Printing a New Era for Cellular Research: The landmark project from Nano Dimension and Montpelier’s Cell Biology Research Center* (CRBM) transforming modern micropatterning techniques
Micropatterning has long been a cornerstone technique in bioengineering, enabling researchers to precisely manipulate the properties of cells and tissues – from the size and polarization of a single cell to the geometries of entire tissues.
www.nano-di.com
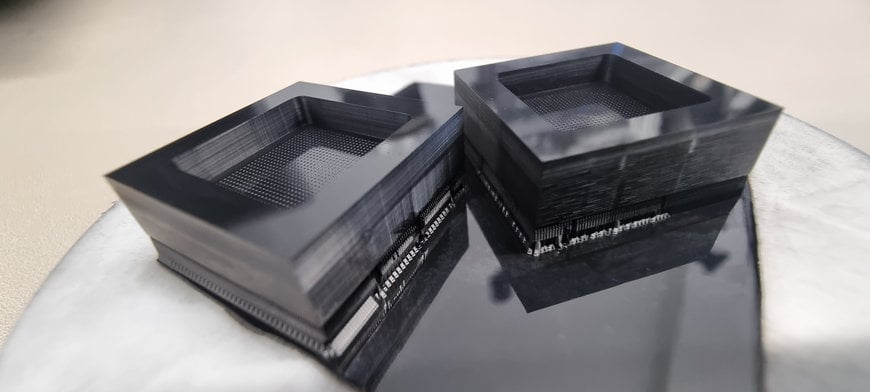
- New collaborative partnership with CRBM – a leading research unit headed by the University of Montpellier and the National Center for Scientific Research (CNRS), France – accelerates the advancement of 3D printing in creating molds for cellular micropatterning
- Traditionally created with photolithography in a time- and cost-heavy process, the new 3D printed molds – produced with Nano Dimension’s micro-3D printing Fabrica technology – have been successfully utilized by CRBM to grow fluorescent protein in hydrogel
- By reinventing the mold development process and proving real-world success, the new project unlocks unique possibilities for cellular research along with a host of efficiencies, democratizing access to micropatterning
Traditionally, creating the necessary molds for this process has relied heavily on photolithography, a method that, while highly effective, is also labor-intensive, time-consuming, and costly. However, as the demand for rapid prototyping grows, the scientific community like many other sectors is increasingly turning to additive manufacturing (AM) as a more efficient alternative.
Today, by enabling researchers, in a matter of hours, to 3D print molds that would traditionally have taken weeks to produce, the switch to AM is not only accelerating scientific research and innovation, but also democratizing access to advanced micropatterning capabilities that could be key in all manner of future research.
Understanding the research field today: why AM is changing the game
The ability to 3D print molds in just a few hours enables the CRBM team to democratize access to advanced micropatterning capabilities that could be key to future research
Engineering a new frontier: navigating a challenging landscape
Working at the cutting edge of its industry sector, the CRBM team embraced the opportunity to realize substantial time and cost savings by leveraging advanced micro-contact printing techniques with AM in its cellular research. By providing a new means of casting the PDMS mold and enabling the research team to print fluorescent proteins on to a hydrogel, the team would stand to prove the viability of the process for bioengineering research and material science moving forward – driving the industry forward and opening up new avenues for future research.
However, working with such small and exacting measures leaves little room for error – meaning the 3D printing technology would need to provide an unprecedented level of accuracy and precision, down to mere microns. Beyond this, the process would also need to meet stringent and extremely specific requirements in terms of material properties, in order to prove valuable and effectual in the field. With a margin for error as narrow as 5µm, the possibility of turning to AM to solve research challenges, simplify and accelerate processes, and open up new possibilities would be entirely dependent on whether the technological capabilities were ready to match its precise demands.
3D printing ushers in a new era
Far from the norm when experimenting with new techniques and processes, what the team at CRBM found when delving into the world of nano-level micro-contact printing was something that not only enabled meticulous control from design to end result, but a solution that proved successful from the very first print.
Teaming up with Nano Dimension, leaders in precision polymer-based micro-3D printing/ AM solutions, the research team was introduced to the capabilities of the company’s Fabrica technology. Employing digital light processing (DLP) to deliver automated, best-in-class precision with resolution down to a single micron, the Fabrica-based Terra solution was able to provide functional, micro-3D printed parts at breakthrough speed, with all the critical material properties and performance qualities previously dependent on the complex photolithography process. Straight from design, the team was able to utilize the 3D printed molds to effectively seed proteins as needed, ultimately resulting in the successful creation of engineered tissues with a catalogue of custom properties.
Enabling researchers to directly translate digital designs into physical models of the PDMS molds, leveraging Nano Dimensions’ solutions bypassed the need for photo masks and UV exposure. This not only reduced the number of steps involved, but thereby also minimized the potential for errors associated with traditional photolithography.
One of the most significant advantages for the team at CRBM, however, came from the ability to facilitate rapid prototyping. By employing Nano Dimension’s advanced technologies, researchers could now quickly produce and test multiple iterations of a design, refining their patterns based on immediate feedback. With rigid and limited timelines often proving a vital factor in the team’s research, this agility proved a particularly valuable – and promising – development.
A new outlook for future research
While photolithography still remains cost-effective and competitive for large-scale production, the initial investment and ongoing operational costs can prove prohibitive for smaller-scale projects or early-stage research. AM, by contrast, offers a scalable solution, proving to reduce costs by hundreds of pounds per mold for the team at CRBM. For small quantities or single prototypes, AM is not only more affordable but also faster, allowing researchers to pivot quickly and explore new ideas without the financial burden of large-scale production methods.
Produced with Nano Dimension’s micro-3D printing Fabrica technology, the new 3D printed molds have been successfully utilized by CRBM to functionalize hydrogel with micropatterned, fluorescent protein
Conclusion
By proving the viable transition from photolithography to AM for micropatterning, the collaborative project with Nano Dimension and CRBM marks a landmark development in bioengineering research. Being able to offer a faster, more cost-effective, and accessible new production process, AM empowers researchers to innovate with unprecedented speed and flexibility – with Nano Dimension’s technology at the center of this new field of possibility. Perhaps the most exciting aspect of the project, however, is that it represents just the beginning of our exploration of micro 3D printing across the biomedical landscape. As this technology continues to evolve, its impact on research and development will undoubtedly grow alongside, paving the way for new breakthroughs and applications in bioengineering and beyond.
* Centre de Recherche en Biologie Cellulaire de Montpellier
www.nano-di.com