www.ptreview.co.uk
28
'25
Written on Modified on
Exploring Safety and Innovation: Outokumpu’s Robotics Journey
ANYbotics' robots have helped mitigate up to 80% of exposure to hazardous incidents, enabling employees to focus on higher-value tasks.
www.anybotics.com
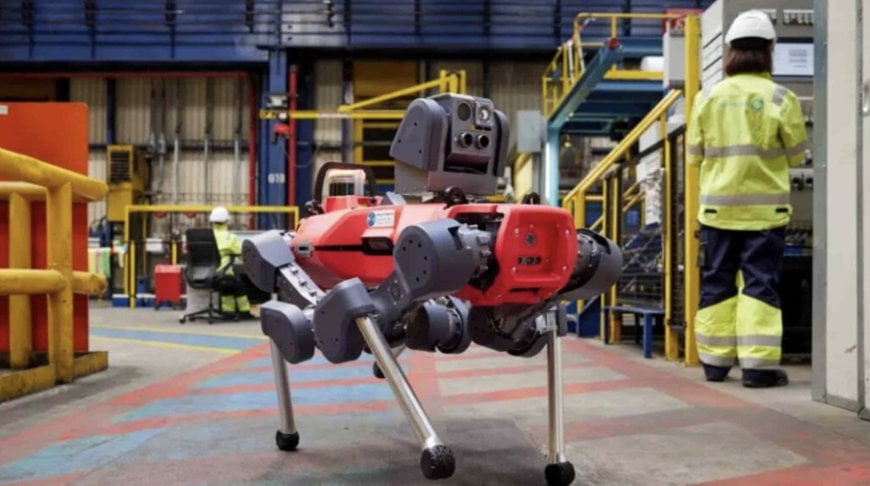
ROSIE, the Krefeld running robot, operates for two hours before requiring a two-hour charging period. (Courtesy: Outokumpu)
Outokumpu, a global leader in stainless steel manufacturing, is celebrated for its commitment to sustainability and its mission to create “a world that lasts forever.” At the core of its operations lies an unwavering dedication to safety, embodied in the company’s ambitious “mission zero incidents” initiative. Recently, Thorsten Piniek, Vice President of Health & Safety at Outokumpu, engaged in a thought-provoking conversation with Tom Tomaszewski, Senior Director of Sales at ANYbotics, to explore the company’s groundbreaking approach to integrating robotics into its safety practices.
Through deploying ANYmal robotic inspection solutions at key sites in Finland, Germany, and Sweden, Outokumpu has significantly enhanced safety-critical operations while reducing risks and protecting its workforce. Robots have helped mitigate up to 80% of exposure to hazardous incidents, enabling employees to focus on higher-value tasks. This pioneering approach positions Outokumpu at the forefront of innovation, blending advanced technology with human ingenuity to achieve remarkable results.
In this engaging interview, Thorsten shares actionable insights into Outokumpu’s safety initiatives, the transformative role of robotics in hazardous environments, and the successes realized through collaboration and technology. Packed with lessons for organizations eager to embrace innovation, this discussion highlights how automation can redefine workplace safety and create a safer, more efficient future for industrial processes.
Why is safety so crucial at Outokumpu, and how do you approach it?
Thorsten: Safety is fundamental because every individual matters. Our commitment is to ensure that anyone visiting or working at our sites leaves in the same condition they arrived. We prioritize safety over production volume, emphasizing the importance of not taking shortcuts. No matter how minor, lessons learned from incidents are integral to improving our safety protocols.
Our safety principles start with each individual: “Safety starts with me.” This approach is embedded in our operations, from risk assessments to initiatives like “Act Safely with Pride and Care,” which focus on human behavior and leadership by understanding.
How has Outokumpu progressed toward its safety vision?
Thorsten: Since 2016, we’ve reduced our incident frequency rate from 8.7 to 1.5 recordable incidents per million working hours, a significant achievement driven by structured initiatives. Our approach involves setting realistic interim targets to maintain momentum and foster a sense of success among our teams.
We’ve also implemented targeted programs addressing critical risks, such as machinery guarding, human behavior, and technology adoption, including deploying robotics in hazardous areas.
Can you explain the role of robotics in your safety strategy?
Thorsten: Robotics plays a critical role in isolating humans from hazardous environments. We identified areas where human interaction with machinery posed significant risks, such as the acid regeneration plant, pickling lines, and crushing areas. By deploying robots, we reduced the need for humans to enter these areas, thus minimizing exposure to dangers like sharp materials, hazardous chemicals, and extreme heat.
The robots are equipped with advanced sensors, cameras, and tools like thermographic cameras and ultrasonic microphones to conduct inspections, detect anomalies, and monitor trends. This data is relayed to control rooms for analysis and action.
How has the workforce responded to robotics?
Thorsten: Initially, there were concerns about job displacement, but we clarified that robots are not replacing people—they enhance safety and efficiency. To engage employees, we encouraged them to name the robots at each site, creating a sense of ownership. For example, our robot in Krefeld is called “Rosie,” while in Tornio, it’s “Jokeri.” This personalization fostered acceptance and enthusiasm for the technology.
What criteria guided your selection of robotics solutions?
Thorsten: The key was finding robots suitable for industrial environments. Critical factors include durability, compatibility with harsh conditions, and the ability to integrate specialized tools like thermographic cameras. Flexibility was also necessary, as the robots needed to be adaptable to various tasks and environments across our sites.
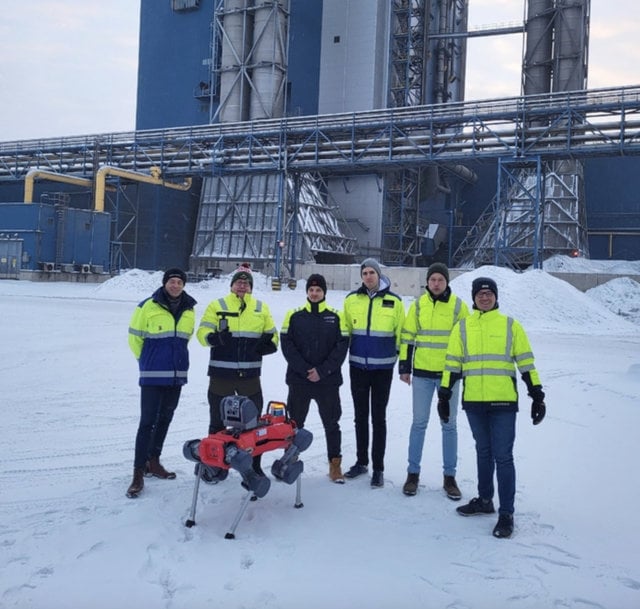
JOKKERI and the operators at Outokumpu’s Tornio Ferrochrome facility. (Courtesy: Outokumpu)
What tasks have the robots taken over, and what are the benefits?
Thorsten: Robots primarily handle inspections, such as monitoring gauges, detecting leaks, and identifying hotspots or deviations in machinery performance. This allows human operators to focus on more complex tasks while reducing their exposure to hazardous conditions. The time saved is significant—for instance, preparing for a manual inspection in the crushing area can take up to 30 minutes, time that robots can use to gather valuable data.
How are you measuring the success of robotics in your safety initiatives?
Thorsten: Our primary metric is reducing employee exposure to hazardous environments. We track the number of missions conducted by robots and the duration of these missions. Additionally, we’re evaluating the return on investment by assessing how robot-detected deviations have prevented equipment breakdowns and production interruptions.
What advice would you give to organizations considering robotics?
Thorsten: Start with a thorough risk assessment to identify areas where robotics can impact the most. Be open to diverse technologies and solutions, such as drones for height inspections. Engage your workforce transparently from the beginning, communicating the goals and benefits of automation. Collaborate closely with technology providers, challenging them to deliver tailored solutions. Lastly, celebrate small successes and involve the entire organization in the journey.
What are the long-term benefits of automation and robotics in the industry?
Thorsten:: Automation reduces manual, high-risk tasks, enabling us to leverage the expertise of our workforce better. It also facilitates the generation of valuable data, enhancing predictive maintenance and overall operational efficiency. As technology advances, the potential for safer, smarter, and more sustainable operations continues to grow.
Any closing thoughts?
Thorsten: Robotics and automation are integral to our journey toward zero incidents and a safer workplace. Collaboration, innovation, and a shared commitment to safety will ensure our success. Thank you for the opportunity to share our story.
The partnership between Outokumpu and ANYbotics highlights the transformative potential of combining advanced technology with a steadfast commitment to safety. By deploying ANYmal robotic inspection solutions, Outokumpu has not only enhanced its ability to mitigate risks but also empowered its workforce to focus on higher-value tasks. Thorsten Piniek articulated that the journey toward zero incidents is a continuous process driven by collaboration, innovation, and a shared vision for a safer and more efficient future. By leveraging robotics and automation, Outokumpu is setting new benchmarks for safety and operational excellence in the stainless steel industry, embodying its mission to create “a world that lasts forever.” This partnership is an inspiring example for industries worldwide as they navigate the intersection of technology and sustainability.
Outokumpu, a global leader in stainless steel manufacturing, is celebrated for its commitment to sustainability and its mission to create “a world that lasts forever.” At the core of its operations lies an unwavering dedication to safety, embodied in the company’s ambitious “mission zero incidents” initiative. Recently, Thorsten Piniek, Vice President of Health & Safety at Outokumpu, engaged in a thought-provoking conversation with Tom Tomaszewski, Senior Director of Sales at ANYbotics, to explore the company’s groundbreaking approach to integrating robotics into its safety practices.
Through deploying ANYmal robotic inspection solutions at key sites in Finland, Germany, and Sweden, Outokumpu has significantly enhanced safety-critical operations while reducing risks and protecting its workforce. Robots have helped mitigate up to 80% of exposure to hazardous incidents, enabling employees to focus on higher-value tasks. This pioneering approach positions Outokumpu at the forefront of innovation, blending advanced technology with human ingenuity to achieve remarkable results.
In this engaging interview, Thorsten shares actionable insights into Outokumpu’s safety initiatives, the transformative role of robotics in hazardous environments, and the successes realized through collaboration and technology. Packed with lessons for organizations eager to embrace innovation, this discussion highlights how automation can redefine workplace safety and create a safer, more efficient future for industrial processes.
Why is safety so crucial at Outokumpu, and how do you approach it?
Thorsten: Safety is fundamental because every individual matters. Our commitment is to ensure that anyone visiting or working at our sites leaves in the same condition they arrived. We prioritize safety over production volume, emphasizing the importance of not taking shortcuts. No matter how minor, lessons learned from incidents are integral to improving our safety protocols.
Our safety principles start with each individual: “Safety starts with me.” This approach is embedded in our operations, from risk assessments to initiatives like “Act Safely with Pride and Care,” which focus on human behavior and leadership by understanding.
How has Outokumpu progressed toward its safety vision?
Thorsten: Since 2016, we’ve reduced our incident frequency rate from 8.7 to 1.5 recordable incidents per million working hours, a significant achievement driven by structured initiatives. Our approach involves setting realistic interim targets to maintain momentum and foster a sense of success among our teams.
We’ve also implemented targeted programs addressing critical risks, such as machinery guarding, human behavior, and technology adoption, including deploying robotics in hazardous areas.
Can you explain the role of robotics in your safety strategy?
Thorsten: Robotics plays a critical role in isolating humans from hazardous environments. We identified areas where human interaction with machinery posed significant risks, such as the acid regeneration plant, pickling lines, and crushing areas. By deploying robots, we reduced the need for humans to enter these areas, thus minimizing exposure to dangers like sharp materials, hazardous chemicals, and extreme heat.
The robots are equipped with advanced sensors, cameras, and tools like thermographic cameras and ultrasonic microphones to conduct inspections, detect anomalies, and monitor trends. This data is relayed to control rooms for analysis and action.
How has the workforce responded to robotics?
Thorsten: Initially, there were concerns about job displacement, but we clarified that robots are not replacing people—they enhance safety and efficiency. To engage employees, we encouraged them to name the robots at each site, creating a sense of ownership. For example, our robot in Krefeld is called “Rosie,” while in Tornio, it’s “Jokeri.” This personalization fostered acceptance and enthusiasm for the technology.
What criteria guided your selection of robotics solutions?
Thorsten: The key was finding robots suitable for industrial environments. Critical factors include durability, compatibility with harsh conditions, and the ability to integrate specialized tools like thermographic cameras. Flexibility was also necessary, as the robots needed to be adaptable to various tasks and environments across our sites.
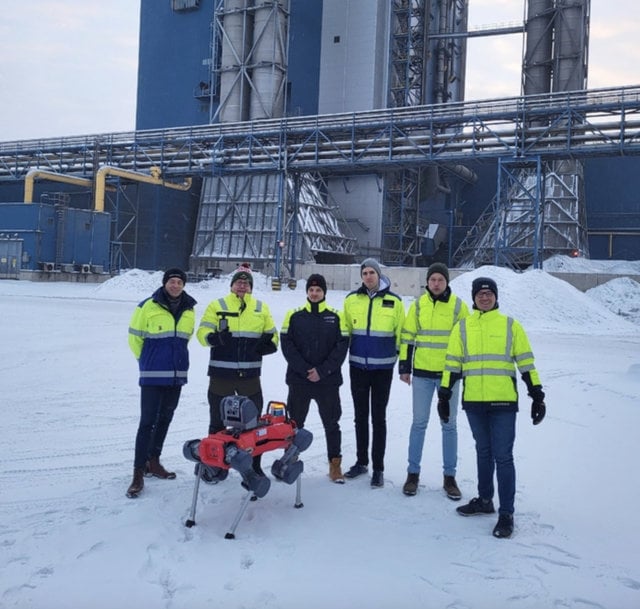
JOKKERI and the operators at Outokumpu’s Tornio Ferrochrome facility. (Courtesy: Outokumpu)
What tasks have the robots taken over, and what are the benefits?
Thorsten: Robots primarily handle inspections, such as monitoring gauges, detecting leaks, and identifying hotspots or deviations in machinery performance. This allows human operators to focus on more complex tasks while reducing their exposure to hazardous conditions. The time saved is significant—for instance, preparing for a manual inspection in the crushing area can take up to 30 minutes, time that robots can use to gather valuable data.
How are you measuring the success of robotics in your safety initiatives?
Thorsten: Our primary metric is reducing employee exposure to hazardous environments. We track the number of missions conducted by robots and the duration of these missions. Additionally, we’re evaluating the return on investment by assessing how robot-detected deviations have prevented equipment breakdowns and production interruptions.
What advice would you give to organizations considering robotics?
Thorsten: Start with a thorough risk assessment to identify areas where robotics can impact the most. Be open to diverse technologies and solutions, such as drones for height inspections. Engage your workforce transparently from the beginning, communicating the goals and benefits of automation. Collaborate closely with technology providers, challenging them to deliver tailored solutions. Lastly, celebrate small successes and involve the entire organization in the journey.
What are the long-term benefits of automation and robotics in the industry?
Thorsten:: Automation reduces manual, high-risk tasks, enabling us to leverage the expertise of our workforce better. It also facilitates the generation of valuable data, enhancing predictive maintenance and overall operational efficiency. As technology advances, the potential for safer, smarter, and more sustainable operations continues to grow.
Any closing thoughts?
Thorsten: Robotics and automation are integral to our journey toward zero incidents and a safer workplace. Collaboration, innovation, and a shared commitment to safety will ensure our success. Thank you for the opportunity to share our story.
The partnership between Outokumpu and ANYbotics highlights the transformative potential of combining advanced technology with a steadfast commitment to safety. By deploying ANYmal robotic inspection solutions, Outokumpu has not only enhanced its ability to mitigate risks but also empowered its workforce to focus on higher-value tasks. Thorsten Piniek articulated that the journey toward zero incidents is a continuous process driven by collaboration, innovation, and a shared vision for a safer and more efficient future. By leveraging robotics and automation, Outokumpu is setting new benchmarks for safety and operational excellence in the stainless steel industry, embodying its mission to create “a world that lasts forever.” This partnership is an inspiring example for industries worldwide as they navigate the intersection of technology and sustainability.
www.anybotics.com