www.ptreview.co.uk
26
'23
Written on Modified on
Enemac Introduces Torque limiter ECP for indirect drives with integrated ball bearing
To protect high-quality machine components in the powertrain from overload, ENEMAC offers a wide range of mechanical torque limiters for all areas of engineering.
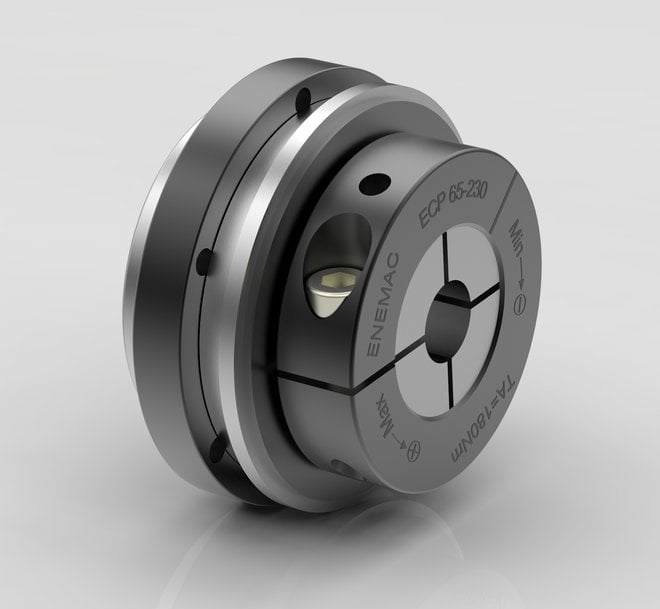
Safety couplings from ENEMAC are compulsory. Split secondly, they interrupt the torque transmission. The separation of drive and output is purely mechanical and thus independent of power failures and similar disturbances.
A variant designed for indirect drives is the ECP torque limiter equipped with integrated ball bearing. It separates on the spot by the use of disc springs, which guarantee a large adjustment range without disc spring exchange. One tab location per revolution in the sophisticated ball detent principle ensures separation of the drive train within a few degrees of angle and automatic re-engagement after 360 °. It is ideally suited for high bearing forces with the best concentricity.
By using a proximity switch, the stroke of the balls can be interrogated and the resulting signal can be given for switching off the drive to the supervision. The overload clutch ECP is mounted on the shaft by means of a mounting-friendly clamping ring hub. The advantage of this hub lies mainly in the easy disassembly, which prevents destruction of the hub. 19 sizes between 0,5 Nm and 9,000 Nm disengaging torque are available. The shaft can have a diameter of up to 120 mm, at speeds of up to 4,000 min-1.
For demanding environments, ENEMAC also offers this safety coupling as corrosion-resistant variant ECP_KS. For this purpose, the main components of the torque limiter are nitro-carburized or gas-nitrided and then oxidized. The built-in disc springs are coated, bearings and further small parts are made of stainless steel. This makes the coupling type suitable for many outdoor applications and wherever moisture could become a problem.
A variant designed for indirect drives is the ECP torque limiter equipped with integrated ball bearing. It separates on the spot by the use of disc springs, which guarantee a large adjustment range without disc spring exchange. One tab location per revolution in the sophisticated ball detent principle ensures separation of the drive train within a few degrees of angle and automatic re-engagement after 360 °. It is ideally suited for high bearing forces with the best concentricity.
By using a proximity switch, the stroke of the balls can be interrogated and the resulting signal can be given for switching off the drive to the supervision. The overload clutch ECP is mounted on the shaft by means of a mounting-friendly clamping ring hub. The advantage of this hub lies mainly in the easy disassembly, which prevents destruction of the hub. 19 sizes between 0,5 Nm and 9,000 Nm disengaging torque are available. The shaft can have a diameter of up to 120 mm, at speeds of up to 4,000 min-1.
For demanding environments, ENEMAC also offers this safety coupling as corrosion-resistant variant ECP_KS. For this purpose, the main components of the torque limiter are nitro-carburized or gas-nitrided and then oxidized. The built-in disc springs are coated, bearings and further small parts are made of stainless steel. This makes the coupling type suitable for many outdoor applications and wherever moisture could become a problem.
www.enemac.com