Why ‘traditional’ material handling equipment remains vital to automation
By Carl Hodges, business development manager at Gough Engineering, delves into the indispensable role of systems like batch sieves in ensuring precise, gentle material handling and seamless automated processes.
www.goughengineering.com
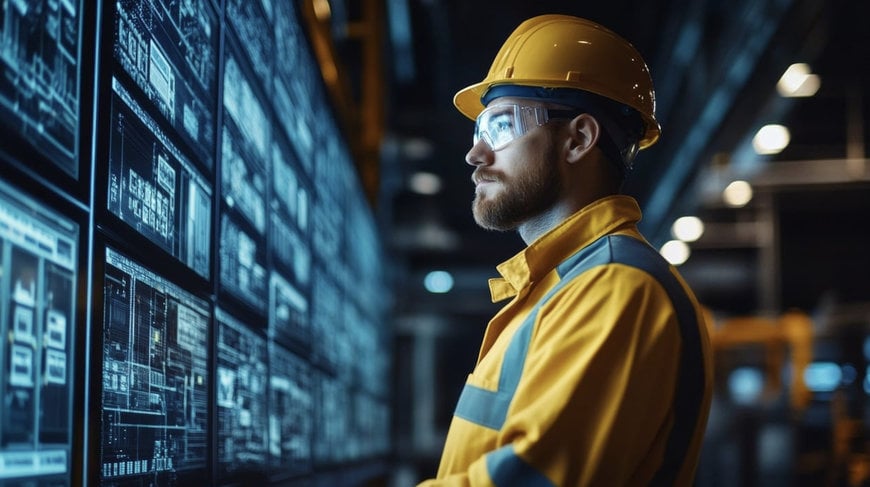
Food and beverage companies that have implemented automation achieve a 20 per cent higher growth rate than their manually operated counterparts, according to Aptean. While much attention is given to cutting-edge Industry 4.0 systems and software, traditional equipment to convey and screen plays an equally important role in material handling processes, but is frequently overlooked.
Aptean’s figures show that the transformational impact of Industry 4.0 is well established. The focus naturally turns to technologies like advanced analytics, machine learning, artificial intelligence (AI) and the Internet of Things (IoT). These innovations streamline production processes and provide valuable insights that drive continuous improvement and innovation.
Despite these advancements, traditional equipment like elevating conveyors and screens remain crucial in material handling. Innovations in traditional equipment — such as ultrasonics for de-blinding sieves or electromagnetic drives for feeders — show that these machines continue to evolve and improve, providing productivity improvements.
Adding value
Particle and product classification separation support quality control across various industries. They add value when positioned before automation systems in production lines, such as before the final packaging stage, where products are packed for distribution.
For instance, a UK-based pickle manufacturer installed a batch sieve on the line immediately before a small bag filling machine. This sieve performs a quick quality check before a semi-automated process where the product is weighed and bagged individually. In this case, the sieve ensures there are no contaminants in the final product.
Similarly, Gough Engineering provided a Swinglink elevator conveying system for a pet food manufacturer. This system transports product from the plant’s silo emptying stations to the final fully automated packing line. The elevator ensures the product reaches the packaging line without degradation or damage with the gravity feeding for onward process. Prior screening systems remove broken bits or fine particles, ensuring customers only find normal, pellet-sized pieces of pet food.
Quality checking processes with a circular sieve or linear screens are common in food and pet food manufacturing. This equipment is used before final packaging lines and other processes, such as temporary holding buffers/silos where materials are temporarily stored before proceeding to the next production stage.
Systems integration
How do these conventional material handling systems integrate with Industry 4.0? There are two key considerations. First, the physical integration of the machine into the production line, ensuring the product flows smoothly from previous processes into the new machinery and onward to subsequent processes. Proper configuration should take the following into account:
- Throughput to avoid bottlenecks
- Bulk density
- Product flow, without bottlenecks
- Product degradation
- Product dust levels during transfer
The second consideration is the integration of controls. Gough Engineering often designs equipment with standalone controls to keep operations simple. However, sometimes the controls incorporate sensors to work alongside other systems, integrating into a broader control system.
A fascinating aspect of automation over the past two decades is the development of advanced vision systems and robotics. These systems can sort products on a conveyor belt, removing defective items and ensuring only high-quality products proceed to final packing. For example, the aforementioned pet food manufacturer uses high-tech vision systems in its production lines, pushing the boundaries of what automation can achieve to retain high product quality. Nevertheless, automation can sometimes fail due to poor design or a lack of understanding of the production system, leading to costly errors, even years after implementation.
Quality control failures often result from inadequate sorting performance, highlighting the importance of statistical process control (SPC) in defining acceptable standards. Drawing from my experience, I’ve seen automation systems cause more problems than they solve due to poor design and integration, leading to significant financial losses in the long term. Companies sometimes persist with flawed systems even with a substantial initial investment, hoping for eventual improvements that never come to fruition.
Gough Engineering focuses on understanding the inputs and outputs of customers’ machines and ensuring integration with existing production lines. By incorporating modern technologies like auto-rejection systems for metal detection, Gough Engineering enhances its traditional offerings. Certain material handling systems like these require precise calibration to function correctly, rejecting only intended materials and ensuring system reliability.
Automation relies heavily on human expertise for calibration and understanding material handling requirements. It’s important to design solutions tailored to customer needs, and conduct rigorous testing to ensure proper integration and functionality. This process, if possible, may include pre-dispatch testing to verify that all components work seamlessly before installation.
Right quality, right time
While Industry 4.0 technologies propel automation forward, traditional material handling equipment remains indispensable in ensuring precise, efficient operations. Embracing both innovation and the proven reliability of traditional equipment allows businesses to achieve sustainable growth and maintain a competitive edge in the evolving landscape of manufacturing and automation.
It is possible to seamlessly integrate mechanical solutions with other automated systems to optimise production workflows. Key innovations include the Swinglink® Bucket Elevator system, the Gough Batch Sieve (GBS), Vibrecons (GVC) and Vibrofeeders, all designed to enhance operational efficiency and product integrity in automated manufacturing environments.
In conclusion, while Industry 4.0 technologies are revolutionizing manufacturing processes with advanced analytics, AI and IoT, the role of traditional material handling equipment remains vital. Equipment like sieves/separators and elevators and feeders ensure precise and gentle handling of materials, seamlessly integrating with modern automated systems. By combining the reliability of traditional machinery with cutting-edge automation, businesses can achieve higher growth rates and maintain their competitive advantage within budget.
www.goughengineering.com