www.ptreview.co.uk
19
'22
Written on Modified on
Antaira: A New Vision For Robotics, Gives Industrial Robots Human-like Functions
General Motors (GM) incorporated the world’s first robots into an assembly process back in 1962. Although primitive by today’s standards, these robots opened new possibilities by performing dull, repetitive tasks automatically and more accurately than humans.
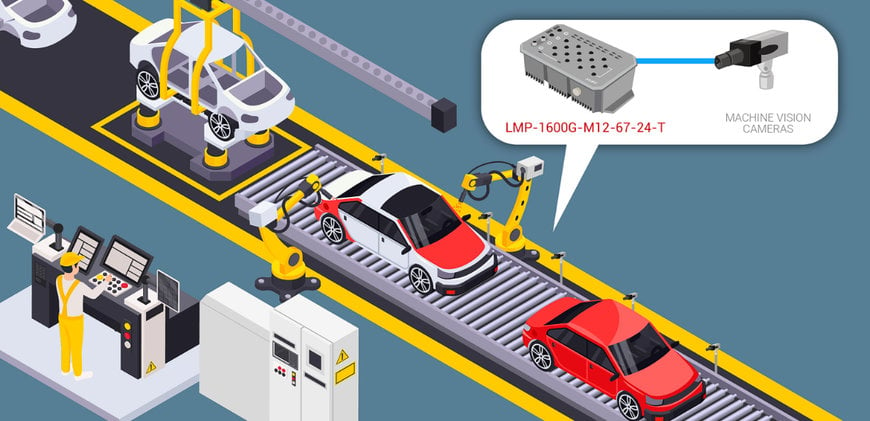
Reducing workplace danger was another benefit for GM. For instance, large car parts previously requiring multiple workers to lift into place could be hoisted up by a single robot, increasing safety along with productivity.
At about the same time another industrial revolution was emerging — machine vision. Consisting originally of low-resolution monochrome analog cameras strung together with coaxial cables, machine vision systems quickly evolved to tackle complex inspection tasks such as edge detection, Optical Character Recognition (OCR), presence detection, and segmentation with far more precision than the human eye.
It was only a matter of time before these two technologies merged. The first Vision-Guided Robot (VGR) was a pick-and-place machine known as the programmable transfer machine. Essentially, the machine had a monochrome camera that was programmed with an algorithm that took pictures of each workpiece that it interacted with. If the piece did not match the algorithm, the piece was rejected -- the programmable transfer machine would not interact with it.
Today, VGR technology has grown far beyond the programmable transfer machine due to advances in 2D and 3D cameras, visual servo control, embedded Ethernet networks, and increasingly more sophisticated software including AI. Advances in RGBD cameras — composed of a standard RGB camera and a depth sensor — have received considerable attention lately because of their ability to quickly acquire 3D models of the environment and to estimate the camera pose in a low-cost way. Prior to RGBD cameras, other approaches to SLAM (Simultaneous Localization and Mapping) robotics relied upon laser sensors that are far more expensive.
Benefits of incorporating a vision system into an industrial robot are numerous. Empowering a robot to “see” allows it to precisely and consistently differentiate, pick, sort, move, weld or assemble various parts no matter their complexity. For instance, a multiple-step manual welding task on an automobile assembly line might take ten “blind” robots to perform since each part must be mounted in place before every weld. However, this same multi-step welding process can be done with a single VGR, since its camera can precisely align the different parts in place without human assistance.
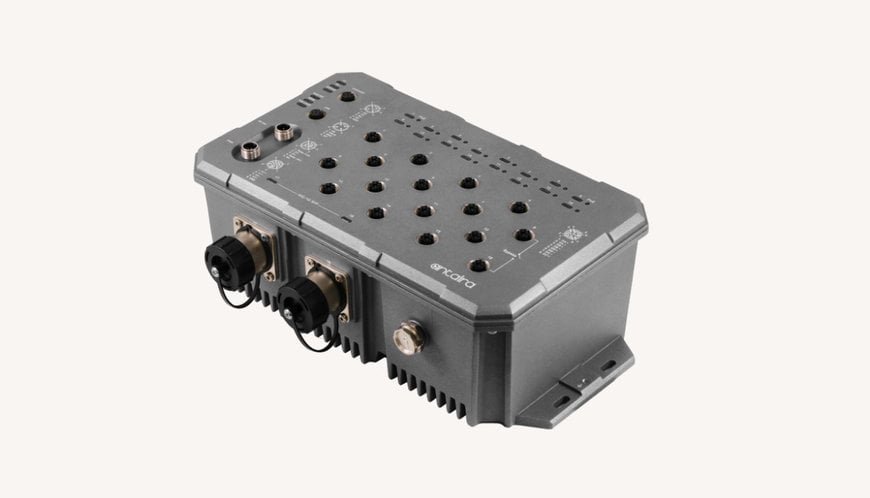
Antaira PoE M12 10 Gigabit fiber Ethernet switches are IP67 rated for harsh industrial environments including resistance to moisture, dust, vibration and shock
Flexibility is another huge benefit of VGRs. As with a machine vision system on an assembly line, a VGR uses intelligent processing to give it instructions. A slight alteration to the code allows the same robot to perform entirely different tasks, i.e., switching between products and batch runs, with no mechanical adjustments.
And then there is safety. With VGRs, factories can significantly reduce the risk of on-site accidents. To give you an idea of how that might work, consider a vision-guided forklift insidea warehouse. The automated forklift will sense obstructions along its pre-programmed paths and its movements to avoid contact with people or objects while precisely selecting items off pallets to meet customer orders.
At Amazon, for instance, robotic material handling “co-bots” (collaborative robots) safely work directly alongside humans. The Amazon Sparrow robot uses vision and a robotic arm is able to pick up a new item and deposit it on a metal chute every three seconds, handling more than 1,000 items per hour.
The Need for Ethernet Switches
To add vision to a robot, one or more cameras are needed. One is mounted on the robotic arm, serving as the machine’s eye Other cameras are installed in strategic locations in the working cell to capture more visual data. Adding these static cameras will compensate for the limitations of the arm-mounted camera.
Careful attention must be given to ensure the camera and lens has the proper resolution, frame rate, and depth-of-field required for the application at an acceptable cost. Low-cost GigE Vision cameras are preferred since they use standardized, off-the-shelf Ethernet cables and components, while eliminating the need for frame grabbers.
All this engineering takes a collaborative effort on the part of vision systems providers, robotic arm manufacturers, and robotic systems integrators. It isn’t a surprise that a major trend today is to purchase VGRs already equipped with a vision system supplied by the robot manufacturer. This translates into faster adaptation into a production line, lower costs, and more responsive technical support from a single manufacturer.
Whether the vision system is installed by the end-user or the OEM, it will require an industrial Ethernet switch to create an embedded Ethernet network within the robot. Ethernet allows the individual robot parts to communicate with each other and is suitable for VGRs because Ethernet can handle image data.
At Antaira, we manufacture managed and unmanaged high port-count Industrial Gigabit Ethernet switches for robots that make the networking of Ethernet nodes uncomplicated, even simple. Our industrial switches can be found today in robots and co-bots used in agriculture, material handling, auto manufacturing and other sectors.
Antaira Ethernet Switches
Space inside a robot is always a limiting factor. Luckily, the compact DIN-rail design of Antaira Ethernet switches allows them to fit easily next to a power supply, contactor, or relay. Power over Ethernet (PoE, PoE+, PoE++) is available on most of Antaira's industrial switches to uncomplicate the connection of cameras and other components.
In addition to multiple Gigabit Ethernet ports, Antaira’s industrial switches also offer SFP slots for fiber optic connections. Fiber is impervious to electronic noise, so the SFP slots may be useful in running long-distance communications between the robot and a remote higher-level controller. While the industrial switch’s remaining Ethernet ports are able to collect data from various components in the robotic cell.
Antaira Ethernet switches are built industrial-grade to withstand harsh manufacturing environments. Antaira’s industrial switches are housed in sturdy IP30-rated metal cases and can be trusted to handle high levels of vibration, electronic interference, and wide temperature swings.
www.antaira.com