www.ptreview.co.uk
04
'22
Written on Modified on
NEW COBOT WELDERS WITH EXTENDED RANGE TO DEBUT AT FABTECH 2022
Universal Robots has grown its welding application segment with more than 80% this year as partners develop new capabilities for the pioneering cobot welders. At FABTECH, Universal Robots’ booth will showcase new solutions from Vectis Automation and Hirebotics, enabling the weldment of larger and more complex parts.
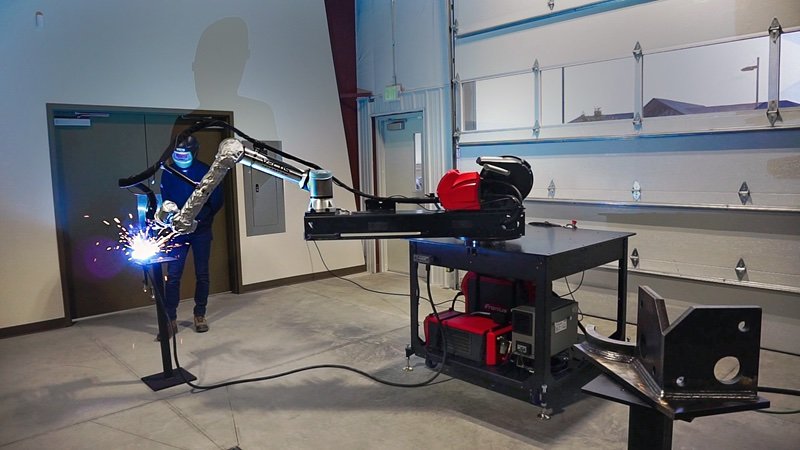
Attendees will also experience Precision Cobotics’ automated MECCO laser marking solution with Apera AI bin picking, laser welding with Cobot Systems, metal deburring with Kane Robotics, along with the new UR20 cobot in a machine tending application.
Since the first UR cobot-powered welder made its debut in North America at FABTECH 2017, a wealth of OEM partners now standardize weld solutions on the UR platform, constantly innovating their offerings. At UR’s FABTECH booth #C-11045 in Atlanta, GA, November 8-10, Vectis Automation will debut the new Park’N’Arc; a “diving board” rotational range extender that allows for the base of the cobot to be manually moved to various locations. “Compared to a short linear track, the Park’N’Arc is an improved design for increasing range as the cobot base can be translated nearly 8ft in a linear direction while maintaining simplicity, robust cable management, and portability,” says Josh Pawley, co-founder of Vectis Automation. “We’ve got a lot of customer excitement around this new product and orders are already coming in for it.”
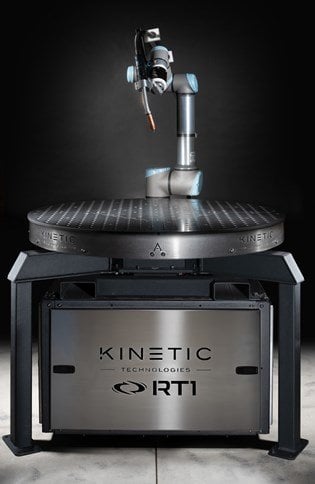
Hirebotics Cobot Welder equipped with the new indexing table, RT1 from Kinetic, will excel on handling hard-to-reach joints and products such as large frames and welded steel boxes where a cobot on a single table cannot reach fully across the part. Users can control the A/B position directly within the Cobot Welder’s Beacon software.
Another new take on welding larger parts, typically out of the cobot’s reach, will be shown by Hirebotics and partner Kinetic Technologies LLC, launching RT1, a new cobot-controlled rotary table designed to maximize welding capacity. “The need for this system is two-fold,” says co-founder of Hirebotics, Rob Goldiez. “RT1 gives customers the ability to rotate the part to the front and back for welding. Secondly, it gives users with high volume production the ability to have separate load and weld stations; loading a part on one side while the cobot is welding on the other, increasing arc on time and throughput.”
UR cobots with Apera AI handle challenging bin-picking task.
Picking unstructured parts out of bins is another traditionally challenging task to automate. At FABTECH, UR will showcase a collaboration with Precision Cobotics, demonstrating how a UR5 cobot is able to pick a shiny metal part from a randomized bin and place it into a MECCO laser marking machine. The UR5 is guided by Apera AI’s new UR+ certified Vue Vision software that accurately locates and places the part. “Robotic bin picking systems often struggle with shiny or complex objects and usually have much longer cycle times than a human performing the same actions,” says Eric Petz, head of marketing at Apera. “The Vue Vision software provides the industry’s fastest total vision cycle time—as low as 0.3 seconds— and operates under ambient light using standardized cameras, so the user does not need expensive specialized equipment.”
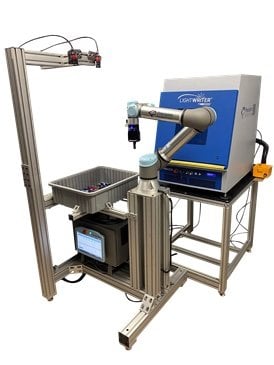
At FABTECH, Apera AI will demonstrate how its new UR+ certified Vue robotic vision software gives UR cobots human-like sight and perception, enabling them to quickly pick and accurately place parts from randomized bins. The cobot will place the part in Precision Cobotics' MECCO Laser Marking Cell capable of marking multiple materials with logos, serial numbers, barcodes and more.
Laser welding, deburring – and the new UR20
Metal fabricators visiting UR’s booth will also gain new insights from Cobot Systems, a UR Certified Systems Integrator (CSI), that has launched the first commercially available IPG LightWELD laser welder to be guided and controlled by a cobot. For deburring needs, Kane Robotics will show the GRIT™ ST-X robotic system that is ideal for sanding, grinding and finishing, using ATI’s UR+ certified Compliant Reciprocating Tool.
For the first time at a fabricating show in North America, attendees will also be able to experience the new 20kg payload cobot, the UR20 from Universal Robots that greatly expands automation opportunities such as the ability to reach further into machines, tend several machines in the same cycle, and handle 25% heavier parts than other UR cobot models. Despite being UR’s most powerful robot, the UR20 is the lightest cobot in its class, weighing only 64kg (141.1 lbs.).
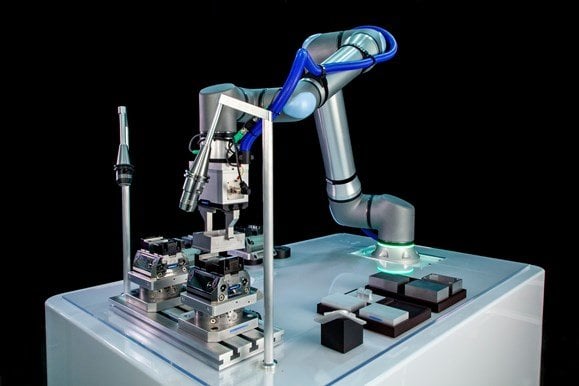
The new UR20 cobot can handle heavier loads - up to 20 kg with a greater reach of (1750 mm). It’s the lightest robot on the market in its payload and reach class, weighing only 64 kg with a small footprint (Ø 245 mm). The cobot features an all-new joint design, increasing all joint torques and TCP speed. The updated software brings smoother motion and increased uptime
“We are launching a redefined cobot that has been completely re-engineered from the ground up, focused on freeing up more manpower within a wide range of human-scale automation tasks,” says Joe Campbell, senior manager of applications development and strategic marketing at Universal Robots. “We look forward to showing fabricators the capabilities of our new cobot along with the numerous new innovative partner solutions showcased in close to 30 different application demos across our own booth and throughout the FABTECH show.”
www.universal-robots.com