www.ptreview.co.uk
19
'24
Written on Modified on
TAS Enhances Electric Battery Production with Deep Learning by Zebra Technologies
TAS has improved and increased the production quality of automotive electric battery caps with a reliable, precise and secure deep learning machine vision solution powered by Zebra’s Aurora Vision Studio™ software.
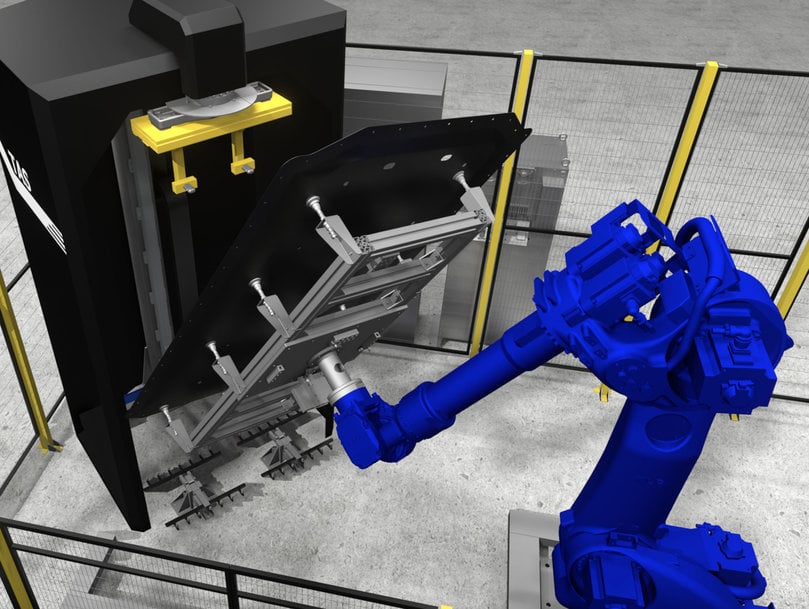
Headquartered in Kreuzwertheim, Germany, TAS GmbH is a specialist surface treatment technologies supplier. The company is integral to the precise finishing of metal surfaces – particularly those which are used for battery caps in electric vehicles that protect the high-voltage batteries from external influences such as moisture.
“The successful integration of surface treatment technology and a custom-built quality control system with deep learning represents a significant advancement in quality control and our continuous commitment to innovation,” said Temel Tas, Managing Director, TAS. “With Zebra Technologies’ machine vision system, we can meet the high-quality standards of the automotive industry, and we are already planning to implement this technology in future projects.”
To ensure a precise finish for each component, TAS follows a meticulous process. Metal sheets like battery caps are handled by a robotic system, which manoeuvres them through various stages of inspection, guided by a highly sophisticated camera system to check for possible defects that could affect the quality. Addressing TAS’ need for precision and reliability, the custom-built camera system can detect even the smallest surface imperfections that could hinder performance. In doing so, the new system has also improved the overall safety of the battery caps, and with the adaptability of Aurora Vision Studio, these safety measures are continually made even more accurate and efficient.
The cameras in the system are custom-built for TAS by ID Engineering, a Zebra Registered Industrial Automation System Integrator with machine vision specialisation. The cameras are strategically positioned to scan each component for possible defects like coating irregularities, surface scratches and laser marking issues.
“The main advantage of Zebra’s Aurora Vision Studio is its speed in development and execution time when analysing many and sometimes large image files simultaneously, which is much faster than other technologies we tested,” said Michael Sartor, Machine Vision Department Head, ID Engineering. “The scalable Zebra system is easy to use and it’s no-code solution enables fast development. Beyond the technology, we appreciate the valuable support from Zebra.”
Setting it apart from others on the market, the Aurora Vision Studio system incorporates deep learning tools that allow for continual improvement across the manufacturing process. Its ability to do this is enabled by extensive training using a comprehensive data set to recognise and classify certain types of defects using images. Previously selected image data sets are annotated and fed to the system, which can be retrained to recognise new inspection criteria based on the information or fine-tuned for defects already known to the system. As a result, the image processing solution can be constantly developed and improved using deep learning technology.
Another core benefit to the system’s deep learning capabilities is the inspection process remains flexible even when the industrial conditions change. This is a significant advantage over image processing solutions with traditional tools, which may not be as durable or adapt well to changing production conditions. The flowchart-based image processing solution with deep learning technology used by TAS follows a no-code approach which enables convenient and fast training of the image processing solution while maintaining consistent quality.
“This solution is a good example of how deep learning algorithms can be used to help ensure better quality in industrial production,” said Donato Montanari, Vice President and General Manager, Machine Vision, Zebra Technologies. “Aurora Vision Studio and its deep learning add-on provide the foundation on which even huge amounts of data can be processed and utilised. This is an important contribution to the manufacturing technology of the future.”
Key Takeaways
- TAS needed a highly accurate and adaptable visual inspection solution for the electric battery caps it provides to global automotive OEMs.
- Zebra partner ID Engineering created a bespoke vision-guided robotics solution using Aurora Vision Studio with deep learning.
- TAS has improved and increased production quality and demonstrated its commitment to innovation and quality standards.