French Navy Validates Meltio's Metal 3D Printing for Part Manufacturing and Repair
The French Army utilized a Meltio wire-laser metal 3D printer for remote assistance in an offshore maneuver, utilizing its unique additive manufacturing technology to repair and fabricate stainless steel parts on board.
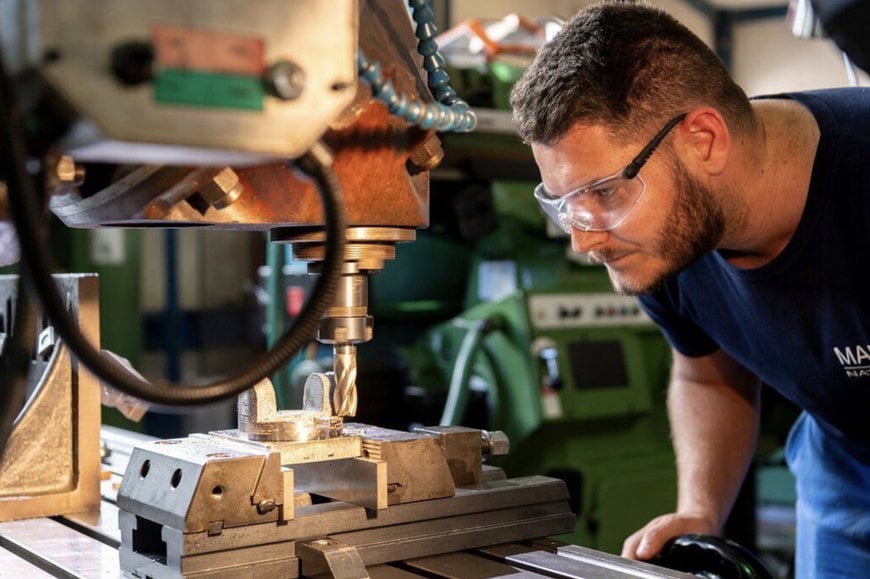
The French Navy has validated the use of the unique additive manufacturing technology developed by Meltio for real maneuvers. The Spanish multinational has thus achieved the third approval of its metal 3D printing technology for the defense sector. In this case, the French Navy joins the incorporation of Meltio's technology by the US Navy, which has successfully installed a Meltio solution on board a military vessel. This technology has also been validated by the Spanish Army, which already uses Meltio 3D printing solutions in its manufacturing and repair processes for metal parts.
The validation of Meltio's technology by the French Navy has occurred recently, during military maneuvers carried out at the end of last May while using a Meltio metal 3D printer on an experimental basis and after passing the adoption tests of its unique metal 3D printing technology over the last few months. The French Ministry of Defense has made this milestone public by assessing the effectiveness of the solution and confirming it continues to validate the Meltio solution.
The French Navy is already considering including it in upcoming real-life maneuvers and may even incorporate it on board ships in its fleet in the future.
Metal 3D printer developed by Meltio and used by the French Navy. Photos: Marie Bailly / French Navy / Defense //Jeremy Vacelet / French Navy
Meltio has consolidated its unique metal additive manufacturing technology in the defense sector. The Spanish multinational based in Linares (Jaén) has been passing different technological tests on its hardware, metallic materials and software worldwide. Meltio has become a strategic and reliable partner, meeting the high demands of different armies around the world with its disruptive 3D printing technology.
In addition to these milestones, Sicnova, Meltio's distributor in Spain, signed a contract with the Spanish Ministry of Defense at the end of 2023 to introduce additive manufacturing in the three Spanish armies for the next four years.
Currently, armies in other countries are in the process of validating Meltio's unique additive manufacturing technology. This interest from the defense sector is also opening the door to companies in the aerospace sector that are already validating the Spanish multinational's technology.
Meltio assists the French aircraft carrier, Charles de Gaulle
The French aircraft carrier Charles de Gaulle has been experimentally using a metal 3D printing solution provided by Meltio. In May 2024, as part of the "Ursa Minor" exercise - a high-intensity operational maintenance naval exercise organized by the Fleet Support Service (FSS) - a special breakdown repair experiment was carried out in the workshops of the Navy's logistics department in Toulon. Meltio's technological solution is installed on shore at the Toulon arsenal and is receiving requests for the manufacture and repair of metal parts from the aircraft carrier.
Stainless steel 3D printed part created by the French Marine Nationale with Meltio additive manufacturing equipment. Photos: Marie Bailly / French Navy / Defense //Jeremy Vacelet / French Navy
Meltio's 3D printer works with various types of materials, including stainless steel, titanium, Inconel, mild steel and tool steel.
3D printing technology experimentation exercise enables the supply and repair of fully dense parts for various industrial applications. These parts are manufactured at a low production cost per cubic centimeter. In addition, the speed of execution and efficiency are such that production is more competitive than with traditional manufacturing methods," stresses the French Navy.
Another aspect of the technological challenge faced by the French engineering team was that the part to be manufactured had to be made of metal, a first for the department, which had never used this manufacturing process before. Meltio's technology works by Direct Energy Deposition (DED), i.e. the stacking of welding wires on top of each other, in the form of wire introduced into a molten bath generated by a laser. It is based on digital modeling of the replacement, which is an essential prerequisite for production.
The use of metal 3D printing makes it possible to supply fully dense parts for various industrial applications. These parts are manufactured at a low production cost per cubic centimeter. Moreover, the speed of execution and efficiency are such that production is more competitive than with traditional manufacturing methods, such as boilermaking, forging and others.
French Navy engineer using Meltio metal 3D printing equipment. Photos: Marie Bailly / French Navy / Defense //Jeremy Vacelet / French Navy/ Defense
Jean-Marc Quenez, director of Innovation and Additive Manufacturing at the Service de Soutien de la Flotte (SSF) of the French Ministry of Defense assures:
"We are at a point of overcoming technological tests of the Meltio metal 3D printer for the French Navy. Its state of use is experimental. The French Navy is using this Meltio machine on land. The machine is installed at our naval base, the Arsenal, located in the city of Toulon. After months of preliminary tests at our technology center in Toulouse, south of France, to test Meltio's wire-laser DED technology (direct material deposition with laser melting technique as welding), the transfer of the printer to Toulon was approved. The main objective of this transfer is to respond to the Navy ships that are sailing with their repair and manufacturing needs in different metallic materials, mainly stainless steels and Inconel, for which Meltio's additive manufacturing system is very efficient in the result of the parts obtained".
Quenez continues: "Last May, we conducted the Ursa Minor 2024 offshore exercise, in which the Charles de Gaulle aircraft carrier requested us from its internal naval engineering center to repair metal parts. It was at that moment that we turned to Meltio's metal 3D printing technology. Let's say that this machine performs a function, for the moment experimental from land and in tests, of land-sea tele-assistance. The exercise was a success. We plan to carry out more exercises of this type over the coming months and in the future, the French Army is considering incorporating this type of metal 3D printer on board."
He adds, "We chose Meltio for this exercise because it allows us to repair existing metal parts and with this machine, we manufacture test parts with DED technology, not final parts that we then post-process and machine according to our needs. The Spanish brand's metal 3D printer meets our expectations for reliability and is very easy to use by our engineers. We anticipate that this metal 3D printer will continue to be functional and will be part of our experimental additive manufacturing usage program that continues to evolve."
Since its foundation in 2019, Meltio has achieved relevant projects in Defense, consolidating and strengthening its technology and positioning itself as a strategic business partner for the manufacture and repair of metal parts in different industrial sectors, among which the defense sector stands out. Its technology is based on the patent of a 3D printing head capable of melting various metallic materials using lasers and the welding wire technique.
Other Meltio milestones in defense:
Meltio solution aboard the US Navy ship USS Bataan.
Meltio together with its U.S. distributor Phillips Corporation - a global leader in U.S.-based manufacturing solutions - have collaborated to install for the first time on a US Navy ship a metal 3D printing solution for onboard manufacturing of spare parts and repairs. The Phillips Additive Hybrid powered by Haas took Meltio's laser metal deposition technology and integrated it with the world-renowned Haas CNC vertical machining center control milling machine aboard the USS Bataan. The equipment, installed as part of a joint effort between the Commander, Naval Surface Force Atlantic and the Naval Sea Systems Command (NAVSEA) Technology Office, includes the Phillips Additive Hybrid system, which integrates a Meltio wire laser metal deposition head on a Haas TM-1 computer numerical control milling machine.
Installation of the hybrid solution integrating Meltio's 3D printing solution on board the US Navy ship USS Bataan. Norfolk (Va, USA). Kenya Latham, assigned to East Coast Repair coordinates the loading of a Meltio 3D printer head aboard the Wasp-class amphibious assault ship USS Bataan (LHD 5). Photo by Communication Specialist Darren Newell/Released.
The first 3D printed part with Meltio solution aboard USS Bataan
Another milestone in the United States is the first part printed on board the US Navy's USS Bataan, demonstrating the successful results of the Meltio hybrid system installed aboard this warship, in this case on a computerized machine or CNC milling machine. The ability to obtain spare parts at sea is a challenge, especially considering that space is at a premium and many decades-old parts are nearly obsolete.
Hybrid solution with Meltio metal 3D printing head installed on a CNC milling machine installed on board the US Navy ship USS Bataan, in collaboration with Phillips Corporation in the US and Haas milling machine. Photo: Phillips Corporation.
The U.S. Navy ship USS Bataan is addressing the problem by being the first to deploy a hybrid manufacturing system that includes the Meltio head on a milling machine and provides sailors with industrial-grade manufacturing capabilities.
Meltio's solution enabled a replacement 3D metal plate for a ballast air compressor (DBAC) to be manufactured in just 5 days, rather than potentially taking weeks to supply through conventional Navy supply channels.
3D printed part with Meltio 3D printing equipment on board the USS Bataan (US Navy).
The part is used to force pressurized air through saltwater tanks and discharge accumulated saltwater. The tanks are filled to reduce the ship's draft in amphibious operations. Fabrication of the metal sprayer plate offshore allowed the ship to reduce the time required to obtain a spare assembly.
Meltio, technology awarded by Xtech and the U.S. Department of Defense.
Meltio's success aboard the USS Bataan enabled the Spanish brand to achieve technological confidence and accreditation in the United States. Thus, the U.S. Department of Defense (DoD) has awarded Meltio's technology with XtechInternational, which means recognition as a "strategic technology partner" in the current and future development plans of that country in the military and security field. This is the first time that a Spanish company has received this award in the field of additive manufacturing.
Equipo de profesionales en la sede de Meltio, en Linares (Jaén) con el premio Xtech de Estados Unidos. Foto: Carolina Vilaplana
Milestone of Sicnova, Meltio distributor, with the Spanish Ministry of Defense
Soluciones Sicnova, distributor in Spain of Meltio’s solutions, has signed an agreement with the Ministry of Defense to implement in four years "joint actions for the development and implementation of a digitalization strategy to simplify the manufacture of parts and spare parts in their supply chains".
Defense aims to improve the supply and logistics chains of the Armed Forces, increase the operability of fleets, resources in operations and avoid problems related to the obsolescence of parts and pieces, as well as increase their useful life through a strategy of design and additive manufacturing that allows the development and manufacture of parts, spare parts and tooling.
www.meltio3d.com