www.ptreview.co.uk
10
'24
Written on Modified on
THE NEW SMARTREACH COMAU RESPONDS TO THE LIGHTWEIGHT COMPONENTS MARKET FOR HIGHLY VERSATILE MACHINING
Automotive, aerospace, energy and other markets can all benefit from this flexible and dynamic machining solution for better productivity and scalability.
www.comau.com
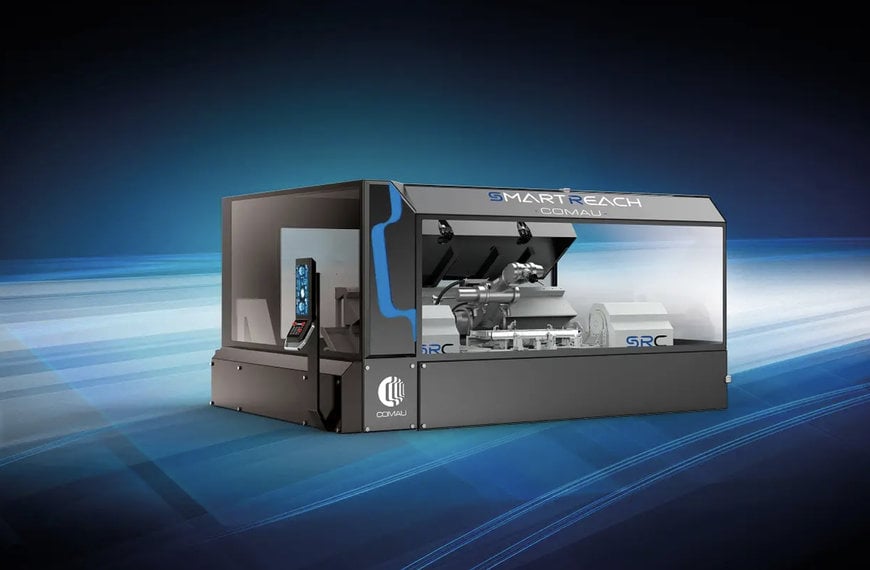
As automotive manufacturers look to increase sustainability and cost effectiveness, there is a growing demand for large structural components made of lightweight metals that can deliver better fuel efficiency, battery power range and higher cost-effectiveness.
Comau has thus enriched its next-generation machining portfolio with SmartReach Comau, a new paradigm in enhanced machining productivity, designed specifically for effective and efficient machining of large size lightweight components such as underbodies, and battery trays made by mega casting or stamping technologies.
Thanks to its unique combination of flexibility, dynamics, stiffness and accuracy, the application of SmartReach Comau caters to the automotive, aerospace, energy, and other industries, where the 5-axis flexible machining solution of oversized light material components is widely required.
The next-generation machine tool will make its worldwide debut at 34.BI-MU, Pavilion 15, Booth D10, from October 9th -12th 2024.
SmartReach Comau: Dynamic and agile machining with unwavering stiffness and accuracy
SmartReach Comau is not a traditional robot machining unit, but born as a CNC (Computer Numerical Control), with its linear X axis, reinforced rotary axes with double encoders and other specifically designed configuration, it is able to deliver high-end CNC level performance which means the combination of dynamics, stiffness and precision.
In a single part clamping posture of the part, the agile high-speed spindle can easily reach compound angles and access any side of large or multifaceted parts without frequent recourse to angular heads. In this way, it’s easy to realize one-set up machining, the key to megacasting and large lightweight parts machining (clamping the parts too many times will cause part deformation and loss of tolerance).
In a machining line, by including all the machining operations into one station, multi-machine parallel machining can reduce line stop risk due to one machine failure.
Flexibility and scalability
With its modular structure, the machine can be easily reconfigured into mono, twin spindle or multi spindle configuration, with one frame to multi-frame (frame extendable without limit), to work with different configurations of turntable (A axis, B axis single, double tables).
The standard configuration with one frame has the stroke of 3000x1890x1000mm, and with this flexibility the machine can adapt to different part sizes and different production needs.
Easy operation and maintenance
Real 5-axis continuous machining with CAD CAM and Programming G Code for machining programing and CT simulation, easy for fast model change.
Furthermore, the modular structure ensures easier reconfigurability and simple access to the installed machine, resulting in shorter mean time to repair (MTTR) compared to market standards, thus saving time, money and resources.
Most maintenance activities can be done at ground level for major operation safety and enhanced ergonomics.
Environment friendly
By using MQL or dry machining, SmartReach Comau saves coolant and reduces waste, which helps protect the environment.
Thanks to its special machine architecture, developed in full compliance with Comau’s ESG strategy, there is much less energy consumption during machining operation, compared to traditional vertical or horizontal CNC machines. In this way the energy saving can reach up to 40%.
www.comau.com