www.ptreview.co.uk
05
'22
Written on Modified on
MAN AND ROBOT HAND IN HAND
Automation solutions have been an integral part of the world's factories for decades. And the trend is rising: handling systems move components from one operation to the next, they assemble smartphones, weld car bodies and take care of loading and unloading machines. There are hardly any limits to the imagination anymore. Everything seems possible. But not everything makes sense.
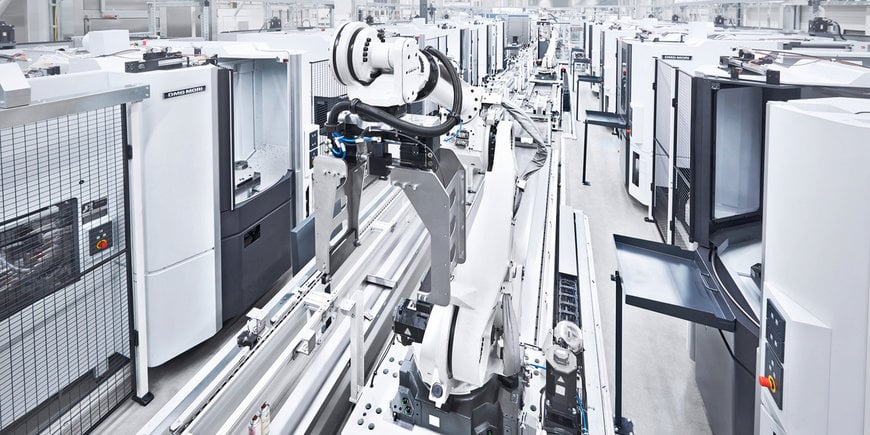
Two decisive factors in this consideration are, on the one hand, the complexity of the handling task and, on the other hand, the number and variance of the components or workpieces to be manufactured. And it is precisely here that solutions from the field of human-robot collaboration are pushing the boundaries.
The pleasant thing about automation systems is that they precisely follow the tasks and paths set for them by humans. And until recently, they did so exclusively "blindly" and "numbly". What was programmed was done. Come what may…
To safely prevent pre-programmed collisions, especially those with humans, automation was condemned to being alone; secured by high protective fences and light barriers. Safety was and is the highest priority. However, the restricted freedom rights for robots & co also led to restriction in their application. "Human safety has limited the efficiency of machines," describes the Fraunhofer Institute for Cognitive Systems IKS, for example.
But times are changing dynamically — today, intelligent sensors and modern image processing systems, with increasingly powerful computing technologies, are ensuring that automation is becoming more collaborative. Fraunhofer IKS is researching precisely such collaboration solutions. In their target image, humans and robots should be able to interact directly in the same workspace without restrictions. The institute distinguishes between four different levels of this "interaction". The lower levels describe the strict separation of work areas or mere coexistence and spatial demarcation. Only in the context of so-called cooperation do humans and robots work on a product not simultaneously, but already time-shifted in the same workspace. At the highest level of collaboration, they really do interact with each other as colleagues.
Safety continues to be a top priority
In its position paper "Safety in human-robot collaboration", the German Engineering Federation (VDMA) describes the protective measures that must be taken to ensure that employees are not put at risk.
The VDMA lists the following principles:
- safety-oriented monitored standstill: robot stops when the employee enters the shared workspace and continues to move when the employee has left the shared workspace again.
- manual guidance: robot movement is actively controlled by the worker using appropriate equipment.
- speed and distance control: contact between employee and robot in motion is prevented by the robot.
- power and force limitation: contact forces between employee and robot are technically limited to a non-hazardous level.
If the cooperation between humans and robots is cleverly designed, the efficiency of a production can be significantly increased. A working environment in which both humans and robots can move more freely gains flexibility and allows more flexible production. Both are essential considering the increasing degree of individualization and ever smaller batch sizes in almost all industries.
In addition, the workload of employees is reduced. Robots can — literally — take the strain off people. This is already happening in the automotive industry, where humans assemble heavy components together with collaborating robots. Figuratively speaking, this collaboration applies to many areas of automation — whenever personnel can trust automated processes and contribute their expertise precisely where machines will be inferior for a long time to come.
Collaboration between humans and Robo2Go
DMG MORI also makes use of interaction possibilities between humans and robots when designing manufacturing solutions. The goal is always the best possible manufacturing process. In the case of small and medium batch sizes, Robo2Go has proven itself as a tried and tested automation solution. Thanks to predefined program modules, it can be taught within 15 minutes without any knowledge of robot programming. Robo2Go also marks the start of human-robot collaboration.
The innovative solution already offers a flexible automation layout with free access to the machine and an intelligent safety concept as standard. In this case, absolute safety ensures a laser scanner that monitors the working radius of the robot and stops its movement immediately as soon as the working area is entered.
Beyond the standard, the Robo2Go Vision also offers an intelligent image recognition system so that the system can be equipped with, among other things, Euro pallets. A 3D camera recognizes the robot the raw part position takes place the loading and unloading in the automated sequence without specific workpiece deposits from.
The Robo2Go variants are available for turning centers of the CLX, CTX alpha and CTX beta TC series as well as for the DMU 50 3rd Generation in the area of 5-axis simultaneous milling.
www.dmgmori.com
In addition, the workload of employees is reduced. Robots can — literally — take the strain off people. This is already happening in the automotive industry, where humans assemble heavy components together with collaborating robots. Figuratively speaking, this collaboration applies to many areas of automation — whenever personnel can trust automated processes and contribute their expertise precisely where machines will be inferior for a long time to come.
Collaboration between humans and Robo2Go
DMG MORI also makes use of interaction possibilities between humans and robots when designing manufacturing solutions. The goal is always the best possible manufacturing process. In the case of small and medium batch sizes, Robo2Go has proven itself as a tried and tested automation solution. Thanks to predefined program modules, it can be taught within 15 minutes without any knowledge of robot programming. Robo2Go also marks the start of human-robot collaboration.
The innovative solution already offers a flexible automation layout with free access to the machine and an intelligent safety concept as standard. In this case, absolute safety ensures a laser scanner that monitors the working radius of the robot and stops its movement immediately as soon as the working area is entered.
Beyond the standard, the Robo2Go Vision also offers an intelligent image recognition system so that the system can be equipped with, among other things, Euro pallets. A 3D camera recognizes the robot the raw part position takes place the loading and unloading in the automated sequence without specific workpiece deposits from.
The Robo2Go variants are available for turning centers of the CLX, CTX alpha and CTX beta TC series as well as for the DMU 50 3rd Generation in the area of 5-axis simultaneous milling.
www.dmgmori.com