www.ptreview.co.uk
22
'23
Written on Modified on
Intralogistics Flexibility meets Delta Line Flexibility
This case study will introduce how Delta Line motion solutions help the next generation of Autonomous Mobile Robots (AMRs) overcome movement, size, and payload challenges.
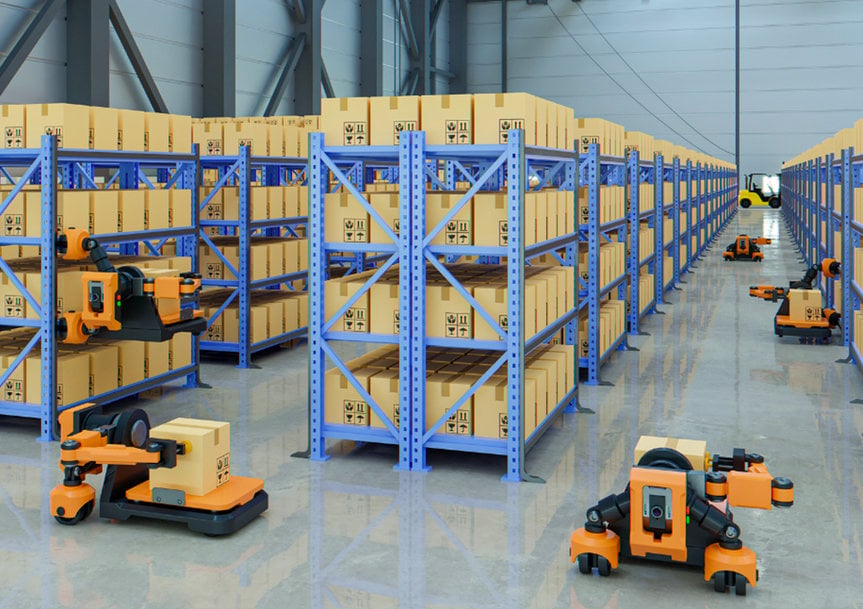
Delta Line is integral to the motion of many applications all over the world. We are immersed in a wide range of industries such as agriculture, healthcare, intralogistics, robotics, and even consumer products. We are a trusted partner because of our dual value proposition: we provide a large catalog of customizable products and have a collaborative global engineering presence. We meld our motion solution expertise with the application knowledge of our customers to create breakthrough technologies and products.
The challenge of space optimization: Horizontal and Vertical Movement Planes
The technology to support e-commerce warehousing, distribution, micro-fulfillment, and storage facilities continues to evolve as hardware and software mature. Most of these facilities today depend on Automated Storage and Retrieval Systems (AS/RS) which offer incredible benefits in terms of space usage optimization, efficiency, accuracy, and speed. AS/RS is comprised of the hardware (i.e., racks, retrieval equipment, and shuttles) and is controlled by the Warehouse Management System (WMS) and Warehouse Execution Software (WES).
Typically, shuttles are used in these systems to transport inventory inside the warehouse to improve efficiency and reduce employee walk time. Floor shuttles can be categorized into two families: Autonomous Mobile Robots (AMRs) or Automated Guided Vehicles (AGVs). AMRs are sophisticated robots, equipped with artificial intelligence, machine learning, and sensors to help them travel independently within the warehouse with limited human intervention. Contrast this with AGVs which are guided by magnetic strips, wires or sensors, and travel along pre-defined routes. If we compare an AS/RS system to a human body, the AS/RS hardware is the skeleton while the AMRs or AGVs are the blood cells that move throughout the system.
Infrastructure varies widely between distribution, micro-fulfillment centers, and warehouses. Each warehouse might be slightly different but all are designed to maximize both horizontal and vertical storage space. Maximizing vertical usage is done in many different ways with varying levels of complexity: fixed cranes, robotic shuttles, or cube-based storage systems. Our customer’s mission is to develop a package retrieval AMR that moves both horizontally (along the warehouse floor) and vertically (up the rack structure).
A fully independent AMR robotic shuttle with a guidance system, wheels, and vertical package retrieval system requires a large number of onboard motors and control electronics. Motors are required to: turn the drive wheels, extend the telescopic package retrieval arm, reposition the wheels for rack or floor movement, actuate box grippers, and engage the elevator system. Each motor had to be configured for its dedicated motion. The Delta Line engineering team collaborated with the customer’s engineering team starting from the initial concept phase. Together we designed and defined the right 12 onboard motors and control electronics.
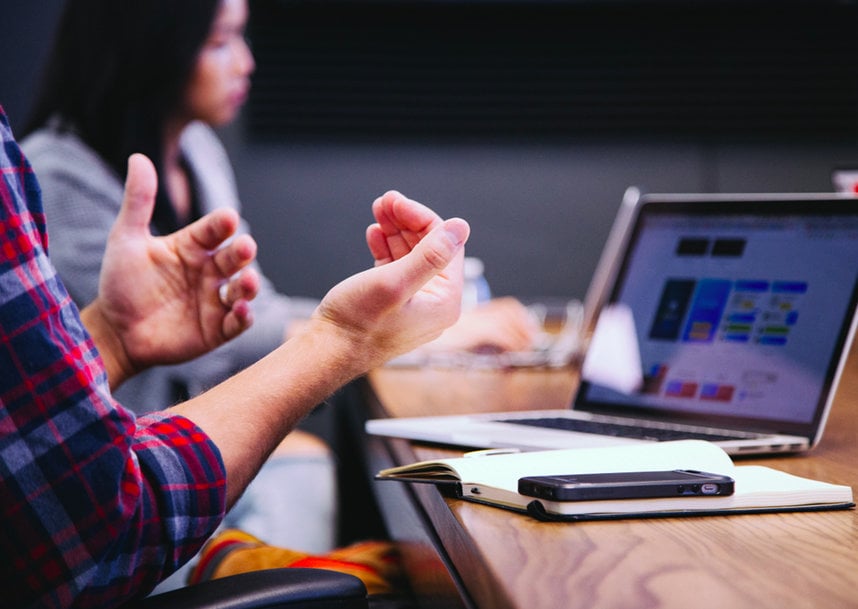
Thanks to the early collaboration, our expertise, our company-wide portfolio, and our customization capabilities, we have been able to create a very efficient motion system in terms of performance, volume, cost, and assembly. The Delta Line product portfolio includes multi-axis drives which support up to 3 motors. For this AMR, the 12 total motors are controlled by 4 custom drives.
Nimble Robots and Our Solution
Robot dimensions, payload size, and overall weight are the critical elements that an AMR manufacturer must manage, especially considering the battery-powered nature of these shuttles. The tendency is to focus on space and weight reduction at the component level. However, it is crucial to consider the complete motion system from the beginning of the project. Wiring and connectors, for example, are often the cause of extra space usage. The ability to design the right motion system answers both the performance needs and reduces the overall robot size.
AMRs and AGVs require a large number of motors, and even more so as extra functionalities are added. To answer the mechanical needs of this application we opted for a combination of 8 BLDC motors and 4 Servomotors. The controls presented a greater challenge. The electronic system needed to handle high current levels (greater than 10A rms), be exclusively based on EtherCAT communication fieldbus and include specific brake digital outputs. Given the Delta Line customization capabilities and flexibility, we were able to develop a tailor-made 3-axis EtherCAT control for currents up to 12A rms.
This multi-axis drive solution was selected because of its advantages in reducing component footprint (fewer drives and wiring) and cost efficiency. Since there are few higher-current 3-axis drives for the growing AMR and AGV industry, we added these 3-axis drives to our standard portfolio. Today, our Phoenix drives are readily available through our catalog in two versions: a smaller embedded model (without a housing) able to control BLDC motors up to 3A rms and a standard housed version controlling BLDC motors up to 12A rms.
The control Delta Line has over our electronic manufacturing process allows us to easily provide customized firmware for plug-and-play-ready systems without requiring prohibitively large MOQs. We bring the right-fit motion solution and simplified supply chain to the table so our customers can focus on their software. It is intralogistics and mobile robot customers like ours that are changing the landscape of e-commerce, warehousing, micro-fulfillment, distribution, and storage facilities. Configurable and customizable Delta Line motors and drives help the next generation of autonomous mobile robots overcome movement, size, and payload challenges. Our flexible products and collaborative global engineering presence is an asset for intralogistics developers.
There’s a simple, yet often neglected, piece of advice which applies to every project involving a motion system: start talking to your motion solutions system provider sooner rather than later. This applies even if your own design team includes experienced mechatronics engineers, because they are unlikely to have the expertise and wealth of specialised knowledge that the provider’s engineers, who work day in, day out with motion solutions, can bring to your project.
www.delta-line.com