www.ptreview.co.uk
20
'22
Written on Modified on
Visual components: 5 Misconceptions About Implementing Manufacturing Simulation Software Uncovered
Manufacturing simulation came to the fore in the 1990s. Early products offered two-dimensional animations, but as computer power grew, so did 3D simulation. Before long, it became one of the manufacturing industry's more practical and beneficial tools. But with its rise in prominence, simulation as a tool for manufacturers did come with its fair share of raised eyebrows and misconceptions.
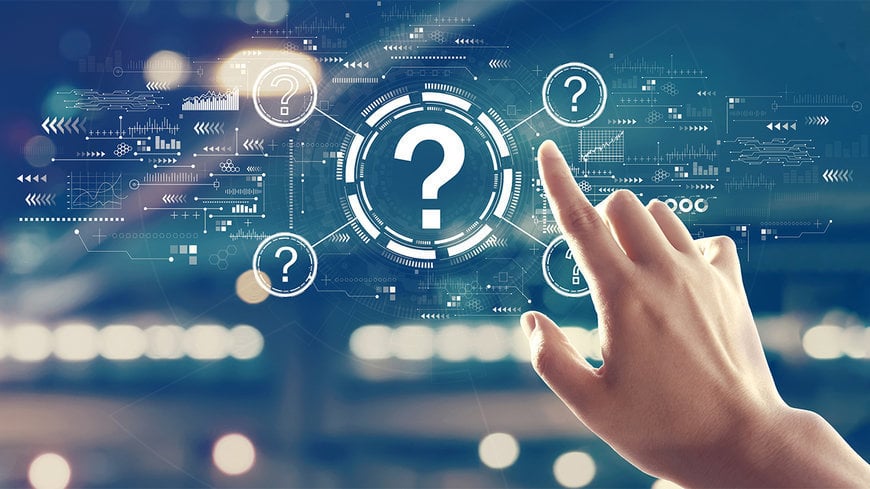
Most people understand what simulation is in its most basic form – an imitation of something – whether it be complex algorithms or virtual reality simulations recreating various real-life scenarios. But that limited understanding might lead to a lack of appreciation for using simulation in your field of expertise.
When it comes to manufacturing simulation, engineers found they could use it to model the operations of individual machines, cells and lines, and even entire factories. It was a way of investigating problems, planning new equipment installation, and exploring ways to increase output. Above all, they saw 3D manufacturing software as a tool for improving clarity when communicating ideas and, most importantly, reducing costly mistakes.
As a company with over twenty years of providing our customers with 3D manufacturing simulation solutions, we have heard a lot of myth about our industry. With that said, we feel confident in telling you that many of the problems related to 3D manufacturing simulation are mostly explained out of context by people who might not have been able to harness the true capabilities of simulation.
So, to help set the record straight, we’ll address some of the more frequently cited concerns here. Read on as we uncover five misconceptions about 3D manufacturing simulation and how anyone working in manufacturing should consider implementing simulation in one way or another.
#1 High upfront cost
“We just can’t justify paying such a high price!”
Often things take time before you can start to reap the benefits of any business solution. Training, finding specific use-cases for your business, and the resources spent to begin using the solution as efficiently as possible take considerable time and effort. That’s why, when weighing the pros and cons of any solution, you should keep in mind future opportunities.
While many simulation solutions share similarities, their features, applications, and pricing can vary. It helps to define your needs and requirements and compare your options. We find that most companies don’t need the “premium package” for their applications. Instead, they can opt for a manufacturing simulation solution that meets their needs and requirements for a much more reasonable price than they thought it would cost.
#2 Requires lots of customization
“We just don’t have the time to customize every little thing…”
When it comes to simulation software, you can go all out on customization or do minimal. Such is the case with a lot of our customers. They’ve done their due diligence and decided which of our solutions best meets their needs and requirements so that we can implement a solution for them with minimal customization. With Visual Components, you can do a lot of customization: creating your own individual components, customizing your user interface, or defining new workflows, all of which can be done with minimal or maximal customization; it’s up to you. We have a generous eCatlog, home to over 2700 ready-made components from top brands in the manufacturing industry (the likes of KUKA or ABB). This means you do not need to go through hours of painstaking 3D modelling to start using Visual Components in your workflows.
Most of our companies we work with opt for a minimal customization approach, but there is another category of companies that have a very specialized need for simulation or demand greater customization. They may require additional development work to customize existing solutions or prefer to create all-new features and solutions. The companies that fall into this category usually have a very niche application or are looking for a platform to develop white-label solutions. We’ve worked with several companies on these custom projects over the years. Still, most of our customers fall under the first category.
#3 Complexity
“It looks too confusing to me. I’ll just stick to the stuff I know.”
Simulation software might have the label as being a bit too complex for the average person to grasp their head around. But it’s essential to remember that there are multiple ends of the spectrum, as with any application – the micro and macro – the only limit is your imagination and your willingness to learn the true capabilities of 3D manufacturing simulation.
People in the manufacturing space have most likely had experience with other tools that have required years of experience to master. However, not all tools used by manufacturing professionals need a specialized degree to operate them. We can confidently make this claim about our manufacturing simulation solutions. We’ve developed solutions specifically for manufacturing design and planning teams and designed them to be used by technical and non-technical professionals. You don’t need an engineering degree or expert domain knowledge to perform many routine jobs with our software, such as configuring layouts or presenting simulations. Common sense and a little bit of practice are usually all that are required to get you going.
#4 High learning curve
“It would take us far too long to start seeing any benefits, given the time it would train someone to use the software.”
Like the previous point, a high learning curve or a perceived high learning curve can dissuade many people from using 3D simulation software before they have even started.
As the name implies, 3D simulation software like Visual Components is incredibly visual, which lends itself to the end user to better understand how our software works. If you’ve ever played a video game with drag-and-drop elements (think RTS-style games), you can start to see what we’re getting at. Dragging components into a layout can feel much the same.
Of course, things get a bit more complicated when you add more complex process modelling, robotics, human/machine interaction, etc. Therefore, we have our extensive online academy, which covers everything you would ever want to know about using our software and its use-cases.
In addition to our online academy, we have a team of Simulation Experts ready to help you whenever need a helping hand.
#5 Other systems can do the same thing
“It all seems a bit gimmicky. I’ve been able to do similar things on other CAD software.”
Altering the habits of your staff and convincing them to adopt new technologies and solutions and new ways of working can be difficult. The challenge is even greater when the belief that the systems in place are good enough.
Implementing new technologies doesn’t always go as expected, and the same can be said for implementing manufacturing simulation solutions. We have several examples of companies that completed smooth and fast implementations and were able to see immediate results from integrating manufacturing simulation into their workflows. But there are also examples of companies that didn’t have such positive experiences. This can be due to several reasons, and it’s certainly not always the customer’s fault. But we’ve generally noticed that adequate planning – before selection, purchase, and implementation of manufacturing simulation solutions – is the most critical activity that users can control to ensure a positive outcome.
Conclusion
Like we said in the beginning, over the years, we’ve heard all the possible reasons why people have strayed away from simulation. And over the years, we have noticed that many of the problems have been caused by a lack of planning, which in turn have become generalized as problems with manufacturing simulation. We hope your key takeaway from this blog post is that 3D manufacturing simulation comes in many forms and that it can be an incredibly useful tool.
Hopefully, we have shed some light on the misconception behind implementing simulation software and why you should seriously consider adding 3D simulation software into your workflows to bolster your manufacturing arsenal.
www.visualcomponents.com