Continuous and precise metering and mixing of adhesives and sealants
DOPAG adds progressive cavity pump systems for 1K and 2K materials to its product range.
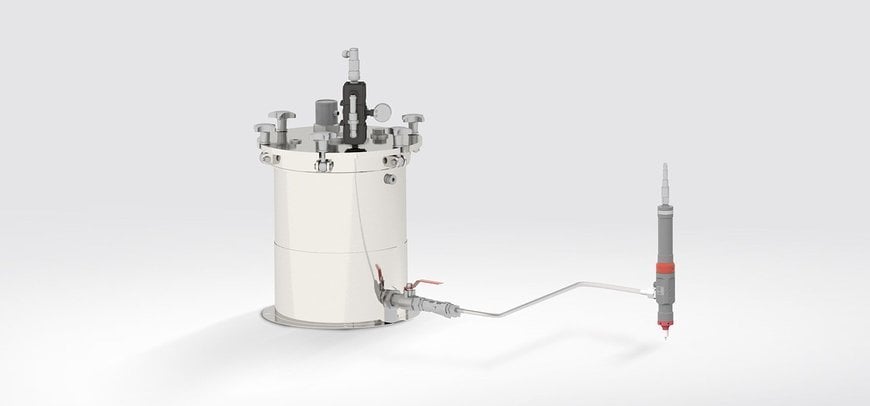
rotordis: progressive cavity pump system for processing single-component materials.
When processing adhesives and sealants, as well as epoxy resin and silicone, continuous metering is necessary for certain applications. Metering systems with progressive cavity pumps are suitable for this. These work based on the volumetric metering principle, meaning that they enable highly precise metering of the material quantity. DOPAG offers two metering systems with progressive cavity pumps:
- rotordis for processing single-component materials
- rotormix for metering and mixing mutli-component materials
Progressive cavity pumps work with no pulsation. Consisting of two components, the stator-rotor combination is the heart of the progressive cavity pump. This is a volumetric metering system that is sealed leak-free. It conveys the material continuously without any restrictions on volume, with low shear and gently in an axial direction. Progressive cavity pumps are therefore highly suitable for processing filled and abrasive materials. Rotordis and rotormix are each available in four different nominal sizes: 0.01, 0.05, 0.15 and 0.30 ml/U. Rotordis enables shot sizes from 0.002 ml (2 μl) to be processed at a discharge rate of 0.13–45 ml/min, while rotormix enables shot sizes from 0.006 ml (6 μl) to be processed at a discharge rate of 0.26–90 ml/min. In both cases, this is dependent on the viscosity and, in the case of rotormix, also on the mixing ratio. Metering precision is ± 1 per cent.
rotormix: progressive cavity pump system for processing multil-component materials
Reliable material supply
With rotordis and rotormix, materials with different viscosities can be processed, ranging from water-thin to highly viscous or pasty. Depending on the viscosity, cartridges, pressure tanks or barrel pumps can be used. With both systems, application is generally carried out directly from the metering system onto the component by means of a nozzle or mixing tube. A DC drive enables dynamic metering and a controllable back suction effect. This ensures a clean thread break at all times.
A specially developed electronic metering control unit ensures optimal adaptation of all application- specific parameters. In addition, straightforward integration into automated production processes is ensured thanks to a standardised interface.
Benefits of DOPAG progressive cavity pump systems at a glance:
- Uninterrupted metering
- Pulsation-free and low-shear
- Can convey abrasive materials
- High repeatability
- Configurable back suction effect
- Variable mixing ratio with the 2K system rotormix
- Comprehensive range of accessories available (cartridges, nozzles, plastic mixers, etc.)