www.ptreview.co.uk
05
'24
Written on Modified on
3D Systems Expands High Precision Investment Casting Portfolio with QuickCast Air
3D Systems announced an advanced tool in its investment casting portfolio, designed to maximize material removal from the interior of casting patterns.
www.3dsystems.com
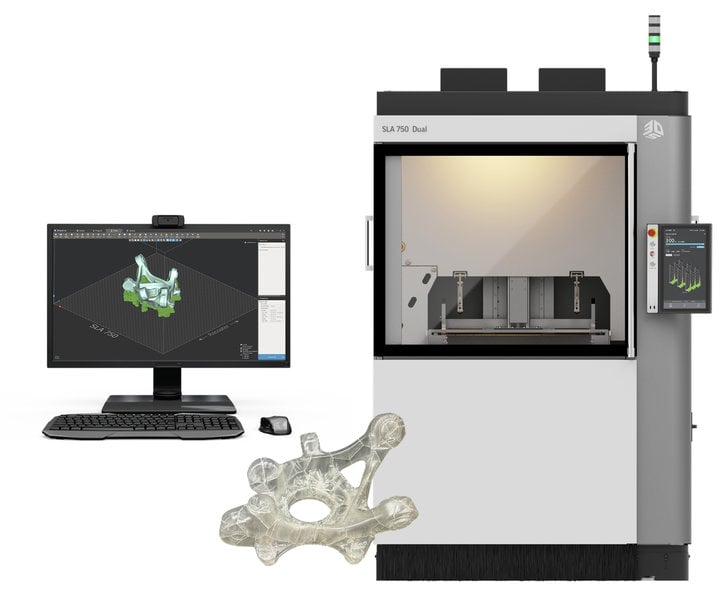
QuickCast Air enables reduced material consumption, lower pattern costs, faster build times, cleaner burnout processes, and improved draining efficiency. As a result, end-users in industries such as foundries, aerospace & defense, and energy can reliably deliver large, high-precision investment casting patterns at a fraction of the time and cost of traditional tooling and with no limitation on geometric complexity. QuickCast Air is already helping some of the Company’s large-volume aerospace customers reduce the material consumption on their patterns by up to 50%. Additionally, customers are seeing a multi-hour reduction in build times.
QuickCast Air is available to 3D Systems customers through its 3D Sprint® software which is integral to the Company’s polymer printing platforms. This feature, available via an annual subscription, allows customers to design casting patterns with fewer structures within the self-supporting walls. Using less resin and building more refined support structures results in less material needing to be burned out and thus less ash. Furthermore, having less internal structure makes it easier to drain the resin, thus retaining more within the vat during the draining process rather than being lost downstream. Within 3D Sprint, users can easily adjust the part’s shell thickness and add vents and drains on any surface, simplifying part set-up regardless of the build orientation.
Investment casting is the process of pouring molten metal into ceramic shells made from sacrificial patterns with a history that is thousands of years old. Using traditional methods such as creating a wax injection tool is both time consuming and expensive requiring several weeks and tens of thousands of dollars. In the mid-1990s, 3D Systems pioneered creating high precision casting patterns using 3D printing, introducing the manufacturing industry to QuickCast®. This 3D-printed investment casting process enables manufacturers to produce lightweight, hollow parts with 3D Systems’ polymer technologies such as Stereolithography (SLA), or MultiJet Printing (MJP) that ultimately can be used to produce end-use metal components. QuickCast patterns are recognized as the leading type of additively manufactured high precision pattern across the industry enabling manufacturers to improve efficiency and reduce cost.
As the pioneer of an industry-standard methodology, 3D Systems has demonstrated its extensive experience helping customers address their application challenges through its additive manufacturing solutions comprising materials, 3D printing technologies, software, and services. As a result, a variety of industries are able to reliably deliver large, high-precision casting patterns in a fraction of the time and at much lower cost than associated with traditional tooling.
3D Systems will showcase QuickCast Air in its booth (West Building, booth 433129) at this year’s International Manufacturing Technology Show (IMTS) to be held September 9-14 at McCormick Place in Chicago, Illinois. Show attendees are welcome to stop by to see how 3D Systems’ large-format 3D printing solutions accelerate problem-solving on the factory floor to optimize workflows, increase uptime, and extend equipment life.
www3dsystems.com