www.ptreview.co.uk
03
'25
Written on Modified on
Explosionproof motors for hazardous environments
Lenzing Filtration needed explosionproof motor and drive systems for hazardous MDI production. WEG Gear Systems provided a custom solution to meet safety standards.
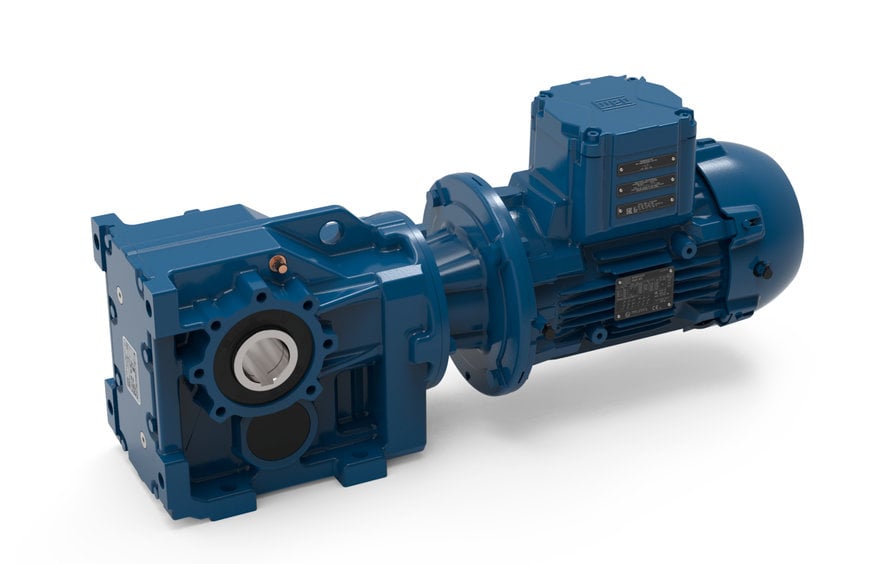
Over 270 hazardous chemical incidents — including fires, explosions and harmful chemical releases — occurred in 2023 alone, according to data published by the Coalition to Prevent Chemical Disasters. In chemical production, the risk of explosions is always present and creates a pressing need for stringent safety measures. Over four decades, the Austrian manufacturer Lenzing Filtration has built a solid reputation for developing high-quality filter devices. The company specialises particularly in automated backflush filtration systems, which are deployed across diverse industrial domains.
However, the company faced a steep challenge when a Chinese chemical company sought its expertise for the production of polymer MDI, which is hazardous due to its toxicity, potential for explosions, and chemical reactivity. MDI poses health risks to individuals through inhalation or skin contact, can create explosive atmospheres, and its reactivity with other substances can lead to hazardous by-products.
Effective safety measures and proper handling procedures are crucial to mitigate these risks and protect both human health and the environment. In addition, all manufacturing systems involved in the process — ranging from drives to motors —should meet the stringent provisions of the ATEX Directive 2014/34/EU, the certification for equipment used in potentially explosive atmospheres.
The Chinese polymer MDI producer approached Lenzing Filtration, to draw on the latter company’s wealth of experience and technical acumen. Lenzing Filtration put forward its own OptiFil® backwash filters as the best solution.
ATEX-certified
Lenzing Filtration’s backwash filters are engineered to filter all kinds of low-viscosity media found in production processes, with seamless precision. However, propelling these automated systems into action would require robust and ATEX-certified motor and drive systems that were capable of guaranteeing reliability, safety and endurance — particularly in harsh production environments.
Lenzing Filtration turned to WEG Gear Systems — then still known as Watt Drive — for a holistic solution that was engineered to overcome these challenges. WEG Gear Systems was able to draw on its diverse array of drive solutions, including explosionproof motors and drives conforming to the exacting ATEX specifications.
Lenzing Filtration opted for W22Xde ATEX motors, capable of withstanding pressures up to 14.1 bar and temperatures of 80 degrees Celsius. Special Viton shaft seal rings and a corrosiveness-resistant epoxy resin finish would help ensure the motors’ durability.
For the OptiFil-250-0720 filters, a WG20 helical bevel gear motor with a torque of 308 Newton meters (Nm) and 1.10 kilowatts (kW) output was employed. Larger OptiFil-350-1080 filters utilised a more powerful solution with 696 Nm torque and 2.20 kW output. Both setups featured thermal monitoring and complied with ATEX requirements.
In all, WEG Gear Systems supplied 21 drive systems for use in China, meeting Zone 1 and Zone 21 ATEX requirements with a 660 volts (V) voltage supply.
Lenzing Filtration praised the robustness and cost-effectiveness of WEG's solutions. Johannes Kneissl, technical manager filtration & separation at Lenzing Filtration, commented that WEG Gear Systems, “was able to design a very robust WEG drive solution for us from a single source, which was able to meet all challenges and at the same time contributed to a significant reduction in overall costs.”
The solution also reduced personnel needs and ensured operational efficiency in the Chinese chemical company’s hazardous environments.
Safety standards
The collaboration between Lenzing Filtration and WEG Gear Systems, has resulted in a highly successful project that addresses the demanding challenges posed by supplying systems for hazardous MDI production in China.
By leveraging WEG Gear Systems’ expertise and WEG's robust motor and drive solutions, Lenzing Filtration effectively met the stringent safety standards required by the industry, which remain as important as ever, as illustrated by the Coalition to Prevent Chemical Disasters report.
“Not only were the performance and results right, but the cooperation and reliability also proved to be excellent,” added Kneissl. “Lenzing Filtration is therefore very satisfied with WEG as a supplier in all respects.”
www.weg.com