www.ptreview.co.uk
14
'22
Written on Modified on
AMB 2022: ULTRATEC DEMONSTRATES THE A25 ULTRASONIC DEBURRING SYSTEM
For this purpose, the components are guided along in a process water basin upstream of a patented ultrasonic sonotrode, whose generated vibrations cause the burrs to oscillate in an energy-efficient manner and break off with sharp edges in a process-safe manner. Since July 2022, the start-up ultraTEC has been a company of the international VOLLMER GROUP from Biberach an der Riß.
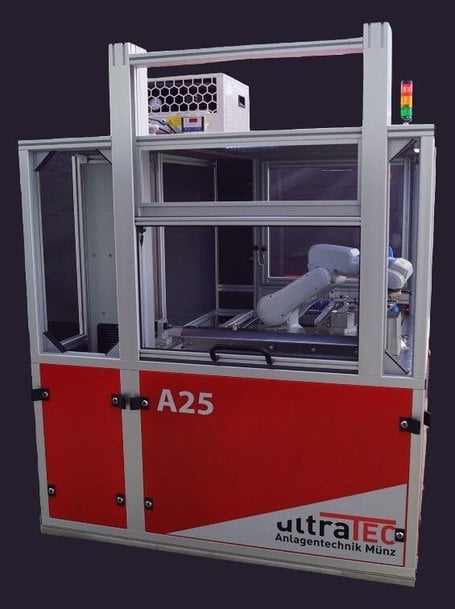
At the AMB 2022 metalworking trade show in Stuttgart, ultraTEC innovation GmbH is presenting their A25 ultrasonic deburring system. It can remove disruptive burrs or fibres from metal or plastic parts automatically and contact-free.
In all machining processes or the casting of metal and plastic parts, unwanted burrs and fibres occur at edges or cross holes. Deburring these is one of the mandatory tasks in order to make cutting edges sharp and durable or to meet hygiene requirements for implants. Currently, companies mainly deburr using manual grinding, automated ECM (electrochemical machining) processes or high-pressure waterjet deburring – but, very often, components still have to be deburred manually.
Save up to 95 percent energy with the ultrasonic process
ultraTEC innovation GmbH has developed a technology for deburring, which is based on the use of high-frequency ultrasonic sonotrodes. At the AMB 2022 metalworking trade show, the start-up, which is part of the VOLLMER GROUP, is presenting its A25 machine, which handles the deburring of components automatically and without contact. When compared to deburring with high-pressure water, the ultrasonic process requires 20 times less energy; moreover, the process water can be disposed of without any problems. . The heart of the A25 ultrasonic deburring system is a patented sonotrode that is firmly anchored in the process water tank. Stimulated by a generator, the sonotrode oscillates back and forth 20,000 times per second over 0.1 millimetres. The process allows burrs to be oscillated and removed in a process-safe manner.
A25 ultrasonic deburring system features digital control
On the A25, cutting edges or cross-drilled holes of components are guided along the tip of the sonotrode at a defined angle with the aid of an industrial robot that can operate 24/7 – the A100 ultraTEC machine for larger components also works according to this principle. For micro parts that cannot be gripped with a robotic arm, the company has developed the B10 ultrasonic deburring system. Here, the sonotrode sits on the robot arm and is guided along the component. The programming of all systems is similar to the CAM programming of milling centres and is created offline. Using IoT-based (Internet of Things) remote maintenance modules, the machine can be controlled web-based, for example, to rectify faults without an on-site service visit.
Deburring micro parts right through to 20 kilogram elements
With ultraTEC ultrasonic deburring systems, tool manufacturers and machine manufacturers can also gently deburr sensitive surfaces. The targeted process control enables selective deburring on individual edges or holes. The range of
components to be machined extends from microparts for the optics or watchmaking industry, and precision tools for machining, right through to 20-kilogram elements of the kind required in mechanical engineering or vehicle construction. "We want to use this year's AMB to demonstrate to interested parties, live, the process of ultrasonic deburring," says Dieter Münz, CEO of ultraTEC innovation. "Our A25 ultrasonic deburring system in particular stands out not only thanks to its precision, non-contact and energy efficiency, but also thanks to its automated processing around the clock."
www.vollmer-group.com