www.ptreview.co.uk
05
'22
Written on Modified on
NSK trains production staff using VR technology
Operators of high-precision grinding and honing machines in NSK's ball bearing production are now taking advantage of virtual reality (VR) training methods. VR technology has the advantage, among other things, of allowing machines to keep producing, while simultaneously permitting easier standardisation of training courses. For NSK, this first project at its Munderkingen plant in Germany serves as a model for future roll-out at other facilities.
In the production of high-quality ball bearings, machining accuracy requirements are extremely high, which is why NSK’s production sites make use of special high-precision grinding and honing machines. The challenge is to keep these machines running 24/7, while at the same time training employees in their operation.
NSK, working in partnership with Varity.me, has found the solution to this challenge in VR technology: no more production interruptions are necessary to carry out training sessions because they now take place interactively in the virtual space. In addition, it is possible to hold the training in a decentralised location as small as 2 m2.
One of the advantages of this type of training is that each operator learns how to set up the machine in the same way whenever switching over to the next product. At the Munderkingen plant, set-up workflows are especially important because the plant produces a wide variety of customer-specific bearing types in small batches, requiring frequent machine set ups.
VR-supported training of the set-up process establishes a standard procedure, which reduces cycle time errors, scrap rates and quality deviations. Importantly, operators can repeatedly practice and improve their set-up skills without having to dismantle the machine each time.
Carsten Schleyer, responsible for the project at NSK in Munderkingen, cites another advantage: "The time required for training sessions in the virtual space is often only a third of that required for conventional training, largely because VR training can focus purely on procedures without having to handle real tools and workpieces."
In practice, it quickly became apparent that VR could offer additional advantages to NSK that go far beyond training requirements. For example, consider a machine which is still be under development at the manufacturer. It is possible to install this machine in the virtual space and train employees on it. Set-up procedures can be analysed and optimised using the digital model of the machine. Operators can then make suggestions for optimising the set-up procedures, and even transmit their feedback and proposals directly to the machine’s developers, who can perhaps make adjustments accordingly.
Another advantage of having a digital machine model in the virtual space is the ability to view it from every conceivable angle. This capability can benefit repair and maintenance staff, for example, who can look inside the virtual machine and develop a plan for replacing components.
NSK’s management team sees this project as a good example of how digitalisation not only delivers expected benefits, but also reveals potential in other areas.
"Having a model of a grinding or honing machine in the virtual space not only makes employee training easier, it also helps with the operation and maintenance of the actual machine,” confirms Carsten Schleyer.
Project implementation at NSK's Munderkingen plant took place with co-operation from Varity.me, an interdisciplinary team from Modellfabrik Bodensee GmbH. Varity.me has developed its own software, Varity SDK, for developing interactive training courses in the virtual space quickly and easily.
NSK, working in partnership with Varity.me, has found the solution to this challenge in VR technology: no more production interruptions are necessary to carry out training sessions because they now take place interactively in the virtual space. In addition, it is possible to hold the training in a decentralised location as small as 2 m2.
One of the advantages of this type of training is that each operator learns how to set up the machine in the same way whenever switching over to the next product. At the Munderkingen plant, set-up workflows are especially important because the plant produces a wide variety of customer-specific bearing types in small batches, requiring frequent machine set ups.
VR-supported training of the set-up process establishes a standard procedure, which reduces cycle time errors, scrap rates and quality deviations. Importantly, operators can repeatedly practice and improve their set-up skills without having to dismantle the machine each time.
Carsten Schleyer, responsible for the project at NSK in Munderkingen, cites another advantage: "The time required for training sessions in the virtual space is often only a third of that required for conventional training, largely because VR training can focus purely on procedures without having to handle real tools and workpieces."
In practice, it quickly became apparent that VR could offer additional advantages to NSK that go far beyond training requirements. For example, consider a machine which is still be under development at the manufacturer. It is possible to install this machine in the virtual space and train employees on it. Set-up procedures can be analysed and optimised using the digital model of the machine. Operators can then make suggestions for optimising the set-up procedures, and even transmit their feedback and proposals directly to the machine’s developers, who can perhaps make adjustments accordingly.
Another advantage of having a digital machine model in the virtual space is the ability to view it from every conceivable angle. This capability can benefit repair and maintenance staff, for example, who can look inside the virtual machine and develop a plan for replacing components.
NSK’s management team sees this project as a good example of how digitalisation not only delivers expected benefits, but also reveals potential in other areas.
"Having a model of a grinding or honing machine in the virtual space not only makes employee training easier, it also helps with the operation and maintenance of the actual machine,” confirms Carsten Schleyer.
Project implementation at NSK's Munderkingen plant took place with co-operation from Varity.me, an interdisciplinary team from Modellfabrik Bodensee GmbH. Varity.me has developed its own software, Varity SDK, for developing interactive training courses in the virtual space quickly and easily.
1) VR machine training at NSK's Munderkingen plant delivers a number of important advantages (Photo: NSK Munderkingen)
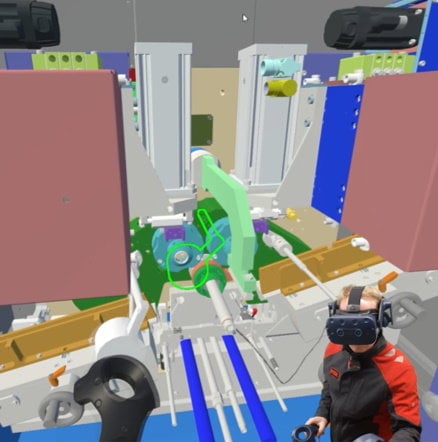