Stratasys Launches SAF ReLife to Repurpose Waste PA12 Powder for Sustainable Manufacturing
The new SAF ReLife solution allows manufacturers to transform waste PA12 powder into high-quality parts, cutting production costs and reducing carbon emissions by up to 89%, according to Fraunhofer IPA's life cycle assessment.
www.stratasys.com
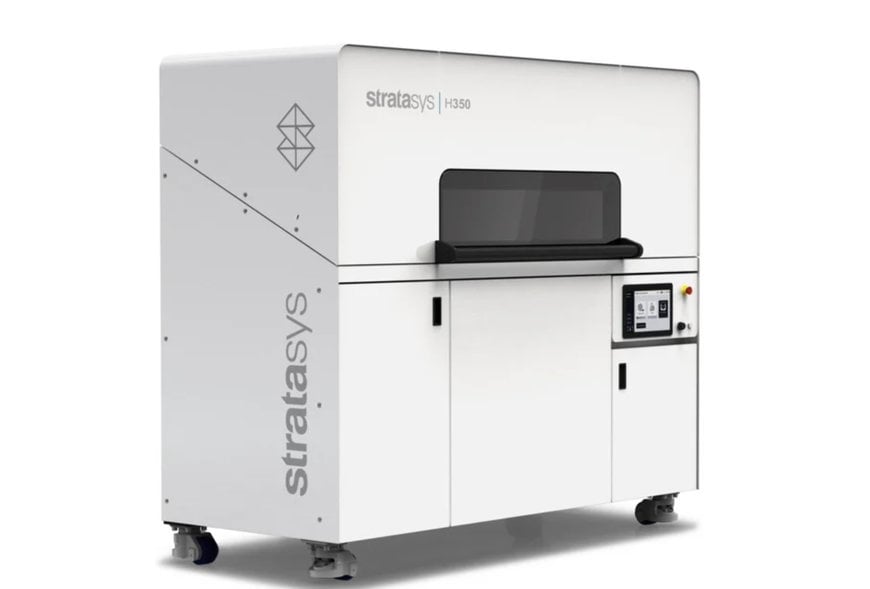
Stratasys has announced the launch of SAF ReLifeTM, an innovative software-based solution that transforms waste PA12 powder from other additive manufacturing (AM) technologies into high-quality parts.
The SAF ReLife solution can efficiently repurpose waste PA12 powder from powder bed fusion printers, including high-speed sintering, SLS (selective laser sintering) and jetting build processes for use within the Stratasys H350 printer. This sustainable solution helps customers produce high-quality surface finished parts with powder that otherwise considered waste. This new technology can significantly lower the cost-per part for customers; improve their material efficiency; and reduce their overall carbon footprint per build.
"SAF ReLife gives customers a unique ability to make high-quality parts with powder considered waste from other polymer powder bed fusion processes,” said Neil Hopkinson, Vice President, Additive Manufacturing Technology, Stratasys. “Our patented unidirectional print-and-fuse architecture and thermal control uniquely enable this capability at production volumes."
Wehl Green, a leading service bureau, beta tested SAF ReLife by utilizing their SLS waste to their SAF ReLife. The company reported significant savings of 20 percent in total cost per part and a substantial reduction in waste by turning unused powder into functional parts through a repeatable process using SAF technology. In addition, Wehl Green has been able to turn around new parts and have them delivered within 48 hours for customers, helping them meet demand.
"By utilizing the SAF ReLife technology, we’ve cut production costs while producing parts that meet strict industrial specifications. It’s a game-changer for our competitiveness,” said Javier García, Manager and Co-founder, Wehl Green. “Thanks to Stratasys’ SAF ReLife project, we’ve been able to turn PA12 waste into high-quality parts. This circular economy approach has reduced our environmental impact while maintaining top-tier product standards.”
SAF ReLife is a breakthrough in making additive manufacturing more sustainable, and eco-friendly by addressing a common challenge of what to do with aged powder. To determine the environmental impact, Stratasys partnered with Fraunhofer IPA to conduct a third-party Life Cycle Assessment (LCA) to validate the environmental benefits of SAF ReLife. The study revealed that repurposing PA12 waste from powder bed print processes in SAF production can reduce carbon footprint up to 89%, compared to standard production with polyamide 12 material.
"Our life cycle assessment demonstrates that Stratasys' SAF ReLife PA12 solution can reduce the carbon footprint of the reference print job by 43% with the German electricity mix and by as much as 89% when powered by renewable energy sources, compared to standard PA12," said Chantal Rietdorf, M.Sc., Research Associate at Fraunhofer.
Visit the Stratasys booth at Formnext 2024 in Hall 12.1 | booth D12.
Research Data and assumptions:
- The system boundaries were defined as cradle-to-gate, with the functional unit specified as one reference print job.
- Energy consumption measurements were taken at the Fraunhofer IPA for the reference print job.
- Material consumption data was obtained from the build report. For the standard PA12 a new powder share of 30% was assumed and for ReLife PA12 a share of 100%.
- The background data modeling for HAF and energy consumption utilized the Ecoinvent 3.9 database.
- The emission factor for standard PA12 was sourced from the literature, while the environmental impacts of SAF ReLife PA12 were accounted as zero, as it is a byproduct of another process (London, Michael B. (2020): Cradle-to-Gate Life Cycle Assessment of Multi-Jet Fusion 3D Printing. Master’s Thesis, University of Michigan, Michigan).
- The greenhouse gas emissions were calculated using the GWP100 IPCC2013 impact assessment method.