Reshoring with ease: RoboCAM+ software supports transition to domestic manufacturing
Hakan Aydogdu, general manager of CNC automation system manufacturer, Tezmaksan Robot Technologies, examines how intelligent software like RoboCAM+ can help streamline production workflows and optimise resource utilisation, to empower manufacturers in their reshoring endeavours.
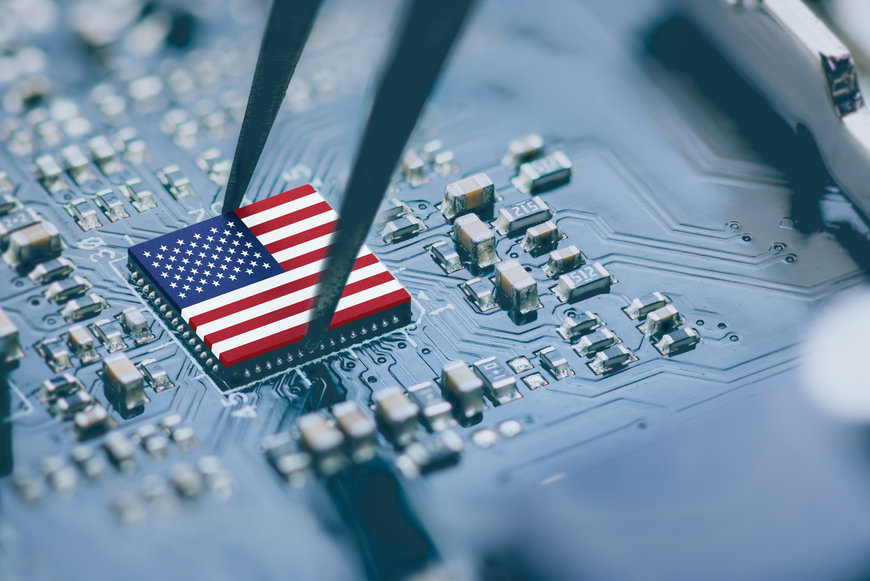
Forrester reports that, among Fortune 500 manufacturers, 30 per cent are retracting plans to reshore their manufacturing due to “significant challenges” and concerns. Reshoring is fraught with complexities that threaten its success — from supply chain blockages to interoperability issues between machinery and software.
Reshoring refers to bringing manufacturing operations and processes back to domestic territories which were previously outsourced to other countries. This decision is often driven by various factors, including rising wages in offshore locations, quality control issues, transportation costs, intellectual property concerns, supply chain disruptions and changes in government policies or tariffs. In addition, reshoring is seen as a strategy to boost domestic manufacturing capabilities, create jobs, improve supply chain resilience, and regain control over production processes.
The concept of reshoring has existed for as long as manufacturing itself but, according to the MIT Sloan Management Review (MIT SMR), “COVID-19 marked a turning point.” Discussions around reshoring increased in the second quarter of 2020 as the pandemic spread globally, and continued to grow as supply chain pressures increased following Russia’s invasion of Ukraine: “Overall, instances of executives mentioning these ideas increased nearly 3,000 per cent in just three years”
As a result, businesses started rapidly constructing domestic manufacturing facilities — including in the United States at levels unseen for many years. This surge was brought about by various factors including supply chain blockages, increased expenses in labour and transportation, tariffs imposed by the US on Chinese goods and geopolitical strains.
Yet, today, a new hesitancy has emerged among adopters of reshoring. Despite its promising aims, reshoring faces a myriad of challenges. As it turns out, these challenges are the same factors that spurred the reshoring trend in the first place: supply chain disruptions, container ship blockades and continuing geopolitical tensions.
In response, governments are offering cash incentives and tax breaks to certain industries, like batteries and pharmaceuticals, in the hopes of coaxing manufacturers back to domestic shores. But these incentives fail to address issues that are much closer to the shop floor: that overconfident early adopters are struggling to effectively harmonise their machinery, software and workforce.
Communication barriers
Machinery integration — incorporating new equipment into existing setups, ensuring compatibility and optimising workflow — is difficult in any context. Challenges may stem from differing technology standards, space constraints and the need for employee training.
Another barrier is legacy equipment that may not be immediately compatible with modern Industry 4.0 technologies. Or there might be interoperability issues between hardware and software because the shop floor relies on a mix of equipment from different vendors, sometimes operating in different silos. Solving these problems can invite substantial costs and downtime.
Likewise, software integration is essential for managing various aspects like inventory, scheduling and quality control. Transitioning to new software might be complex due to data migration issues, compatibility problems and the need for employee training.
Reshoring can also exacerbate challenges relating to workforce integration, such as ensuring employees are adequately trained to operate machinery and use software effectively. Issues may include resistance to change, lack of technical skills, communication barriers, and the need for cost- and time-consuming upskilling programs.
Given these many challenges, and the risks of failure that haphazard reshoring may bring, it’s no wonder that, as reported by Forrester, Fortune 500 manufacturers are dialling-back their relocation plans. How can manufacturers better align their machinery, software and workforce — and do so cost-effectively? Fortunately, a solution exists in industrial software programs for control and monitoring.
Simplified robot programming
To solve the reshoring challenges, manufacturers should adopt protocol and communication agnostic software platforms to control and monitor robotic operations. Such software functions independently of specific communication protocols, which allows seamless interaction and cloud communication across diverse platforms, without depending on particular technologies.
A further advantage of modern industrial software platforms is they are designed to be user-friendly, both for seasoned professionals and those who are new to automation. Not only does this significantly reduce time spent instructing the robot, software can help eliminate the complexities of robotics programming and make these tasks accessible to operators of all skill levels.
As well as sidestepping the need for time- and cost-consuming training sessions, easy-to-use industrial software platforms can help win the buy-in of employees and overcome barriers of culture and understanding — especially useful when robotic operations are being reshored from other countries back to domestic shores.
With these advantages in mind, Tezmaksan has developed its RoboCAM+ software. The platform was first developed to control Tezmaksan’s own robot automation system, the CubeBOX, a modular solution designed to automate production without human operators. However, RoboCAM+ has since emerged as a versatile software solution compatible with all robotic CNC machines, and already benefits several sectors including automotive, casting, aviation and metalware manufacturing.
Streamlined reshoring
A significant advancement achieved through the utilisation of RoboCAM+ lies in its capability to generate 3D models of workpieces. By transforming 2D CAD drawings into 3D CAM instructions, RoboCAM+ simplifies the design manufacturing process. This feature eliminates the necessity for programming and extensive CAM expertise, along with specialised training.
RoboCAM+ is the latest iteration of Tezmaksan’s RoboCAM intelligent software. Engineered for simple setup, the new version has the capability to seamlessly interpret Drawing Exchange Format (DXF) files. This feature enables operators to effortlessly upload and oversee designs, enhancing customisation and adaptability.
The system seamlessly imports solid models of the workpieces to be processed without any prior experience in robot programming. They only need to input the part dimensions, attach the tools to the robot, provide the CAD drawing of the inlay, and outline the workflow for the robot's movements. The software automatically extracts positions from the inlay drawing and transmits them to the robot. Finally, the operator initiates the process by pressing "start," and the CubeBOX commences its operation.
Moreover, RoboCAM+'s user-friendly interface facilitates the creation of transportation scenarios, enabling the robot to transfer objects or materials between different locations while considering part sizes and floor layout. Furthermore, it offers the capability to record and reuse robot movement positions.
In the face of mounting complexities, manufacturers are seeking innovative solutions to streamline the reshoring process. Tezmaksan's RoboCAM+ software represents a notable advancement in this endeavour. With its user-friendly interface and capability to seamlessly interpret DXF files, RoboCAM+ empowers operators to navigate the intricacies of reshoring with ease.
By bridging the gap between machinery, software, and workforce integration, RoboCAM+ paves the way for a more seamless transition to domestic manufacturing, ensuring sustainable growth and competitiveness in an ever-evolving global landscape.
www.tezmaksan.com