INKMAKER BOOSTS PRECISION AND PRODUCTIVITY AT QINGDAO HAIDE PACKAGING
The deployment marks another significant step in revolutionising the flexible packaging industry with intelligent automation solutions.
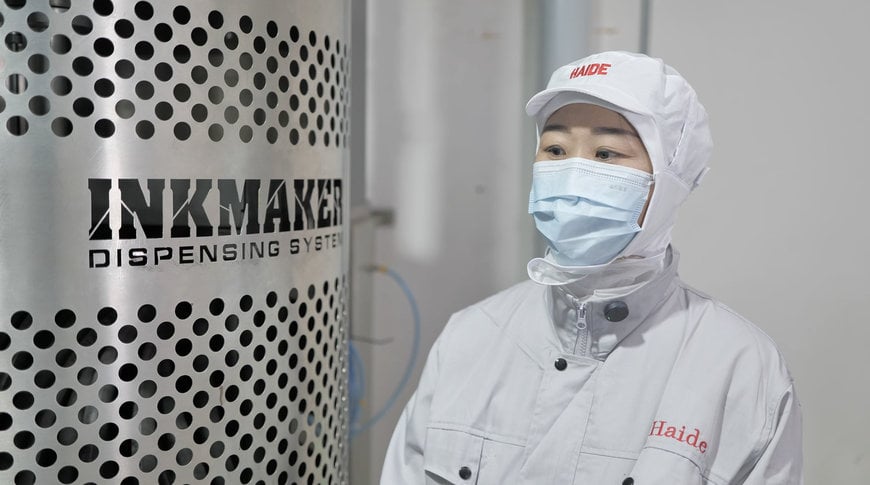
Inkmaker Shanghai, a member of IM GROUP, has announces the transformative impact of its advanced automatic ink-dispensing system at Qingdao Haide Packaging in Qingdao, China.
Qingdao Haide Packaging, a leading manufacturer in flexible packaging, is known for its commitment to innovation and high-quality production standards. Facing the challenges of conventional colour-mixing methods—such as extended ink preparation times, inconsistencies in colour matching, and substantial ink waste—the company sought a solution to enhance productivity and quality control.
Since implementing Inkmaker’s automatic dispensing system, Qingdao Haide Packaging has achieved remarkable improvements:
- Efficiency Gains: Production efficiency increased by nearly 30%, with ink-mixing times per order reduced by approximately 20 minutes.
- Enhanced Precision: Advanced algorithms ensure that colour consistency reaches ΔE ≤ 1 within a single correction cycle, significantly boosting both colour-matching speed and accuracy.
- Cost Reduction: The Inkmaker Automated Ink Management System optimises ink usage, dramatically reducing residual ink waste. Recent data shows that over 50% of previously accumulated residual ink inventory has been utilised effectively.
- Mismatching Reduction: The INKMAKER glue-dispensing system significantly reduces mismatching and manual labour demands.
- VOC Emissions Reduction: Sealed pipeline transportation lowers VOC emissions, improving safety and minimising environmental impact during the glue-dispensing process.
Mr. Liu, Production Manager at Qingdao Haide Packaging, praised the Inkmaker system, stating: "The integration of this technology has significantly enhanced our operational workflow. Our production efficiency has increased by nearly 30%, the average ink-mixing time per ink is approximately 20 minutes faster, and human errors have greatly reduced. Customer satisfaction with our products has also significantly improved because of the ability to store and retrieve colour data within the system. This means we can read the data directly for future reproductions, ensuring rapid and consistent ink blending, which improves both the production process and turnaround times."
The intelligent features of the Inkmaker dispensing system also extend to sustainable ink management. Automated monitoring allows maximum reuse of residual ink, reducing waste and supporting more sustainable production practices.
Ms. Zhang, Workshop Foreman at Qingdao Haide Packaging, noted: "Tasks that once took hours are now completed in minutes. The streamlined process and improved accuracy have redefined our approach to colour management."
Additionally, the Inkmaker Automatic Glue Dispensing System has completely transformed Qingdao Haide Packaging’s traditional manual gluing production methods. It ensures consistent glue quality, significantly improves safety, and enhances environmental protection by reducing VOC emissions.
Inkmaker’s Automated Ink Management System continues to lead the industry by providing innovative dispensing solutions that integrate automation, digitalisation, and smart technology. As global demand for sustainable, efficient production grows, Inkmaker remains committed to delivering tailored solutions that maximise efficiency and minimise environmental impact.
www.inkmaker.com