overall system. This flexibility ensures that customer orders, regardless of size or complexity, can be handled efficiently. Both systems are located next to each other and are fully integrated into the material logistics. They can be operated with very little personnel: numerous components from recurring orders are now set up and can be retooled in less than 10 minutes. When the system needs to be set up for new variants of previously unproduced parts, Dorfmüller is now able to do this completely independently. Both the program adjustment and the production of workpiece-specific gripper fingers are carried out in-house. "This naturally increases flexibility and keeps costs low, but it would also be economical for us to rely on EGS's services," says Lucas Dorfmüller. "Overall, we initially imagined the topic of retooling to be much more complicated than it actually turned out to be."
This capability ensures quick turnaround times and cost-effective solutions for customers. The handling of the robot technology by the operating personnel was somewhat underestimated at the beginning. For the specialists in the company, it was a very short learning phase. After training by EGS and subsequent regular handling of program adjustments and changes, know-how was quickly built up. Operating personnel, who were also trained but rarely use the robot's operating device, had greater reservations.
Consequently, Dorfmüller was delighted to hear about the newly developed SmartPad from EGS. The third system, again a SUMO Flexiplex, will be one of the first to be delivered with this new development. With the SmartPad, no programming knowledge is required, and no robot operating device is needed for operation or setting up new variants. It also offers clear status messages and manages production orders. This time, an existing lathe, which is currently still manually loaded and unloaded, will be automated.
This user-friendly technology ensures that production remains efficient and responsive to customer needs. The entry into robotic automation and further development at Dorfmüller is a typical example of how a medium-sized manufacturing company with constantly changing part variants can achieve successful and economical use. This requires an automation specialist with a lot of experience who stands by the company's needs and supports knowledge and skill development. "We found that with EGS Automation. They made it as easy as possible for us to get started with automation. We now handle everything independently after installing a new system. Nevertheless, it's good to know that we can always rely on support if needed," concludes Lucas Dorfmüller. This partnership ensures that customers benefit from continuous innovation and reliable support.
www.yaskawa.eu.com