www.ptreview.co.uk
15
'24
Written on Modified on
Cummins genset critical to frontline reliability
Preventive maintenance ensures that standby generators are ready for action when called upon in mission critical applications.
www.cummins.com
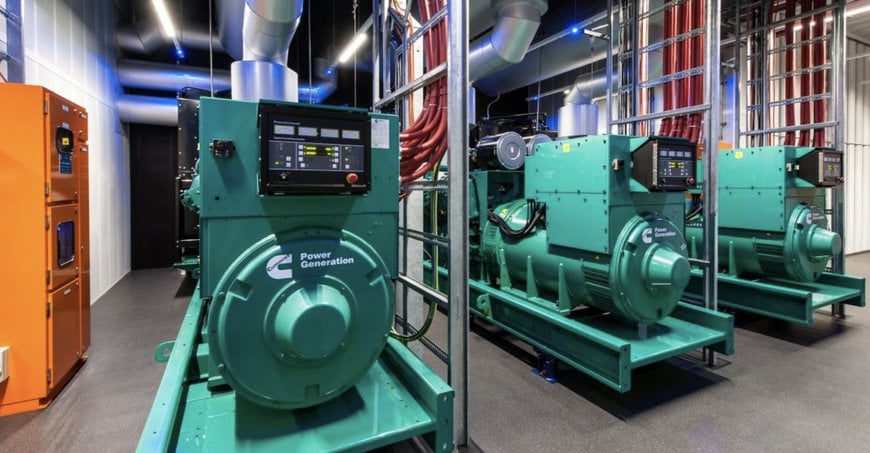
Generators failing to start are not an option for mission critical facilities. Whether for public health, national security or business continuity reasons, the reliability of the generators and standby power systems is crucial to the continued operation of these facilities.
More than 3,500 Cummins Inc. generator sets are installed in mission critical applications across the South Pacific, South East Asia and North East Asia regions – testimony to the reliability of the standby power systems and aftersales support provided by Cummins.
Cummins’ routine servicing and preventive maintenance guidelines underline the fact that generators are among the most important pieces of equipment at a mission critical facility, whether it be a hospital, data centre, airport or telecommunications centre. That importance is highlighted when the lights go out and the seconds are counted anxiously until they come back on again. Maintenance neglect is the single most common reason for genset and power system failures, says Stuart Quinn, aftermarket business development manager for Cummins Asia Pacific’s power generation business.
Peace of mind
“Cummins’ aim is to provide peace of mind with tailored service solutions that underpin power system reliability and ensure that any minor issues are identified prior to becoming major problems,” he says.
“Diesel and gas generator sets and their control systems are complex pieces of equipment so routine servicing and preventive maintenance are critical to overall system reliability.
“In Australia, we’re coming into the storm season which makes preventive maintenance even more critical if the generators need to come on line in the event of grid outages.
“It’s the simple maintenance items that are often missed, such as a coolant or fuel hose leaks, that can let you down. The aim with our service plans is to ensure that minor issues are identified before they become major problems.”
Cummins offers facility managers a range of capped price service solutions, from routine servicing on a quarterly, six-monthly or annual basis to mains failure testing – the ultimate test to know for certain that the generator will start in an emergency.
“We fully simulate a mains power failure and ‘black start’ the generators to ensure they are 100 percent operational. This can be carried out whenever the customer requires,” says Stuart Quinn.
24/7 support
All Cummins service solutions include 24/7 support with fast response and diagnosis, a 90-day workmanship guarantee and 12-month parts warranty, and a detailed service report. Capped pricing can be locked in for up to five years. Importantly, all major components of a Cummins genset are designed and manufactured by Cummins. The Cummins brand also covers digital controls, transfer switches, paralleling systems and remote monitoring.
The support capabilities Cummins has built in the Asia Pacific region are unmatched. In the South Pacific region, for example, 38 company-owned branches are dedicated to customer support in strategic locations around Australia, New Zealand and Papua New Guinea.
Factory-trained Cummins technicians carry out all generator system servicing and maintenance while Cummins’ extensive service network is equipped with comprehensive power generation knowledge to enable all makes and models of generators to be serviced.
Cummins also operates a Customer Support Centre, based in Melbourne, which is staffed 24/7 by qualified technicians and parts interpreters. The centre is available to customers in Australian and New Zealand and provides one-on-one diagnostic and technical support as a well as handling parts orders.
www.cummins.com