www.ptreview.co.uk
11
'24
Written on Modified on
Wistron Advances Energy Efficiency in Manufacturing with AI and NVIDIA Omniverse
They enable the early detection of issues that are crucial for strict quality control and compliance with industry standards in electronics manufacturing with the performance of run-in test rooms, which are essential for ensuring the reliability, quality, and safety of the world’s electronics products.
www.nvidia.com
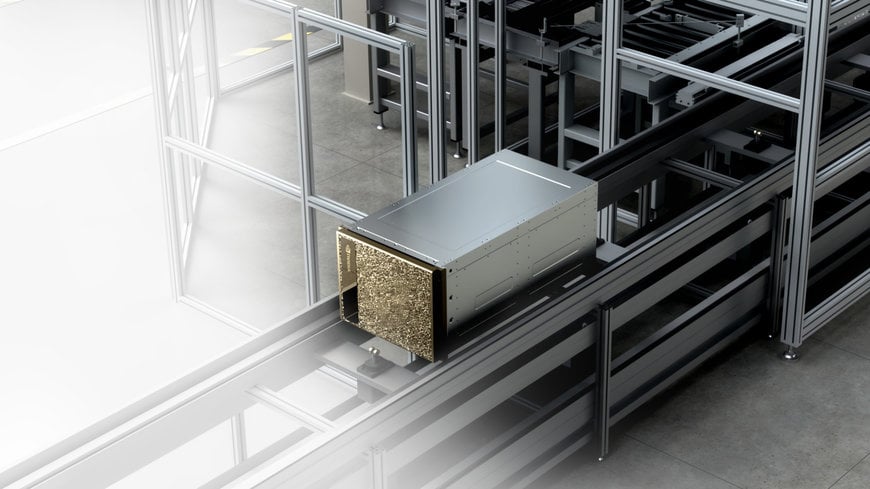
In this spotlight, we explore how developers at Wistron, one of the world’s largest suppliers of information and communications products, built a digital twin platform and AI-enabled simulation tools to ensure optimal design, performance, and energy efficiency of the run-in test rooms in their new NVIDIA DGX and NVIDIA HGX factories, delivering potential savings on energy consumption of up to 10%.
Enhancing operational efficiency with OpenUSD and AI
To help their teams enhance the energy efficiency and productivity of their run-in test rooms and their simulation workflows, developers with AI/ML, IoT, and 3D modeling skills built the Wistron Digital Twin platform on the NVIDIA Omniverse platform, which is powered by Universal Scene Description (OpenUSD) By using OpenUSD, they connect their digital twin platform to their building management system and IoT hub. With these integrations, they now have access to real-time data from thousands of physical sensors in their physical facilities, including the core temperature, inlet temperature of supercomputing facilities, and the return temperature of air conditioning systems.
This has unlocked real-time collaboration for their remote teams, enabling them to streamline the review of facility layouts and accelerate decision-making in facility planning and operations. Wistron developers also built and integrated physics-informed AI models into the Wistron Digital Twin platform, using the open-source NVIDIA Modulus framework. These AI models enable their simulation experts to accelerate their work, improve thermal dynamics, and reduce risks in their facilities. With these new capabilities, teams can make sure that cooling systems deliver peak performance, even under the most demanding conditions.
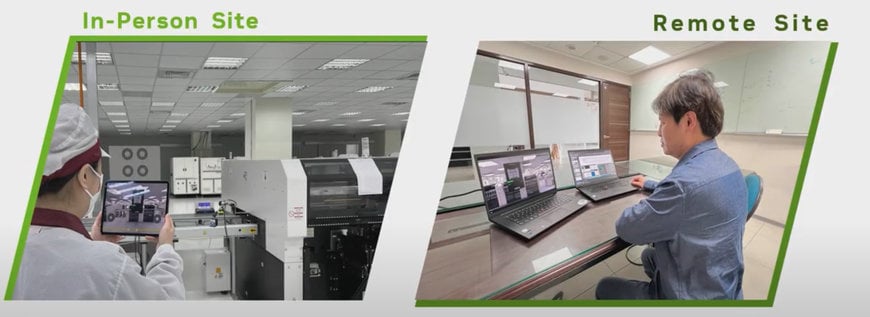
Side-by-side images demonstrating digital twin interaction: a facility worker uses a tablet locally, while the plant manager accesses it remotely through a laptop
Building digital twins of test rooms
To build their digital twin platform and digital twins of their test rooms, Wistron used OpenUSD to unify their data pipeline and streamline their workflows. The 3D models are modeled by their 3D experts using OpenUSD. This approach enables their teams to standardize the asset creation process. It also ensures that assets are easily manageable and compatible across the various software and simulation tools used by their teams.
“OpenUSD provided the benefit of flexible data modeling for us to combine a variety of data and outcomes of various 3D modeling and simulation tools,” said John Lu, plant manager at Wistron. OpenUSD has, for example, enabled a connection between their digital twin platform and the Autodesk FlexSim simulation software, further enhancing their teams’ ability to simulate, analyze, and experiment with critical manufacturing processes. Wistron developers built a custom extension to import data and parameters from FlexSim. Then, they used an OpenUSD-native Omniverse Connector to integrate data from FlexSim into their digital twin platform.
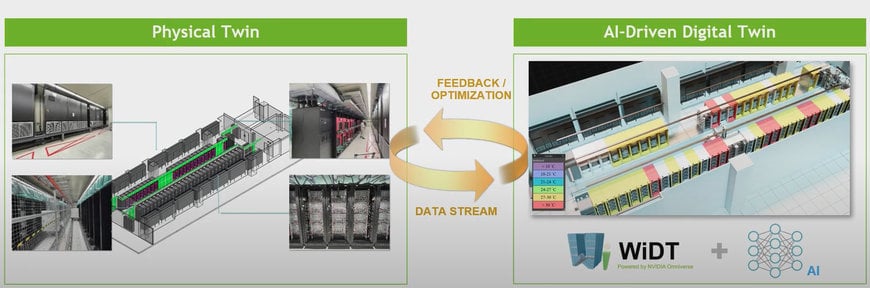
A diagram showing how Wistron’s Digital Twin Platform is connected to the physical facilities
Accelerating simulation and predicting risk with physics informed AI
Wistron’s simulation experts rely on computational fluid dynamics (CFD) simulations to support the design and management of their run-in test rooms. Increasingly, their experts recognized that their CFD approaches, running on general-purpose computing architectures, lacked the flexibility their teams required. Conducting these thermal simulations took their teams significant time and resources to yield the required simulation data. When design parameters changed, results became invalid and simulations had to be re-run. To help their simulation experts address these challenges, they built and integrated additional capabilities into their digital twin platform, including:
- Physics-informed neural networks (PINNs) using NVIDIA Modulus, a powerful open-source framework for developing AI surrogate models. This approach speeds up airflow simulations, reducing a process that previously took their teams 15 hours to 3.6 seconds—a 15,000X speedup.
- An AI-based extension that enables simulation experts to visualize and analyze CFD simulations in high fidelity to minimize the load on cooling systems and lower operating costs, all while maintaining peak productivity.
- A recommendation system for their automated storage and retrieval system (ASRS) to identify optimal testing locations and autonomously place new supercomputing baseboards in locations with the least thermal risk.
- With these new capabilities, they can approximate the underlying physics of their thermal systems, enabling them to conduct fast and accurate predictions of temperature distributions and thermal behaviors within their run-in test rooms. Teams can now pinpoint hotspots in the facility and forecast core temperatures for the upcoming 30 minutes.